In the last publication, we wrote about reducing energy costs in a production plant. In this article, we continue this thread by focusing on electricity. From the reading you will learn how to easily and without large investments relieve your company’s budget without transferring costs to customers.
1. INCREASING ELECTRICITY PRICES
In the era of rising charges for CO2 emissions, the need to modernize outdated transmission networks and build new power units, it is obvious that these costs are passed on directly to electricity consumers. Many companies (perhaps yours as well?) are already experiencing a sudden increase in costs.
Recent contracts with rates in the range of PLN 220-240/MWh are expiring, and the new prices are shocking, reaching the level of PLN 1000-1200 /MWh and more.
The cost of electricity is starting to burden the budgets of manufacturing companies more and more.
Many managers are faced with a dilemma – transfer costs to customers or optimize electricity consumption? At this point, it is worth asking yourself – is the customer willing to pay? Usually not. Whatever you produce, if the prices of your products rise as your energy bills increase, you become less competitive. Therefore, it is worthwhile to start implementing the consumption optimization process instead of passing the costs on to the customer. Ultimately, you will profit from it!
2. Identify unnecessary energy consumption
We know from experience that energy is most often wasted in production plants by:
1. Inefficient use of lighting, heating and air conditioning systems.
2. Leaving machines and other devices turned on during production breaks (weekends, holidays).
3. The use of ineffective and energy-consuming machines – no ongoing analyses in terms of the need for modernization.
4. Improper production planning – machines running for many hours in the production standby mode, without actual production.
5. Improper use of machines by operators – using “own” settings and recipes without consulting the technology departments.
6. Long-term operation of damaged machines and consumption of excessive amounts of energy during this time (worn-out bearings, damaged gears, etc.).
Losses generated as a result of all the above wastes can be counted in thousands, tens, and in extreme cases even hundreds of thousands of PLN a year.
Often, a problem is also the adopted method of allocating the costs of electricity used to individual technological processes. Without access to actual measurement data, an analysis based on summing the installed power and the percentage division of energy consumption depending on this indicator is applied. This is the mistake that most often leads to misconceptions about the actual allocation of costs. Machines with a high installed power, with a low production load, may use less energy than equipment with a lower installed power, but with a high use of the time available for production.
In such a situation, the data from the installed measuring systems are useful, which may be located in the main switching stations, at the power supply approaches to the machines, or at other points (depending on the topology of the power grid). There are several leading suppliers of such equipment on the market, however, most of them only offer the possibility of accumulating and reading data directly (optionally: via cables, via dedicated applications, via the WWW). Moreover, these data do not have the appropriate resolution – you can only see the total value of the kwh/kVar counter, possibly instantaneous or daily values. This is not enough to draw broader conclusions that will optimize production processes and reduce energy consumption.
3. Merely collecting data is not enough
However, we have good news. You can connect to most of the measuring devices via MODBUS RTU/TCP IP or other protocols. Thanks to this, you can connect them with the IPLAS system which will read, import and then automatically process the data with the resolution you need: every hour, minute, second. Instead of a huge number of tables and numbers, you will be able to use transparent visualizations that will help you draw quick and accurate conclusions – hence the easy way to optimize energy consumption.
Losses that can be easily avoided
Let's use an example.
The company X has a furnace for heating elements. The device is turned on 365 days a year. During operation, the temperature in it is around 600 degrees Celsius, and on weekends it is lowered to 300 degrees Celsius (power-off/standby mode). The machine is programmed by the operators so that every Monday at 6.00 am it is ready to work, so already from 4.00 am it gradually increases the temperature from 300 to 600 degrees.
At a temperature of 300 degrees (idle), the machine consumes about 200kW.
At 600 degrees, the consumption increases to around 350kW.
Due to the specificity of production and the planning process, not every Monday the operators have work orders. They often wait until 11 o’clock for new orders to be issued.
It follows that for 5 hours the machine consumes approximately 750kwh of energy. Assuming that there may be 20 such weeks in a year, the company loses 15,000kwh, i.e. almost PLN 15 000 -18 000 (averaging very much).
4. Energy waste , which you can avoid
Now let’s get to the point. We already have energy meters installed and access to them via ETHERNET. The devices were programmed in accordance with the manufacturer’s instructions (in our case, SOCOMEC).
Will data import to the IPLAS system be complicated?
No! We have created an automatic configurator of such connections, which will guide you through the entire process of preparing for data collection step by step. Thanks to this, the implementation will be trouble-free and instant. Not believing? Read below a recommendation from one IPLAS user or take a look for short instructions at iplas.pl/ Szybki-konfigurator.
Below is a simple instruction on how to do this:
On the Installations menu, click Quick Setup. If there is no defined installation, the following information will appear: Watch our guide which will tell you how to add installations and how to download and install the Gateway module.
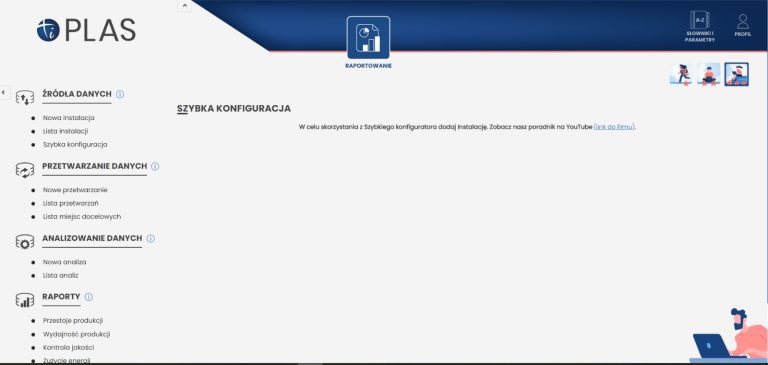
In the next step, you can define the name for your report and select the device manufacturer:
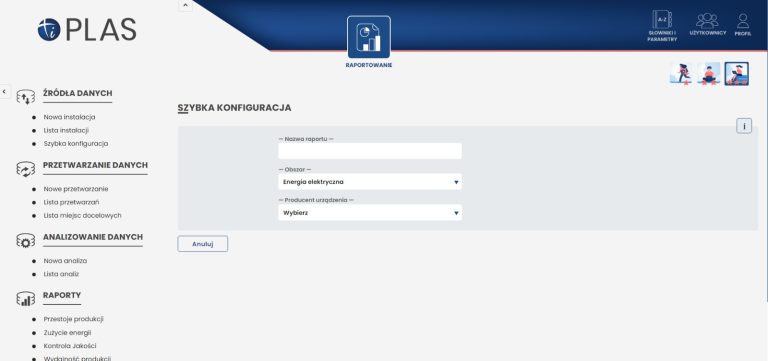
Then select the manufacturer and indicate the installation in which the new communication channel is to be added:
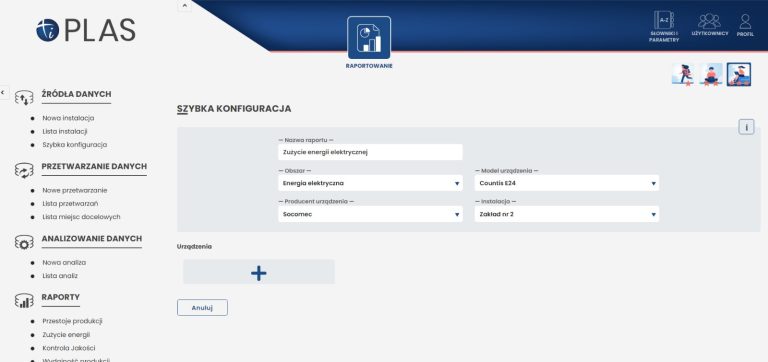
In one report, up to four devices can be added for which you will enter parameters in the same way as you did in the previous step. Add a device by clicking +
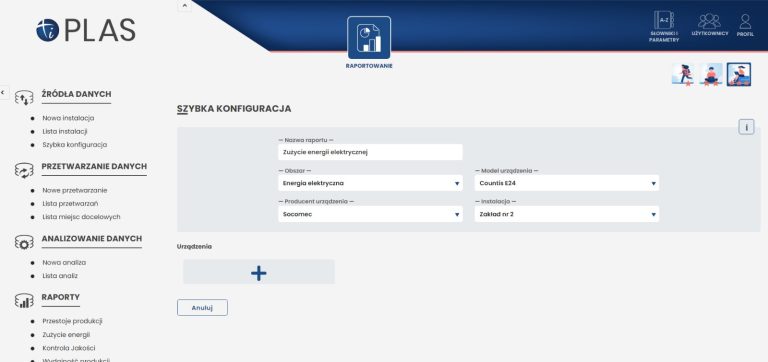
In the last step, enter the parameters of your device:
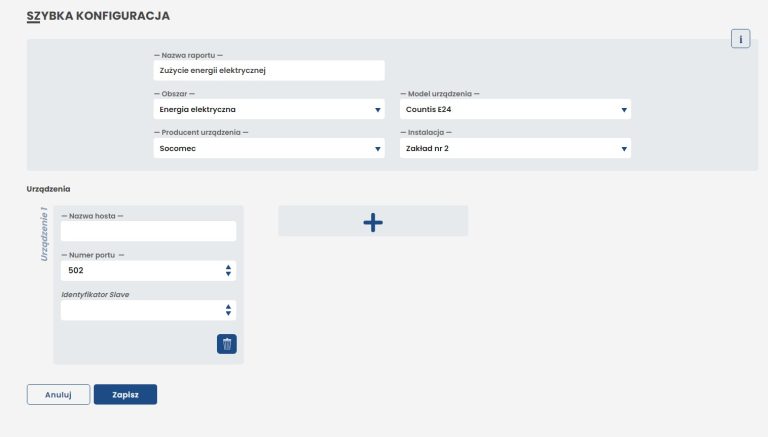
You will finish the configuration by clicking the Configure button. Then, you will be transferred to the report that has been created.
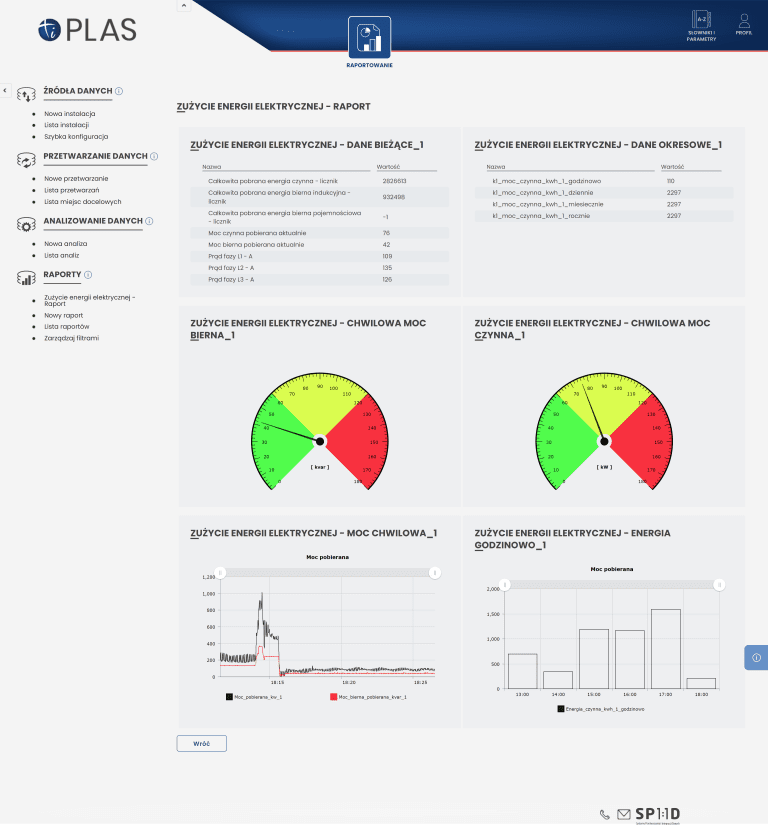
From now on, the system will collect data that you will be able to use in order to create more advanced reports. You will quickly detect sources of needless energy consumption, you will be able to take the right steps to optimize production and … you will immediately notice it in your reports!
Would you like to see What is IPLAS?
Call or write to us and tell us about your problems and the needs of your company!