Introduction
It is no secret that manufacturing plants consume enormous amounts of electricity. Utility bills in many companies devour from several to even dozens of percent of operational budgets. Managing a company’s finances is also not made easier by the constantly rising energy prices. Taking into account the factors mentioned, optimizing energy consumption in production becomes more important than ever. So where to look for savings sources? Is a change in the structure and specifics of the manufacturing plant’s operations necessary to reduce utility bills? If you have no idea how to find the right source of savings, a continuous monitoring system will be invaluable help.
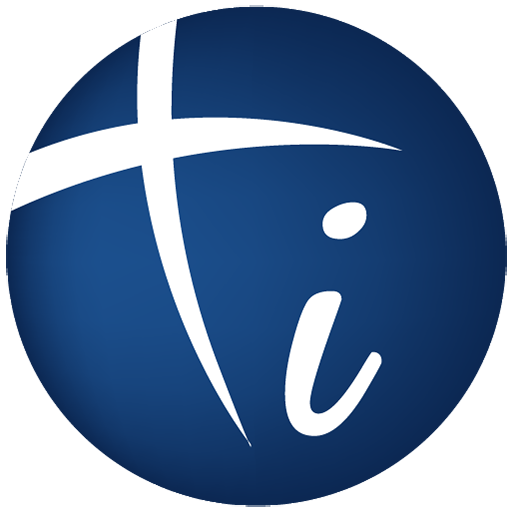
Regardless of the products or services a particular industrial plant offers, energy consumption in such facilities reaches substantial levels. Various machines, cooling installations, and quality lighting are just some of the factors that contribute to high bills. Learn more about the basic terms associated with energy consumption in a company.
Definition of Energy Consumption
Electrical energy consumption in production refers to the amount of electrical energy used by a company or manufacturing plant to produce its products or provide services. It is a measure of the amount of electricity needed to power machines, devices, and production processes.
In analyzing electricity consumption in production, it’s essential to determine how much energy exactly is needed to produce a unit of product or conduct a particular operation. This helps companies identify areas where they can save energy or optimize production processes.
Role of Electrical Energy in Production
Electric power plays a key role in production, serving as a driving force for machines and devices used to manufacture products. It’s like the heart of the production process, enabling the movement of production lines, tool rotation, welding, cutting, and many other operations. With electrical energy, factories operate efficiently, effectively, and according to defined quality standards, which translates into the overall effectiveness of the enterprise.
Methods of Analyzing Energy Consumption
By optimizing energy consumption, companies can not only effectively reduce operating costs but also increase the reliability of machines and other devices. Various methods analyze energy consumption in manufacturing plants. Choosing the right strategy for your business is the first step in a process aiming to identify savings sources.
Manual Data Analysis
Manual data analysis regarding energy consumption is one of the basic methods used to study energy efficiency in a production plant. As the name suggests, it involves traditional manual data collection, input, and analysis concerning energy consumption at different production stages.
The undeniable advantage of this approach is its accessibility. There’s no need to implement advanced systems or specialized software, so this method can be used even in small plants.
However, manual data analysis has several significant drawbacks. The first is a high risk of making an error. An employee typically conducts the analysis. Even the most diligent and hardworking individual can make mistakes affecting the accuracy of results upon which budget-related decisions are made.
Additionally, it’s impossible for an employee to collect data around the clock. Monitoring usually takes place at specific hours, which might overlook significant changes in energy consumption. The financial aspect should also be considered – the annual costs of employing a person certainly exceed the expenses associated with an automatic data acquisition system.
Automatic Monitoring Systems
Automatic monitoring systems, for example, the IPLAS system, are a modern method of analyzing energy consumption in a company. Such solutions utilize advanced sensors, energy meters, and comprehensive software to collect, process, and analyze data on energy consumption in a manufacturing plant.
Automating the energy consumption analysis process brings many benefits. Above all, monitoring conducted with systems is extremely precise. With real-time information, plant owners can quickly respond to changes in energy consumption, identifying potential issues and making necessary adjustments.
Modern systems are designed with the comfort and time of managers in mind. Therefore, collected data is presented in the form of charts, tables, or other visualization forms, eliminating the need to waste resources on information interpretation.
Given that automatic monitoring systems are comprehensive solutions, they initially require more significant financial outlays than manual methods. To create a system tailored to a plant’s needs, a detailed audit of the company’s current situation is necessary, which additionally affects the cost of the project. However, it’s worth noting that monitoring systems are a form of investment. Modern solutions quickly provide accurate data, allowing the entrepreneur to identify savings sources. Besides, implemented solutions remain in the plant for a long time, allowing efficient savings search.
Using IoT Technology for Data Collection
If you want even more precise data collection regarding energy consumption, it’s worth considering using the Internet of Things (IoT) technology. It involves connecting various devices and sensors to the internet, enabling remote access and data monitoring.
Using IoT technology is an excellent solution for those focused on comprehensive production management optimization, not just collecting energy consumption data. IoT can be integrated with other systems monitoring every area of the production plant. This eliminates the weakest and least profitable links, facilitating additional savings.
Energy Consumption Optimization Strategy
A well-thought-out energy consumption optimization strategy should primarily be based on reliable data obtained as a result of monitoring electricity consumption at every production stage. Based on this information, areas of excessive energy consumption can be identified. With this knowledge, owners can implement actions aimed at reducing energy losses.
Another factor in an effective strategy is advanced technologies, e.g., automation and control systems. These innovative solutions allow optimizing machine and device operations by adjusting their work depending on current production conditions. This prevents unnecessary energy consumption during periods of low production activity.
Regular technical reviews of all machines and devices used in the industrial plant are also crucial. Every breakdown results in downtime, generating losses for the company. Production monitoring systems analyze the condition of all devices, and if any irregularities are detected, they indicate in the generated report that a review of a specific part or the entire machine is necessary. Regular technical reviews and maintaining devices in good technical condition are key factors in minimizing energy losses resulting from malfunction or suboptimal machine operation.
Electricity Consumption Monitoring System (IPLAS)
The comprehensive IPLAS electrical energy production and consumption monitoring system is a solution that will modernize your facility. With this advanced tool, you will have constant access to the most important data, which we will define together at the very beginning of our collaboration.
The IPLAS system not only collects and processes key information about your business but, crucially, presents it in clear visualizations. Whether it’s a table, a chart, or a synoptic map, you decide how the data should be displayed. With intuitive visualization, you can quickly make the right decisions to improve the production processes in your factory.
In the visualizations created by the IPLAS system, you will also have constant access to all the sources consuming electrical energy. Monitoring this data 24/7 ensures transparency and reliable information, based on which you can effectively identify the devices and areas in your facility that contribute the most to significant bills.
+48 883 366 717