Wstęp
Zakłady produkcyjne muszą liczyć się z perspektywą wielu wyzwań, z którymi prędzej czy później się zmierzą. Jednymi z najczęściej pojawiających się problemów w każdej hali produkcyjnej są awarie i usterki maszyn oraz innych sprzętów będących częścią linii produkcyjnej. Niestety tego typu nagłe sytuacje niemalże zawsze oznaczają straty dla przedsiębiorstwa. Firma musi zainwestować środki w naprawę wszystkich uszkodzeń, a każdy dodatkowy dzień przestoju oznacza kolejne, ogromne koszty dla przedsiębiorcy.
A gdyby tak móc przewidzieć ewentualne awarie i nie dopuścić do ich pojawienia? Tak, to możliwe! Przeczytaj nasz dzisiejszy wpis blogowy i dowiedz się, w jaki sposób uniknąć przestojów w Twoim zakładzie!
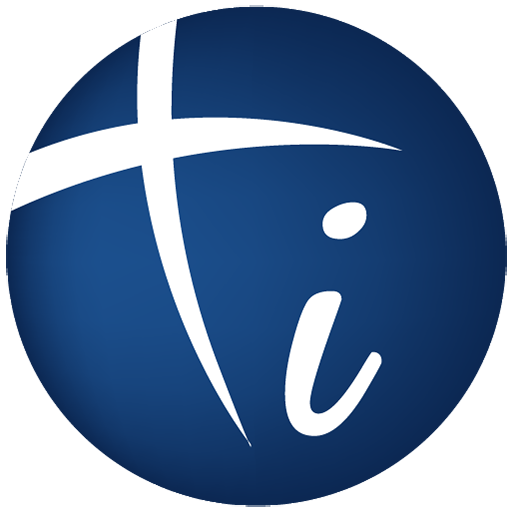
Dlaczego awarie i przestoje są problemem?
Każda awaria czy przestój to problem dla zakładu produkcyjnego z jednego, bardzo prostego powodu – ze względu na koszty. To nieplanowany wydatek, który dodatkowo obciąża firmowy budżet. Naprawa awarii to nie tylko środki przeznaczone na jej usunięcie, ale również stracony czas pracowników i ich niższa wydajność przez okres przestoju. Jakie są najpoważniejsze konsekwencje przestojów na linii produkcyjnej?
Spadek efektywności produkcji
Awarie i przestoje wyraźnie wpływają na efektywność procesu produkcyjnego. Każda przerwa w produkcji oznacza stratę czasu, który mógłby być wykorzystany do wytwarzania produktów. To oznacza mniej wyprodukowanych jednostek w określonym czasie, co z kolei prowadzi do obniżenia efektywności produkcyjnej.
Wzrost kosztów
Naprawy maszyn to koszty, z którymi trzeba się liczyć w obliczu przestojów. Należy uwzględnić koszty naprawy, zużycie materiałów i czasu pracowników zaangażowanych w usuwanie awarii. Ponadto awarie mogą prowadzić do konieczności zakupu nowych części lub maszyn, co zwiększa koszty ponoszone przez przedsiębiorstwo.
Niezadowolenie klienta
Przerwy w produkcji często prowadzą do opóźnień w dostawach. To z kolei może sprawić, że klienci otrzymają produkty później niż obiecano, co negatywnie wpłynie na ich opinie o firmie. Klienci oczekują terminowej dostawy, a awarie i przestoje mogą to skutecznie zakłócić, przez co cierpi reputacja przedsiębiorstwa.
Obniżenie rentowności firmy
Wszystkie powyższe czynniki sumują się, wpływając na ogólną rentowność firmy. Mniejsza liczba wyprodukowanych towarów, wyższe koszty i niezadowolenie klientów prowadzą do mniejszych zysków. Długotrwałe problemy z awariami mogą nawet zagrozić przetrwaniu firmy na rynku.
Jakie są główne przyczyny awarii i przestojów na produkcji?
Awarie i przestoje na linii produkcyjnej mogą mieć różne źródła. Identyfikowanie głównych przyczyn takiego stanu rzeczy jest kluczowe w zapobieganiu niechcianym sytuacjom. Jakie są główne czynniki prowadzące do awarii na produkcji?
- Błędy ludzkie – pracownicy są narażeni na popełnienie błędów, które mogą prowadzić do awarii maszyn. Nieuwaga, brak szkoleń, czy nieprzestrzeganie procedur bezpieczeństwa powodują wzrost ryzyka uszkodzenia sprzętu.
- Zużycie sprzętu – maszyny i urządzenia używane na produkcji ulegają naturalnemu zużyciu. Brak regularnej konserwacji, przeglądów, bieżącego utrzymania oraz przekroczenie granic wydajności maszyn może prowadzić do ich awarii, czego skutkiem będą przestoje na produkcji.
- Braki w utrzymaniu ruchu – systematyczna konserwacja i utrzymanie ruchu maszyn są nieodzowne. Brak planów konserwacyjnych, nieodpowiednie smarowanie, czy ignorowanie sygnałów ostrzegawczych zwiększa ryzyko awarii. Warto do tematu podejść proaktywnie i zawczasu zaplanować strategię prewencyjną, której podstawą będzie wcześniejsze reagowanie oraz odpowiednie dbanie o park maszynowy.
- Problemy z dostawami – awarii można uniknąć, biorąc pod uwagę dostępność niezbędnych materiałów i części zamiennych. Zawsze warto kontrolować stan maszyn i odpowiednio wcześniej przeprowadzić prace konserwacyjne lub wymienić przestarzałe, czy zużyte elementy.
- Kwestie organizacyjne – słabe zarządzanie produkcją, nieefektywne planowanie, czy brak komunikacji między różnymi działami mogą doprowadzić do chaosu na linii produkcyjnej.
Jakie narzędzia i metody mogą pomóc w identyfikacji i monitorowaniu awarii i przestojów?
Efektywne identyfikowanie i monitorowanie awarii oraz przestojów na linii produkcyjnej to klucz do zwiększenia wydajności i obniżenia kosztów. Istnieje wiele narzędzi i metod, które mogą skutecznie wesprzeć właścicieli zakładów produkcyjnych w tym procesie. Z jakich technologii można, a nawet powinno się korzystać, aby skutecznie zminimalizować ryzyko wystąpienia przestojów na linii produkcyjnej?
Pierwszy system, z którym warto się zapoznać, to system MES (Manufacturing Execution System). System MES to zaawansowane oprogramowanie, które pozwala na zarządzanie produkcją, zbieranie danych produkcyjnych w czasie rzeczywistym oraz monitorowanie efektywności produkcji. Dzięki MES można śledzić pracę maszyn, zarządzać zapasami i monitorować przestoje.
Doskonałym uzupełnieniem do systemu MES jest system TPM (Total Productive Maintenance). To innowacyjne podejście do zarządzania utrzymaniem ruchu maszyn, które ma na celu zapobieganie awariom i utrzymanie maszyn w jak najlepszym stanie. Taka strategia obejmuje regularne konserwacje, szkolenia pracowników i dbałość o stan techniczny maszyn.
Wyżej wymienione rozwiązania to systemy, które możesz wdrożyć u siebie w zakładzie produkcyjnym. Jednak, aby móc z nich korzystać niezbędny jest ich zakup. Dlatego, jeśli nie masz odpowiednich środków, warto wdrożyć pewne metody, dzięki którym już od jutra będziesz mógł skutecznie zmniejszyć ryzyko wystąpienia awarii.
- Analiza przyczyn i skutków (FMEA – Failure Mode and Effects Analysis) – FMEA to metoda analizy, która pomaga zidentyfikować potencjalne awarie, określić ich przyczyny i skutki oraz ustalać priorytety działań zapobiegawczych. Jest to skuteczne narzędzie do minimalizowania ryzyka awarii.
- 5 Whys – metoda „5 Whys” polega na wielokrotnym zadawaniu pytania „dlaczego” w celu zidentyfikowania źródła problemu. Ta prosta, ale skuteczna metoda pomaga głębiej zrozumieć przyczyny awarii.
Jakie praktyki i strategie można wdrożyć, aby zminimalizować awarie i przestoje?
Utrzymanie ruchu na linii produkcyjnej to jeden z najważniejszych celów każdego managera lub kierownika hali produkcyjnej. W związku z tą czynnością warto wykonywać szereg zadań prewencyjnych, tak aby nie dopuścić do przestojów w procesie produkcyjnym. Jakie są kluczowe elementy strategii predykcyjnej w zakładzie produkcyjnym?
- Regularne przeglądy i konserwacja parku maszyn – każda maszyna znajdująca się w hali produkcyjnej powinna być regularnie sprawdzana pod kątem ewentualnych części wymagających wymiany. Takie podejście minimalizuje ryzyko wystąpienia awarii, dzięki czemu firma może zaoszczędzić ogromne kwoty.
- Szkolenia dla pracowników – osoby odpowiedzialne za utrzymanie ruchu na linii produkcyjnej powinny ciągle rozwijać swoje umiejętności i poznawać nowe, bardziej zaawansowane metody wspierające ich w codziennym wykonywaniu obowiązków. Jeśli chcesz iść z duchem czasu i stale udoskonalać procesy produkcyjne, kluczową kwestią są szkolenia dla pracowników.
- Inwestycje w nowoczesne technologie – każdy przedsiębiorca powinien zdawać sobie sprawę z tego, że korzystanie z innowacyjnych systemów zwiększa konkurencyjność zakładu na rynku. Systemy takie jak MES czy TPM umożliwiają pobieranie i analizowanie danych w czasie rzeczywistym, dzięki czemu kierownicy i managerowie mogą podejmować ważne, biznesowe decyzje na podstawie rzetelnych informacji.
- Praca nad komunikacją pomiędzy pracownikami na linii produkcyjnej – efektywnie prowadzona komunikacja zarówno między pracownikami w jednym zespole, jak i pomiędzy działami to niezwykle ważny aspekt, nad którym warto ciągle pracować. Im lepiej będzie przebiegała wymiana informacji wśród pracowników, tym mniejsze ryzyko popełnienia błędu wynikającego np. z nieznajomości najnowszych ustaleń.
- Tworzenie planów awaryjnych – kluczowym celem tworzenia planu prewencyjnego jest zminimalizowanie ryzyka wystąpienia awarii na linii produkcyjnej. Jednak nie jesteśmy w stanie całkowicie wyeliminować tego ryzyka – dlatego warto mieć również wypracowany plan awaryjny na wypadek pojawienia się przestoju. Każdy z pracowników, którzy na co dzień pracują z maszynami, powinien być przeszkolony z czynności podejmowanych w przypadku awarii.
Jak mierzyć i oceniać skuteczność wdrożonych rozwiązań w kontekście redukcji awarii i przestojów?
Strategie prewencyjne, systemy do monitorowania awarii oraz przestojów czy plany awaryjne to aspekty, o które szczególnie powinien zadbać każdy właściciel zakładu produkcyjnego. Jednak żadne rozwiązanie nie będzie od samego początku gwarantowało braku awarii. Dlatego tak istotne jest, aby monitorować wskaźniki wskazujące częstotliwość występowania incydentów oraz czas potrzebny do ich zniwelowania. Dzięki tym danym przedsiębiorcy będą mogli skutecznie dopracowywać stosowane strategie. Jakie metryki warto stosować?
Pierwszym wskaźnikiem, którym powinien zainteresować się właściciel zakładu produkcyjnego jest MTBF (Mean Time Between Failures), czyli średni czas bezawaryjnej pracy. Jak sama nazwa wskazuje, jest to wskaźnik określający średni czas pomiędzy awariami produktu technologicznego, jednak z zastrzeżeniem, że można je naprawić. Dzięki MTBF firma może monitorować dostępność wytwarzanego produktu. Jak interpretować ten wskaźnik? Im dłuższy czas pracy bez awarii, tym bardziej niezawodnymi procesami może pochwalić się zakład. Warto ustalić sobie jako cel utrzymanie MTBF na jak najwyższym poziomie.
Kolejnym istotnym wskaźnikiem jest MTTR (Mean Time To Repair), czyli średni czas naprawy przeważnie systemu technicznego lub mechanicznego, który jest używany w zakładzie produkcyjnym. MTTR obejmuje zarówno czas naprawy, jak i okres testowania zastosowanych poprawek. Aby prawidłowo określić ten wskaźnik, należy podawać czas liczony do momentu przywrócenia pełnej funkcjonalności uszkodzonego systemu. Warto regularnie kontrolować stan MTTR, ponieważ to niezwykle istotny czynnik pozwalający zespołom konserwacyjnym dbać o odpowiedni przebieg napraw. MTTR powinien być utrzymywany na jak najniższym poziomie dzięki zwiększeniu wydajności wszystkich procesów naprawczych oraz zespołów.
W celu uzyskania pełnego obrazu stanu parku maszynowego warto także kontrolować wskaźnik OEE (Overall Equipment Effectiveness). Wskaźnik OEE określa, w jakim stopniu wykorzystuje się maszyny w procesie produkcyjnym i jak efektywnie wykonują one swoje zadania. OEE to wynik iloczynu trzech innych wskaźników – dostępności (Availability), wydajności (Performance) oraz jakości (Quality). Odnoszą się one kolejno do – czasu, kiedy maszyna jest dostępna do pracy (dostępność), stopnia, w jakim maszyna wykorzystuje potencjał produkcyjny (wydajność) oraz liczby produktów spełniających wymagania jakościowe (jakość).
Chcesz skutecznie ograniczyć przestoje w Twoim zakładzie produkcyjnym? System IPLAS to rozwiązanie dla Ciebie – porozmawiajmy, jak możemy Ci pomóc!
+48 883 366 717