W nawiązaniu do ostatniej publikacji chcielibyśmy rozszerzyć temat pomiaru zużycia energii elektrycznej. Wstępnie omówiliśmy najczęstsze bariery jakie mogą przed nami stanąć, oraz jak w ekonomiczny sposób można rozpocząć proces pomiaru zużycia energii elektrycznej.
1. ROSNĄCE CENY ENERGII ELEKTRYCZNEJ
W dobie podnoszenie opłat za emisję CO2, konieczności modernizacji przestarzałych sieci przesyłowych oraz budowy nowych bloków energetycznych, oczywistością jest przerzucanie tych kosztów bezpośrednio na odbiorców energii elektrycznej. Już teraz wiele firm w szokowy sposób odczuwa nagły wzrost kosztów.
Niedawne kontrakty z poziomu cen 220-240zł/MWh wygasają, a nowe ceny kształtują się na poziomie 1000-1200 zł/MWh (lub więcej).
Oznacza to, że koszt energii elektrycznej zaczyna coraz bardziej obciążać budżety firm produkcyjnych.
W takiej sytuacji wielu menedżerów będzie stawało przed dylematem – przenosić te koszty na klientów, czy optymalizować zużycie? W tym momencie warto zawsze zadać pytanie – czy klient chce za to zapłacić? Odpowiedź brzmi – NIE, więc automatycznie powinniśmy rozpocząć wdrażanie procesu optymalizacji zużycia.
2. IDENTYFIKACJA NIEPOTRZEBNEGO ZUŻYCIA ENERGII
Na podstawie wcześniejszych analiz wiemy już do czego może prowadzić niekontrolowany pobór energii elektrycznej.
Najczęstsze przyczyny marnotrawstwa energii to:
- Nieefektywne korzystanie z oświetlenia, układów grzewczych i klimatyzacyjnych.
- Pozostawianie włączonych maszyn i innych urządzeń w trakcie przerw produkcyjnych (weekendy, święta).
- Użytkowanie nieefektywnych i energochłonnych maszyn (brak bieżących analiz pod kątem konieczności modernizacji).
- Niewłaściwe planowanie produkcji – wielogodzinna praca maszyn w trybie gotowości do produkcji, bez realizacji rzeczywistej produkcji.
- Niewłaściwe użytkowanie maszyn przez operatorów – stosowanie „własnych” nastaw i recept, bez konsultacji z działami technologicznymi.
- Długotrwała praca uszkodzonych maszyn i pobieranie w tym czasie nadmiernej ilości energii (zużyte łożyska, uszkodzone przekładnie itp).
Straty generowane w wyniku wszystkich powyższych marnotrawstw można liczyć w tysiącach, dziesiątkach, a w skrajnych przypadkach w setkach tysięcy złotych rocznie.
Często problemem jest też przyjęty sposób rozdziału kosztów zużytej energii elektrycznej na poszczególne procesy technologiczne. Nie mając dostępu do rzeczywistych danych pomiarowych, stosuje się analizę opartą na sumowaniu mocy zainstalowanej i procentowym podziale zużycia energii w zależności od tego wskaźnika. Jest to błąd, który najczęściej prowadzi do zakłamań w kwestii rzeczywistego podziału kosztów.
Maszyny o dużej mocy zainstalowanej, przy niezbyt dużym obciążeniu produkcją, mogą zużywać mniej energii niż urządzenia o mniejszej mocy zainstalowanej, ale o wysokim wykorzystaniu czasu dostępnego do produkcji. W tym właśnie momencie bardzo przydatne będą właśnie dane z zainstalowanych układów pomiarowych. Mogą one znajdować się w rozdzielniach głównych, na podejściach zasilających do maszyn, lub w innych punktach zależnie od topologii sieci energetycznej.
3. SAMO ZBIERANIE DANYCH O ZUŻYCIU ENERGII W ZAKŁADZIE NIE WYSTARCZY
Na rynku istnieje kilku wiodących dostawców takich urządzeń, jednak większość z nich ogranicza ewentualne zbieranie danych do kumulowania ich na urządzeniach zainstalowanych w rozdzielniach i odczyt bezpośrednio z nich lub za pośrednictwem dedykowanych aplikacji – przez WWW lub za pomocą np kabli USB. Dane takie nie mają jednak odpowiedniej rozdzielczości – widzimy tylko całkowity stan licznika kwh/kVar lub ewentualnie wartości chwilowe lub dobowe. Mamy jednak dobrą wiadomość! Z większością urządzeń pomiarowych można łączyć się za pośrednictwem protokołów MODBUS RTU/TCP IP lub innych. Dzięki temu możesz je skomunikować z systemem IPLAS, który będzie odczytywał, importował, a następnie automatycznie przetwarzał dane z rozdzielczością, jakiej potrzebujesz: co godzinę, minutę, sekundę.
Zamiast ogromu tabel i cyferek, będziesz mógł skorzystać z przejrzystych wizualizacji, które ułatwią Ci wyciąganie szybkich, a zarazem trafnych wniosków – stąd prosta droga do optymalizacji zużycia energii.
Przykład marnotrawstwa energii elektrycznej w zakładzie produkcyjnym:
Firma X posiada piec do wygrzewania elementów. Urządzenie jest włączone 365 dni w roku. W trakcie pracy utrzymuje się w nim temperatura około 600 stopni Celsjusza, na weekendy obniża się ją do 300 stopni Celsjusza. Maszyna jest programowana przez operatorów tak, aby w każdy poniedziałek o godzinie 6.00 była gotowa do pracy. W związku z tym o godzinie 4.00 w poniedziałek stopniowo podnosi temperaturę z 300 stopni (standby) do 600 stopni. W trakcie biegu jałowego przy temp 300 stopni maszyna pobiera około 200kW, przy 600 stopniach zużycie rośnie do około 350kW.
Ze względu na specyfikę produkcji oraz proces planowania nie w każdy poniedziałek operatorzy mają zlecenia umożliwiające prace. Bardzo często czekają do godziny 11.00 aż zostaną wydane nowe zlecenia.
Wynika z tego, że przez 5h maszyna zużywa około 750kwh energii. Przyjmując, że takich tygodni może być 20 w roku, można przyjąć, że firma traci 15 000kwh. To koszt około 15 000 – 18000 zł za samą energię czynną bez wszystkich opłat związanych z dystrybucją.
4. STRATY ENERGII, KTÓRYCH MOŻESZ UNIKNĄĆ
Przejdźmy teraz do sedna. Mamy już zainstalowane liczniki energii razem oraz dostęp do nich za pośrednictwem sieci ETHERNET. Urządzenia zostały też zaprogramowane zgodnie z instrukcją producenta (w naszym wypadku firmy SOCOMEC).
Czy import danych do IPLAS będzie skomplikowany?
Oczywiście, że nie! Korzystając z naszego doświadczenia udało się stworzyć automatyczny konfigurator takich połączeń, który przeprowadzi nas przez cały proces przygotowania do zbierania danych.
Poniżej prosta instrukcja w jaki sposób to zrobić:
Oczywiście, że nie! Korzystając z naszego doświadczenia udało się stworzyć automatyczny konfigurator takich połączeń, który przeprowadzi nas przez cały proces przygotowania do zbierania danych.
W menu Instalacje kliknij pozycję Szybka konfiguracja. W przypadku jeżeli nie masz zdefiniowanej żadnej instalacji pojawi się poniższa informacja. Obejrzyj nasz poradnik z którego dowiesz się w jaki sposób dodać instalacje oraz pobrać i zainstalować moduł Gateway.
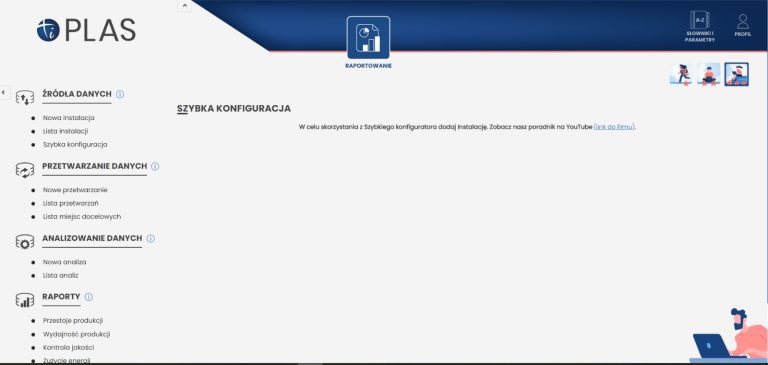
W kolejnym kroku zdefiniuj nazwę raportu oraz wybierz producenta urządzenia:
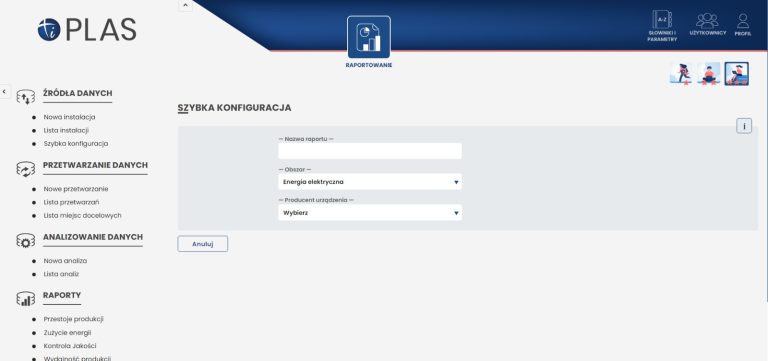
Następnie wybierz producenta oraz wskaż instalację, w której ma zostać dodany nowy kanał komunikacyjny:
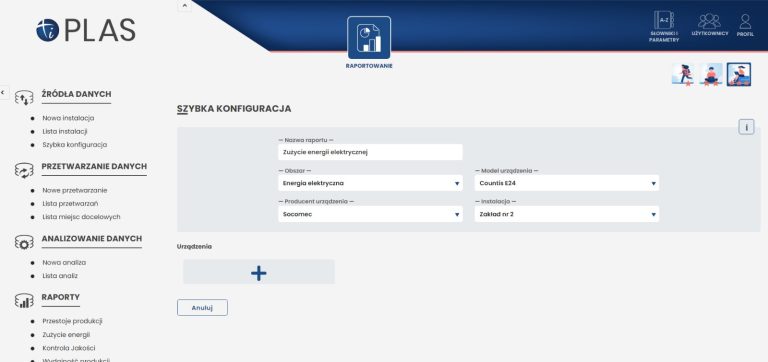
Na jednym raporcie możesz dodać do czterech urządzeń dla których wprowadzisz parametry w taki sam sposób jak w poprzednim kroku. Dodaj urządzenie klikając +
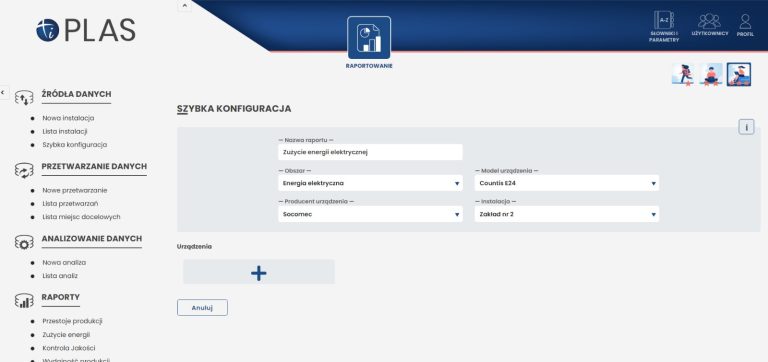
Wpisz parametry dodawanego urządzenia
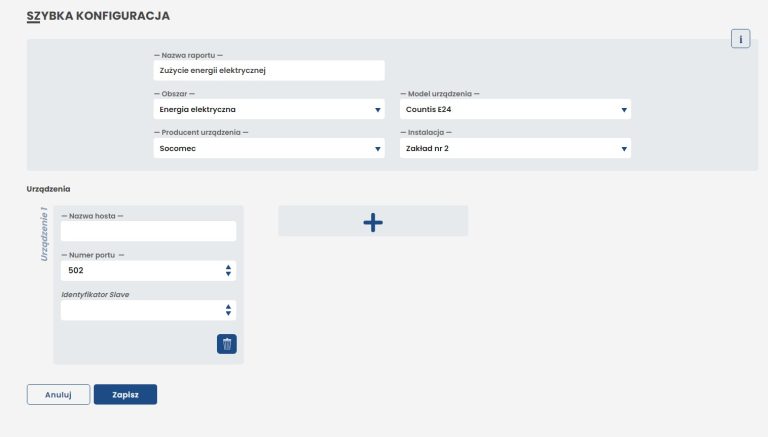
Konfigurację zakończysz klikając przycisk Zapisz po czym nastąpi przeniesienie do utworzonego raportu.
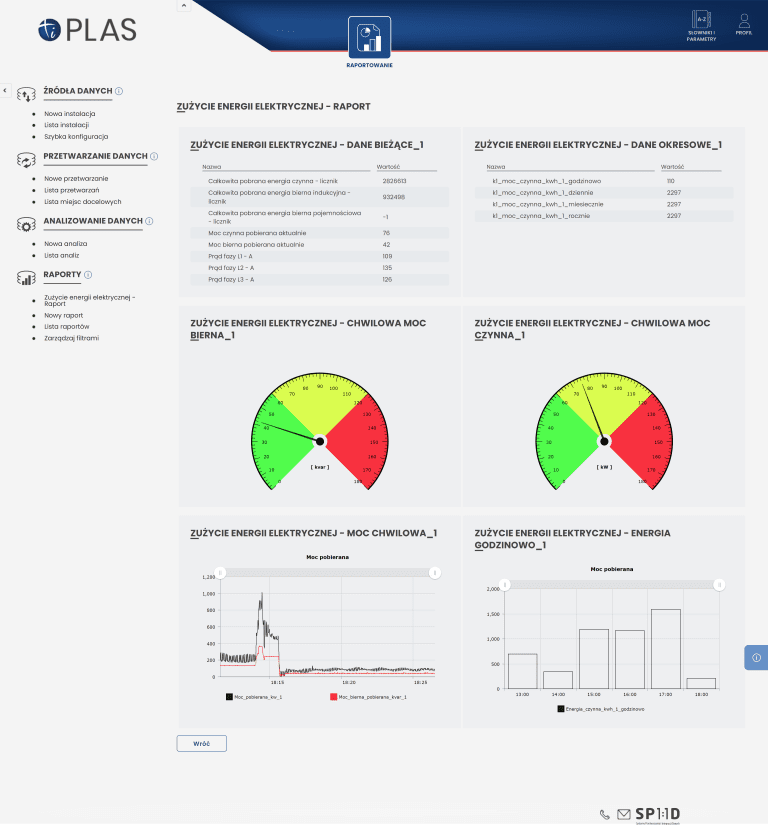
Odtąd system będzie zbierać dane, które wykorzystasz do tworzenia bardziej zaawansowanych raportów. Szybko wykryjesz źródła niepotrzebnego zużycia energii, podejmiesz właściwe kroki, by zoptymalizować produkcję i… od razu zauważysz to w raportach!
Chciałbyś zobaczyć Czym jest IPLAS?
Zadzwoń lub napisz do nas i opowiedz o problemach i potrzebach Twojej firmy!