Wstęp
System MES (Manufacturing Execution System) to zaawansowane oprogramowanie, które służy do zarządzania, monitorowania i synchronizowania realizacji procesów produkcyjnych w czasie rzeczywistym. Najprościej mówiąc, MES łączy świat planowania biznesowego z operacjami na hali produkcyjnej. W artykule wyjaśniamy, czym jest MES, jakie ma główne funkcje, jakie problemy produkcyjne rozwiązuje i jakie daje korzyści. Przyjrzymy się również, czym MES różni się od systemów ERP i SCADA, jakie wyzwania wiążą się z jego wdrożeniem oraz jakie istnieją alternatywy (np. systemy monitoringu produkcji i zużycia energii). Na koniec podpowiadamy, jak wybrać rozwiązanie najlepiej dopasowane do potrzeb Twojej firmy.
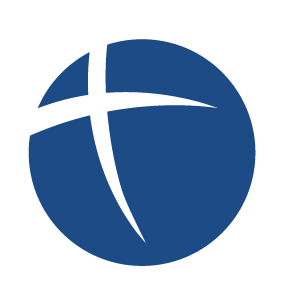
Czym jest system MES?
System MES (Manufacturing Execution System) to system informatyczny do nadzorowania i kontroli procesu produkcji na poziomie operacyjnym (shop floor). Gartner definiuje MES jako „specjalistyczną klasę oprogramowania produkcyjnego, która zarządza, monitoruje i synchronizuje wykonanie procesów przekształcania surowców w półprodukty lub wyroby gotowe w czasie rzeczywistym”. Innymi słowy, MES koordynuje realizację zleceń produkcyjnych, zbiera dane z maszyn i operatorów, śledzi postęp produkcji oraz zapewnia sprzężenie zwrotne o wydajności procesów i jakości produktów. MES działa zazwyczaj na poziomie 3 modelu ISA-95, pomiędzy systemami planowania zasobów przedsiębiorstwa (ERP) a systemami sterowania procesem (SCADA/PLC). Zapewnia to pomost między planowaniem produkcji a rzeczywistym wykonaniem na hali. W praktyce oznacza to, że system MES odbiera zlecenia i harmonogramy z ERP, przekłada je na szczegółowe instrukcje dla produkcji, monitoruje realizację w czasie rzeczywistym, a następnie odsyła do ERP informacje zwrotne (np. o wykonanej produkcji, zużytych materiałach, przestojach). MES wspiera także pełną genealogię produktów i śledzenie partii – od surowców po wyrób gotowy – co jest kluczowe np. w branży spożywczej czy farmaceutycznej. Podsumowując, system MES to „mózg operacyjny” produkcji cyfrowej. Jego zadaniem jest zapewnić, że plany produkcyjne są realizowane efektywnie na hali, a kierownictwo ma pełny wgląd w to, co dzieje się w fabryce – w czasie rzeczywistym i z dbałością o każdy detal procesu.Główne funkcje i moduły systemu MES
Systemy MES składają się z wielu modułów, które razem pokrywają większość potrzeb związanych z wykonaniem i nadzorem produkcji. Do kluczowych funkcji i obszarów MES należą m.in.:- Zbieranie danych produkcyjnych i monitorowanie w czasie rzeczywistym – automatyczny odczyt danych z maszyn, czujników i stacji roboczych, aby na bieżąco śledzić przebieg produkcji, czasy cykli, przestoje, awarie itp.. MES zapewnia aktualny obraz tego, co dzieje się na linii produkcyjnej, bez opóźnień i ręcznego raportowania.
- Harmonogramowanie i rozdzielanie zleceń (dispatching) – szczegółowe planowanie operacyjne produkcji, uwzględniające rzeczywiste ograniczenia zasobów (maszyn, ludzi, materiałów). MES optymalizuje kolejność i timing zleceń na podstawie priorytetów i dostępności zasobów. Dzięki temu możliwe jest tworzenie wykonalnych harmonogramów na poziomie hali, z uwzględnieniem zmian sytuacji w czasie rzeczywistym.
- Śledzenie produkcji, genealogia produktu – śledzenie przepływu materiałów i półproduktów przez kolejne etapy, rejestrowanie partii, numerów seryjnych, operacji wykonanych na każdym wyrobie. Pozwala to odtworzyć pełną historię powstawania produktu (traceability) – ważne dla kontroli jakości i zgodności z przepisami.
- Zarządzanie zasobami i urządzeniami – nadzorowanie dostępności i stanu maszyn, narzędzi, form, a także materiałów i personelu. MES może np. pilnować, czy wymagane narzędzia są kalibrowane, czy operatorzy mają odpowiednie uprawnienia, oraz rezerwować zasoby do zleceń.
- Kontrola jakości – monitorowanie parametrów jakościowych podczas produkcji, rejestrowanie wyników pomiarów, identyfikacja niezgodności i defektów. MES wspiera wdrażanie procedur jakości (SPC, kontrola statystyczna) i może blokować dalszą produkcję lub wysyłać alarmy, gdy jakość spada. Dzięki temu problemy jakościowe wychwytywane są natychmiast, a nie dopiero przy finalnej kontroli.
- Zarządzanie dokumentacją i procedurami – udostępnianie operatorom na bieżąco aktualnych instrukcji pracy, receptur, rysunków technicznych czy list kontrolnych. Moduł ten dba, aby każdy na produkcji pracował według aktualnej wersji dokumentacji (paperless manufacturing), eliminując błędy wynikające z przestarzałych wydruków.
- Analiza wydajności i raportowanie (KPI) – gromadzenie danych o wydajności maszyn i linii (np. OEE, wydajność, dostępność, jakość), a następnie prezentowanie ich w formie raportów i dashboardów. Kierownictwo dzięki temu identyfikuje wąskie gardła, przestoje, straty czasu i materiałów, co stanowi podstawę do ciągłego doskonalenia.
- Zarządzanie pracą pracowników – rejestrowanie czasu pracy operatorów na poszczególnych operacjach, monitorowanie kwalifikacji i obciążenia pracą (moduł Labor Management). Pozwala to lepiej planować zmiany, alokować ludzi tam gdzie są potrzebni i kontrolować wydajność pracy zespołów.
- Wspomaganie utrzymania ruchu – choć typowo za utrzymanie ruchu odpowiada system CMMS/TPM, dobry MES może dostarczać dane o pracy maszyn do działu utrzymania ruchu. Na podstawie danych z MES można wdrażać prewencyjne przeglądy – np. system zgłasza zbliżającą się awarię na podstawie spadku wydajności maszyny. Integracja MES z utrzymaniem ruchu pomaga zmniejszyć nieplanowane przestoje.
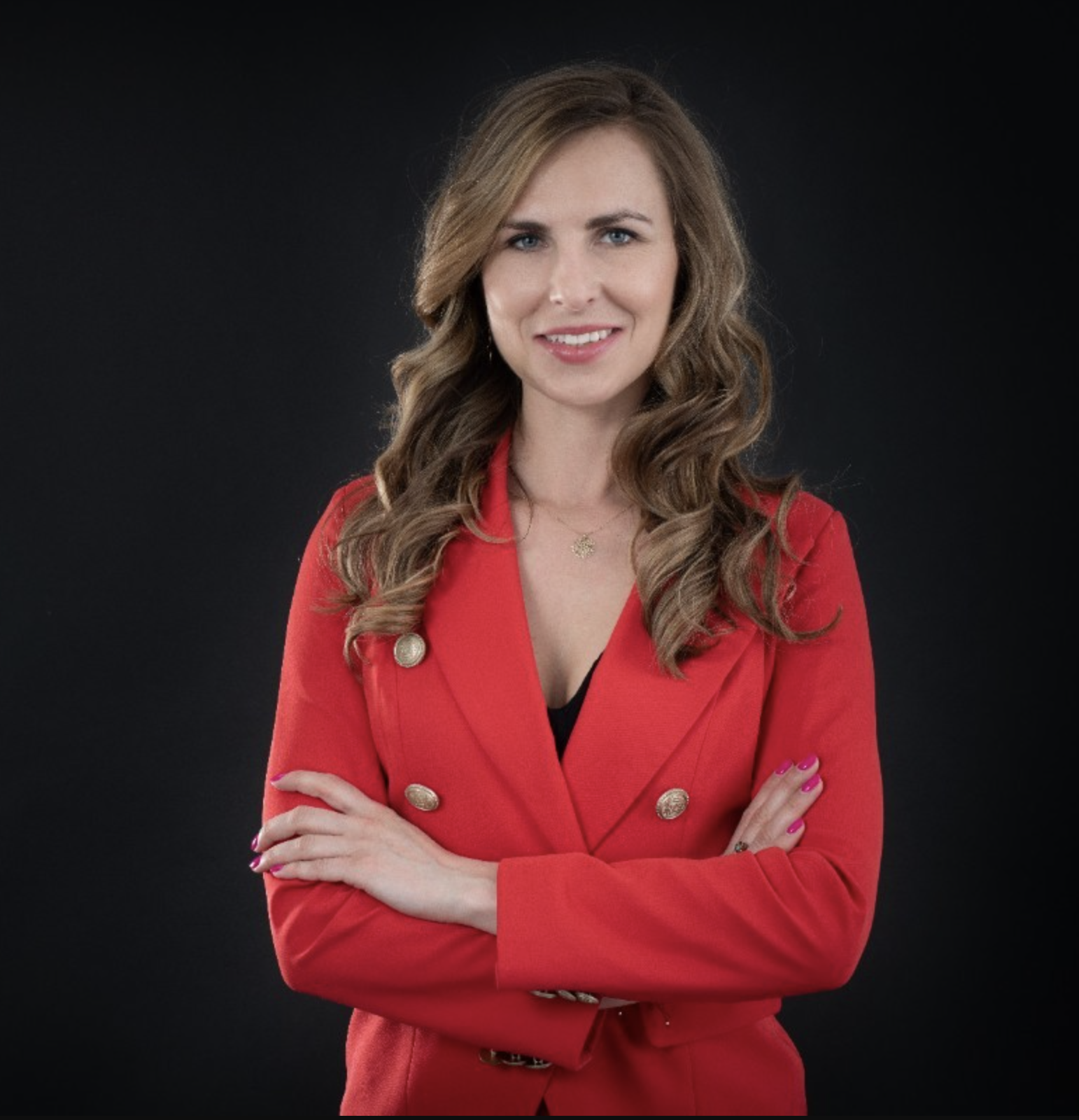
Monika Nowak
Dyrektor projektu iPLAS
Zbieraj dane z całej produkcji w jednym miejscu
iPLAS integruje dane z maszyn, procesów automatycznych i manualnych w czasie rzeczywistym. Bezpiecznie przechowujemy je w chmurze lub na Twoim serwerze, a dzięki zaawansowanemu przetwarzaniu danych zyskasz pełen wgląd w swoją produkcję.
Jakie problemy w produkcji rozwiązuje MES?
Tradycyjne, „analogowe” podejście do zarządzania produkcją wiąże się z wieloma wyzwaniami. System MES został stworzony właśnie po to, by rozwiązać kluczowe problemy trapiące zakłady produkcyjne, takie jak:- Brak bieżącej widoczności i opóźniona informacja zwrotna: W wielu fabrykach informacje o postępie produkcji czy problemach (awariach, brakach materiałów) docierają do kierownictwa z opóźnieniem – często dopiero przy raporcie na koniec zmiany lub dnia. MES rozwiązuje to, dając podgląd w czasie rzeczywistym na wszystkie operacje. Menedżerowie mogą natychmiast reagować na przestoje lub odchylenia od planu, zamiast dowiadywać się o nich po fakcie. Bieżący monitoring umożliwia szybsze usuwanie awarii i minimalizację strat.
- Niska efektywność i ukryte przestoje: Bez systemu MES wiele firm nie zna dokładnie swojego wskaźnika OEE ani prawdziwych przyczyn przestojów. Często pewne straty (np. mikro-przestoje, częste przezbrojenia, wolniejsza praca maszyn niż zakładano) pozostają niewidoczne. MES automatycznie zbiera dane o wszelkich przestojach, zatrzymaniach linii, niewykorzystanym czasie i pozwala identyfikować wąskie gardła oraz źródła nieefektywności. Dzięki temu kierownictwo może podjąć działania usprawniające – np. zmienić harmonogram przezbrojeń, lepiej szkolić operatorów czy zmodernizować najbardziej awaryjne urządzenia.
- Problemy z jakością i brak śledzenia produkcji: W środowisku bez MES kontrola jakości bywa wyrywkowa, a dane o defektach spóźnione. Trudno też prześledzić, z jakiej partii surowca powstał wadliwy produkt czy który operator przy nim pracował. MES rozwiązuje te problemy poprzez ciągłe monitorowanie jakości (rejestruje wyniki kontroli, może wymusić testy jakości na określonych etapach) oraz pełną traceability – każdy produkt ma zapisaną „historię życia” w systemie. W razie wykrycia wady można szybko ustalić, które partie są nią dotknięte i wycofać je lub poprawić, zamiast wycofywać całą produkcję.
- Ręczne raportowanie i papierologia: Wiele firm wciąż polega na ręcznym wypełnianiu kart pracy, meldunków produkcyjnych czy Exceli do raportowania. To generuje ogrom pracy administracyjnej, a do tego jest podatne na błędy i opóźnienia. MES znacząco eliminuje dokumentację papierową i ręczne wprowadzanie danych – dane produkcyjne zbierane są automatycznie, a raporty tworzą się same. Dzięki temu pracownicy mogą skupić się na produkcji, a nie na wypełnianiu papierów, a kierownictwo ma dostęp do informacji od razu po ich zarejestrowaniu (tzw. papierless shop floor).
- Niespójność danych i brak integracji: Gdy różne działy korzystają z odrębnych narzędzi (np. planowanie produkcji w Excelu, magazyn w ERP, a maszyny działają autonomicznie), dane bywają rozproszone i niespójne. MES pełni rolę centralnego hubu danych produkcyjnych – integruje się z maszynami (przez SCADA/PLC) oraz z systemem ERP, zapewniając jednolite, spójne informacje w całej organizacji. Eliminujemy sytuacje, gdzie np. dział planowania myśli, że zlecenie jest zrealizowane, podczas gdy na hali jest opóźnienie.
Korzyści biznesowe z wdrożenia MES
Wdrożenie systemu MES to poważna inwestycja, ale niesie za sobą wymierne korzyści biznesowe. Oto najważniejsze z nich, odczuwalne na poziomie całego przedsiębiorstwa:- Zwiększenie efektywności i produktywności: MES pozwala usprawnić przepływ pracy i wyeliminować wiele strat. Automatyzacja zbierania danych i optymalizacja harmonogramów produkcji przekładają się na lepsze wykorzystanie maszyn i ludzi. Według Rockwell Automation, MES daje możliwość takiego zarządzania procesem, by operacje stały się bardziej wydajne, produktywne i responsywne na zmiany. Firmy raportują wzrost wskaźnika OEE oraz więcej wykonanej produkcji w tym samym czasie dzięki wdrożeniu MES.
- Redukcja kosztów operacyjnych: Poprawa efektywności oznacza obniżenie kosztów na wielu polach. MES pomaga zmniejszyć straty materiałowe, energochłonność i przestoje, co natychmiast wpływa na koszty produkcji. Dzięki lepszemu planowaniu można też obniżyć poziom zapasów produkcji w toku (WIP) i materiałów „na wszelki wypadek” – system od razu aktualizuje stany magazynowe o zużyte surowce i wykonane produkty, co zmniejsza potrzebę utrzymywania nadmiernych buforów. Mniej błędów i poprawek to z kolei oszczędność na kosztach braków i reklamacji.
- Poprawa jakości i mniejsza liczba braków: Ciągłe monitorowanie parametrów procesu i wyników jakościowych sprawia, że jakość produktów utrzymuje się na wysokim poziomie. Jeśli wystąpią odchylenia, MES pozwala natychmiast wstrzymać produkcję wadliwą i skorygować problem. To ogranicza skalę produkcji braków i kosztownych przeróbek. Pełna identyfikowalność produktów ułatwia też ewentualne akcje serwisowe lub wycofanie wadliwej partii z rynku przy minimalnym wpływie na klienta.
- Skrócenie cyklu produkcyjnego i szybsza realizacja zamówień: Dzięki lepszemu harmonogramowaniu i eliminacji przestojów, całkowity czas cyklu od zlecenia do wyrobu gotowego ulega skróceniu. MES usprawnia koordynację dostaw materiałów, przezbrojeń i pracy zmian, co pozwala produkować szybciej i dotrzymywać terminów dostaw do klientów. To z kolei zwiększa konkurencyjność – firma może przyjąć więcej zamówień lub krócej realizować istniejące.
- Większa elastyczność produkcji: W dynamicznym otoczeniu rynkowym, możliwość szybkiej zmiany planów jest na wagę złota. MES czyni zakład bardziej elastycznym – ułatwia przeplanowanie produkcji „w locie” w reakcji na zmiany zamówień, priorytetów czy dostępności surowców. Nowe zlecenia, modyfikacje produktów, zmiany partii mogą być wdrażane płynnie, bo system od razu przelicza i przekazuje nowe instrukcje na halę.
- Lepsze wykorzystanie zasobów i mocy produkcyjnych: MES zapewnia pełny obraz wykorzystania maszyn, linii i pracowników. Łatwo dostrzeżemy np., że dana maszyna ma chroniczne przestoje w jakiejś zmianie, albo że pewne zasoby są niewykorzystane. To umożliwia optymalizację alokacji zasobów – przenoszenie obciążenia, zmiany grafików pracy, inwestycje tam, gdzie faktycznie brakuje mocy przerobowych. W rezultacie rośnie wydajność zakładu bez konieczności dużych nakładów (pracujemy mądrzej, nie tylko ciężej).
- Wsparcie zgodności i raportowania (np. pod kątem regulacji i ESG): System MES dba o to, by procesy odbywały się zgodnie z zadanymi parametrami i standardami. Każda czynność jest odnotowana, co ułatwia audyt i zgodność z wymaganiami prawnymi (np. w branży spożywczej – pełna dokumentacja HACCP, w farmacji – zgodność z FDA 21 CFR Part 11 dotyczącym zapisu elektronicznego itp.). Dodatkowo, MES śledzi zużycie energii, surowców i generowane odpady, co pomaga firmie monitorować ślad węglowy produktów i realizować cele zrównoważonego rozwoju. W dobie rosnącego znaczenia ESG, takie szczegółowe dane są nieocenione przy raportowaniu wpływu środowiskowego produkcji.
MES a systemy ERP i SCADA – różnice
Wiele osób zastanawia się, czym różni się MES od systemu ERP czy od systemu SCADA. To zrozumiałe, bo wszystkie trzy odgrywają ważną rolę w środowisku produkcyjnym, ale na różnych poziomach i w różnych celach. Można je zobrazować klasyczną piramidą automatyki (ISA-95), gdzie: ERP jest na poziomie 4 (planowanie biznesowe), MES na poziomie 3 (operacje produkcyjne), a SCADA/PLC na poziomach 1-2 (sterowanie maszynami). Poniżej wyjaśniamy te różnice bardziej praktycznie:- ERP (Enterprise Resource Planning): To system do zarządzania zasobami całego przedsiębiorstwa na poziomie strategicznym i planistycznym. ERP integruje takie obszary jak finanse, zaopatrzenie, magazyny, sprzedaż, kadry, a także planowanie produkcji. Jego zadaniem jest zapewnienie spójnego przepływu informacji w firmie – np. zamówienie od klienta trafia do ERP, który generuje zlecenie produkcyjne, zamawia surowce i planuje wysyłkę. ERP skupia się więc na planowaniu i rozliczaniu: co produkować, w jakiej ilości i kiedy, by zrealizować zamówienia i utrzymać optymalne stany magazynowe. Nie śledzi jednak szczegółowo przebiegu produkcji na hali ani pojedynczych operacji – od tego jest MES.
- MES (Manufacturing Execution System): Funkcjonuje na poziomie operacyjnym hali produkcyjnej. Otrzymuje plany i zlecenia (np. z ERP) i realizuje je, zarządzając procesem produkcyjnym w czasie rzeczywistym. MES nadzoruje wykonywanie zleceń, rozdziela je na stanowiska, zbiera dane z maszyn, kontroluje jakość i reaguje na bieżące zdarzenia. Można powiedzieć, że MES jest „przedłużeniem ręki” ERP na produkcji – dokonuje szczegółowej egzekucji planu oraz optymalizacji operacyjnej. Tam gdzie ERP operuje planem i danymi historycznymi (np. raporty dzienne, miesięczne), MES operuje sekundami, minutami i sztukami wyrobów tu i teraz. Dzięki temu MES umożliwia precyzyjne sterowanie procesem produkcji oraz szybkie reagowanie na wykryte nieprawidłowości w trakcie produkcji.
- SCADA (Supervisory Control and Data Acquisition): To system typowo inżynierski, działający na poziomie kontroli procesu. SCADA umożliwia nadzór nad pracą konkretnych urządzeń i linii technologicznych – zbiera dane z czujników, wyświetla je w formie wizualizacji synoptycznej i pozwala operatorowi sterować urządzeniami (np. włączyć pompę, wyregulować temperaturę). SCADA działa w czasie rzeczywistym na poziomie maszyn, często z interwałem milisekund czy sekund, ale jej zakres jest ograniczony do kontroli procesu technologicznego. Nie zarządza zleceniami produkcyjnymi ani nie prowadzi analizy biznesowej – to rola MES i ERP. Prosto ujmując: SCADA kontroluje pracę maszyn, MES zarządza całym procesem produkcji, a ERP planuje zasoby firmy.
Wyzwania i koszty związane z wdrożeniem MES
Mimo licznych zalet, wdrożenie systemu MES bywa wymagającym przedsięwzięciem. Oto główne wyzwania, na które warto się przygotować planując taką inwestycję:- Integracja z istniejącymi systemami: MES musi zostać połączony z innymi systemami w firmie – przede wszystkim z ERP (wymiana danych o zleceniach, stanach magazynowych) oraz z warstwą automatyki (SCADA, sterowniki PLC przy maszynach). Integracja ta bywa technicznie złożona, zwłaszcza gdy parki maszynowe są różnorodne lub system ERP jest mocno dostosowany. Warto upewnić się, że wybrany MES ma otwarte interfejsy API i wsparcie protokołów przemysłowych (OPC UA, MQTT itp.), a także zaplanować odpowiedni budżet i czas na prace integracyjne.
- Dostosowanie procesów i organizacji: Wdrożenie MES to nie tylko instalacja oprogramowania, ale często reorganizacja sposobu pracy. Trzeba zdefiniować na nowo procedury zbierania danych, obowiązki operatorów (np. meldowanie przyczyn przestojów), sposoby eskalacji problemów. Konieczne jest ustalenie nowych wskaźników wydajności (KPI), które system będzie śledził, oraz zasad, jak te dane wykorzystać. Opór przed zmianą bywa istotną barierą – kluczowe jest zaangażowanie załogi, odpowiednie szkolenia i jasna komunikacja celu wdrożenia.
- Wybór właściwych funkcjonalności: Systemy MES oferują mnóstwo modułów i opcji. Wyzwanie stanowi określenie, co jest naprawdę potrzebne na start, a co można dodać później. Nadmierna komplikacja od początku może wydłużyć wdrożenie i przytłoczyć użytkowników. Z kolei pominięcie istotnej funkcji może zmniejszyć wartość systemu. Dlatego tak ważna jest analiza potrzeb przed wdrożeniem – zidentyfikowanie największych bolączek produkcji i skupienie się na nich w pierwszej kolejności.
- Koszty i ROI: Koszt wdrożenia MES zależy od wielu czynników – wielkości zakładu, liczby stanowisk do objęcia, zakresu funkcji, stopnia integracji oraz wybranego dostawcy. Może on wynieść od kilkudziesięciu do nawet kilkuset tysięcy złotych. Do tego dochodzą koszty infrastruktury (np. serwery, sieć na hali, terminale dla operatorów) oraz ewentualnych modyfikacji oprogramowania pod specyficzne potrzeby. Wdrożenie bywa czasochłonne (kilka miesięcy do ponad roku). Jest to zatem poważna inwestycja – zwykle usprawiedliwiona przez korzyści, jakie przynosi (poprawa jakości, wzrost wydajności, redukcja kosztów produkcji). Zwrot z inwestycji (ROI) zależy od skali produkcji i obszarów, w których były największe problemy; często jednak firmy widzą znaczące oszczędności i wzrost efektywności, dzięki czemu inwestycja potrafi się zwrócić w ciągu 1-3 lat.
- Wsparcie i utrzymanie systemu: Po uruchomieniu MES istotne jest jego utrzymanie – aktualizacje, serwis, dostosowywanie do zmieniających się potrzeb. Trzeba zapewnić odpowiednie wsparcie IT i merytoryczne. Warto upewnić się, że dostawca oferuje szkolenia dla użytkowników, pomoc przy kalibracji raportów czy dostosowywaniu systemu wraz ze zmianami procesów. Firmy często decydują się na stopniowe rozwijanie MES modułowo, zaczynając od podstawowego zakresu, a potem dokładając kolejne funkcjonalności. To rozsądne podejście pozwala rozłożyć koszty w czasie i uczyć się systemu etapami.
Alternatywy i uzupełnienie MES: systemy monitoringu produkcji i energii
Dla firm, które nie są gotowe na pełne wdrożenie MES lub chcą stopniowo wejść w świat cyfrowej produkcji, ciekawą opcją są lżejsze systemy monitoringu produkcji oraz zużycia energii. Takie rozwiązania koncentrują się na kluczowych aspektach efektywności bez wdrażania pełnej funkcjonalności MES. Mogą one działać równolegle do istniejących procesów i dostarczać szybkich korzyści w wybranych obszarach. Co potrafią systemy monitoringu produkcji? Są to systemy (często zaliczane do kategorii Industrial IoT lub Manufacturing Performance Monitoring), które podłączają się do maszyn i urządzeń, zbierając z nich dane o pracy – np. czasy cyklu, tempo produkcji, przestoje, awarie, licznik wyprodukowanych sztuk. Dane te prezentowane są w czasie rzeczywistym w postaci przejrzystych dashboardów i wykresów dla kadry zarządzającej. Celem jest uzyskanie natychmiastowej widoczności tego, co dzieje się na hali oraz identyfikacja niewykorzystanych możliwości. W przeciwieństwie do pełnego MES, takie systemy mogą nie zarządzać zleceniami produkcyjnymi ani recepturami – skupiają się raczej na monitorowaniu i analizie wydajności (np. OEE dla maszyn, dostępność, cykle pracy). Ich zaletą jest stosunkowo niższy koszt i krótszy czas wdrożenia – często są to rozwiązania chmurowe, działające w modelu abonamentowym, gotowe do integracji z różnymi maszynami. Monitoring zużycia energii to drugi ważny element, który zyskuje na popularności. Energia stanowi dziś znaczący koszt w produkcji, a dodatkowo firmy kładą nacisk na ograniczenie śladu węglowego i realizację celów zrównoważonego rozwoju (ESG). Systemy monitoringu energii instalują liczniki i czujniki IoT na maszynach oraz liniach, by szczegółowo śledzić pobór prądu, gazu, wody i innych mediów przez poszczególne procesy. Dzięki temu można ustalić, ile energii zużywa wyprodukowanie jednej sztuki wyrobu, które urządzenia są najbardziej energochłonne i gdzie występują piki poboru mocy. Analiza takich danych ujawnia możliwości oszczędności – np. przesunięcie produkcji energochłonnej na tańszą taryfę nocną, usprawnienie procesu rozruchu maszyn, wyłączanie urządzeń podczas dłuższych przestojów. Co ważne, ciągły monitoring pozwala też szybko wykryć anomalie mogące świadczyć o awarii (np. nagły wzrost zużycia energii przez silnik sugeruje usterkę). Według ekspertów KPMG, wykorzystanie danych i optymalizacji energetycznej w produkcji może przynieść poprawę zużycia energii nawet o 8–15%, co stanowi istotną redukcję kosztów i emisji CO₂. Widać więc, że cele biznesowe (oszczędność kosztów) i środowiskowe mogą iść w parze, gdy dysponujemy szczegółowymi danymi o mediach. Jak się to ma do MES? Systemy monitoringu produkcji i energii można traktować jako uzupełnienie MES albo krok w jego kierunku. Dla firm, które nie potrzebują pełnej funkcjonalności MES (np. zarządzania zleceniami w systemie), a chcą przede wszystkim poprawić nadzór nad wydajnością i zużyciem zasobów, takie rozwiązania mogą być wystarczające. Często są one bardziej przyjazne dla użytkownika i wdrażane oddolnie – montujemy czujniki, uruchamiamy platformę chmurową i po krótkim czasie widzimy pierwsze dane. Nie trzeba przy tym reorganizować całego procesu produkcji ani szkolić załogi z obsługi rozbudowanych modułów MES. Z drugiej strony, jeśli firma planuje w przyszłości pełne MES, to wdrożony wcześniej system monitoringu może stać się jego częścią (wiele systemów MES ma moduły OEE czy Energy Management – można z czasem migrować dane) lub integrować się z MES jako źródło danych. Poniżej przedstawiamy krótkie porównanie tradycyjnego systemu MES z lżejszymi systemami monitoringu produkcji/energii:Aspekt | Pełny system MES | System monitoringu produkcji/energii |
---|---|---|
Zakres funkcjonalny | Szeroki: zarządzanie całym procesem produkcji (zlecenia, harmonogramy, kontrola jakości, traceability, raportowanie itp.). | Wąski/ukierunkowany: monitorowanie pracy maszyn, wydajności i zużycia mediów; analiza danych produkcyjnych bez zarządzania zleceniami. |
Integracja z innymi systemami | Wymagana integracja z ERP (dwukierunkowa wymiana danych) oraz z automatyką (SCADA/PLC) i innymi systemami (CMMS, WMS). | Zazwyczaj samodzielny lub luźno zintegrowany; może pobierać dane z maszyn (czujniki IoT, PLC) i opcjonalnie wysyłać kluczowe dane do ERP. |
Koszt i czas wdrożenia | Wysoki koszt (licencje, wdrożenie, konfiguracja) i długi czas (kilka miesięcy+), ze względu na złożoność i dostosowanie do procesów firmy. | Niższy koszt (abonament w chmurze, mniej customizacji) i krótszy czas wdrożenia (często kilka tygodni). Mniej ingerencji w istniejące procesy. |
Wpływ na procesy | Wymaga dostosowania procesów i przeszkolenia personelu w szerokim zakresie. Zmienia sposób pracy (meldowanie produkcji w systemie, nowe procedury jakości itp.). | Minimalny wpływ na bieżące procesy – operatorzy często nie muszą wykonywać dodatkowych czynności, system działa głównie w trybie odczytu danych i raportowania. |
Efekty i korzyści | Kompleksowa optymalizacja całej produkcji (lepsze planowanie i wykonanie, mniej braków, pełna kontrola). Dane dla wszystkich działów (od produkcji przez kontroling po logistykę). | Szybkie usprawnienia punktowe: poprawa OEE maszyn, redukcja przestojów, oszczędność energii, wykrycie marnotrawstwa. Lepsza świadomość sytuacji produkcyjnej u kadry kierowniczej. |
Skalowalność i rozwój | Możliwość dodawania kolejnych modułów (np. zaawansowana jakość, harmonogramowanie APS). System rośnie z firmą, ale zmiany mogą być kosztowne i wymagają wsparcia dostawcy. | Łatwe zwiększanie zakresu monitorowanych urządzeń czy dodanie nowych wskaźników. Często dostępne aktualizacje w chmurze. W razie potrzeby możliwa rozbudowa do pełniejszego MES w przyszłości. |
Iplas – więcej niż system MES
W kontekście omawianych lżejszych rozwiązań warto wspomnieć o przykładzie z polskiego rynku. Iplas.pl to platforma, która dostarcza nowoczesne narzędzia do monitorowania i optymalizacji produkcji, łącząc wiele zalet MES z lekkością systemu IIoT. Rozwiązanie iPLAS umożliwia:- Automatyczną akwizycję danych ze wszystkich maszyn i procesów w czasie rzeczywistym, bez angażowania operatorów. System sam zbiera informacje o wydajności, przestojach, awariach, a nawet o zużyciu mediów (energia, gaz, surowce) na poszczególnych stanowiskach. Dzięki temu kadra zarządzająca ma ciągły podgląd kluczowych wskaźników, 24 godziny na dobę – również w nocy i weekendy.
- Inteligentne alerty i nadzór nad krytycznymi parametrami: iPLAS potrafi automatycznie pilnować wartości krytycznych takich jak czas trwania przestojów, temperatura procesów czy zużycie energii/materiałów. Gdy wykryje odchylenie od normy, natychmiast powiadamia odpowiedzialne osoby (np. poprzez e-mail/SMS). Pozwala to szybko reagować na awarie lub marnotrawstwo – zanim przerodzą się one w poważny problem.
- Analizę efektywności i identyfikację wąskich gardeł: Platforma zbiera w jednym miejscu dane z parku maszynowego oraz dane produkcyjne (np. realizacja zamówień, dane wprowadzone przez brygadzistów) i umożliwia ich łączenie. W praktyce oznacza to, że można łatwo zobaczyć które zlecenia produkcyjne realizowane są planowo, a które mają opóźnienia, jakie są najczęstsze przyczyny przestojów na danej linii, jak zmiany produkcyjne różnią się wydajnością itp. To cenna wiedza do optymalizacji procesów – często osiągalna bez wdrażania pełnego MES.
- Niską barierę wejścia i skalowalność: W przeciwieństwie do klasycznych systemów MES, iPLAS oferowany jest w modelu cloud (oprogramowanie jako usługa). Dzięki temu koszt startowy jest niski – aby zacząć monitorować i optymalizować produkcję, wystarczy abonament na poziomie ok. 300 zł miesięcznie. Tak przynajmniej deklaruje dostawca, co czyni rozwiązanie dostępnym nawet dla mniejszych firm. Podejście chmurowe zapewnia też skalowalność – można zacząć od monitoringu jednej linii, a z czasem objąć systemem kolejne wydziały, dokładać moduły analityczne itp., płacąc tylko za to, z czego faktycznie się korzysta.
- Szybkie wdrożenie i wsparcie: Dostawca iPLAS podkreśla, że wdrożenie jest szybkie, a pierwsze efekty widoczne niemal natychmiast. System jest projektowany z myślą o użytkowniku – dane prezentowane są w czytelnej formie (wykresy, tablice wyników) i dostępne przez przeglądarkę z dowolnego miejsca. Firma oferuje również wsparcie we wdrożeniu, szkolenia dla pracowników oraz pomoc w interpretacji danych, aby klienci faktycznie osiągnęli zamierzone usprawnienia.
Jak wybrać odpowiedni system MES lub inne rozwiązanie?
Wybór systemu dla produkcji to strategiczna decyzja, która powinna wynikać z indywidualnych potrzeb i celów firmy. Oto kilka kroków i kryteriów, które warto wziąć pod uwagę, podejmując decyzję o wdrożeniu MES bądź alternatywy:- Analiza potrzeb i dojrzałości cyfrowej: Na początku określ, co chcesz osiągnąć dzięki systemowi. Czy głównym problemem jest brak danych i przejrzystości? Zbyt długie cykle produkcyjne? Niska jakość? Wysokie koszty energii? Różne cele mogą sugerować różne rozwiązania. Zbadaj również obecną infrastrukturę IT i OT w swoim zakładzie – czy masz już jakieś elementy (np. SCADA, czujniki IoT, moduły w ERP) które można wykorzystać? Oceń gotowość organizacji na zmiany. Ta samoocena pozwoli Ci ustalić, czy potrzebujesz kompleksowego MES, czy na początek wystarczy mniejszy system. Pamiętaj, że wybór zależy od wielu czynników, takich jak wielkość firmy, natura biznesu, specyficzne wymagania branżowe i budżet. Inaczej podejdzie do tematu duża fabryka motoryzacyjna, a inaczej średni zakład produkcji opakowań.
- Zestawienie opcji (MES vs. alternatywy): Mając jasno określone potrzeby, porównaj dostępne opcje. Jeżeli wymagasz pełnej funkcjonalności (zarządzanie zleceniami, zaawansowana jakość, integracja end-to-end), prawdopodobnie będziesz celować w system MES od uznanych dostawców (Siemens Opcenter, Rockwell FactoryTalk, Wonderware/AVEVA MES, SAP MES itd.). Jeśli jednak priorytetem jest szybkie usprawnienie monitoringu i OEE, przeanalizuj lżejsze systemy – na rynku istnieją zarówno rozwiązania globalne (np. Plex Production Monitoring, GE Proficy MDC), jak i lokalne jak wspomniany iPLAS. Sporządź tabelę wymagań i sprawdź, które systemy je spełniają.
- Ocena dostawców i referencje: Przy wyborze MES warto kierować się opiniami niezależnych ekspertów i użytkowników. Pomocne mogą być raporty takie jak Gartner Magic Quadrant for MES czy analizy Forrester, które wskazują liderów rynku i trendy innowacji. Sprawdź, czy dostawca ma doświadczenie w Twojej branży i czy może pochwalić się wdrożeniami o podobnej skali. Poproś o demo lub projekt pilotażowy – wielu dostawców oferuje uruchomienie systemu na próbę w ograniczonym zakresie, co pozwoli ocenić, czy interfejs i funkcje nam odpowiadają, zanim zainwestujesz w pełne wdrożenie.
- Koszty całkowite i ROI: Patrz szerzej niż tylko na cenę licencji. Uwzględnij koszty usług wdrożeniowych, integracji, sprzętu (np. terminale, sieć), szkoleń, a także późniejszego utrzymania (aktualizacje, support). Porównując oferty MES vs. prostsze systemy, rozważ model płatności – licencja jednorazowa vs. abonament SaaS. Czasem droższy system może dać większe oszczędności (np. redukcja braków o kilka procent może być warta każdej ceny). Policzenie potencjalnego ROI (zwrotu z inwestycji) bardzo pomaga w podjęciu decyzji i przekonaniu zarządu. Możesz zadać dostawcom pytanie o przewidywane korzyści – ci renomowani powinni móc podać przykłady, że np. u klienta X poprawiono produktywność o Y% po wdrożeniu ich systemu.
- Możliwość skalowania i elastyczność: Dobrze dobrany system to taki, który będzie rósł razem z firmą. Upewnij się, że architektura rozwiązania pozwala na rozbudowę (np. dodawanie kolejnych modułów MES w miarę potrzeb, integracje z nowymi maszynami). Unikaj rozwiązań zamkniętych, które mogłyby Cię uw locked-in u jednego dostawcy bez opcji integracji. Dzisiejszy świat produkcji jest dynamiczny – być może za rok zechcesz wdrożyć moduł predykcyjnego utrzymania ruchu albo połączyć dane produkcyjne z systemem BI. Otwartość i nowoczesność platformy (obsługa chmury, IoT, AI) to czynniki, które zapewnią, że inwestycja będzie przyszłościowa.
Podsumowanie
System MES jest potężnym narzędziem usprawniającym zarządzanie produkcją – dostarcza wglądu w procesy, zwiększa efektywność i ułatwia podejmowanie decyzji opartych o dane. Dla wielu firm wdrożenie MES staje się krokiem milowym w drodze do Fabryki 4.0. Niemniej jednak, nie jest to jedyna droga: istnieją również bardziej zwinne rozwiązania, takie jak systemy monitoringu produkcji i zużycia energii, które mogą przynieść szybkie korzyści tam, gdzie potrzebujemy przede wszystkim transparentności i eliminacji marnotrawstwa. Decydenci w firmach produkcyjnych powinni rozważyć wszystkie za i przeciw – ocenić swoje potrzeby, możliwości budżetowe i zasoby ludzkie. Czasem lepszym wyborem będzie pełnoskalowy MES zintegrowany z ERP i SCADA, a czasem wystarczy mniej skomplikowany system IIoT, który wskaże kierunki usprawnień. Niezależnie od wyboru, jedno jest pewne: inwestycja w cyfrowe narzędzia do zarządzania produkcją jest dziś kluczem do pozostania konkurencyjnym, bardziej ekologicznym (niższy ślad węglowy) i odpornym na wyzwania przyszłości. Zachęcamy więc do dalszego zgłębiania tematu i wyboru rozwiązania najlepiej dopasowanego do Waszej organizacji – takiego, które pozwoli produkować mądrzej, szybciej i czyściej już od teraz.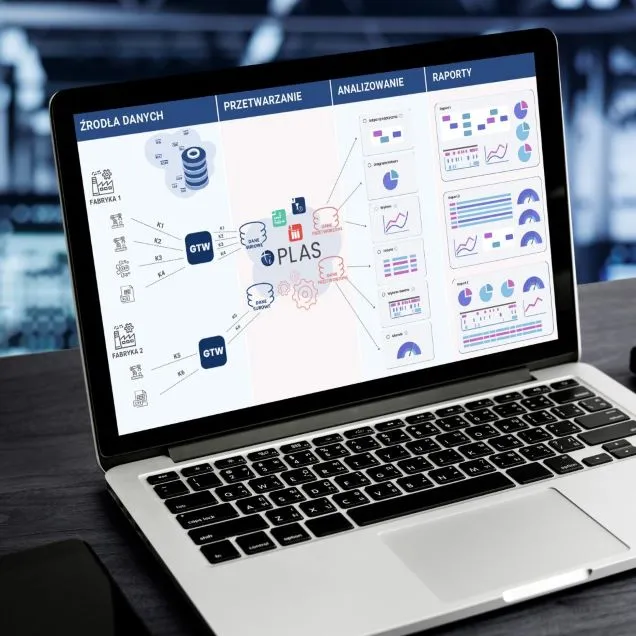
+48 883 366 717