Wstęp
Rosnąca zmienność cen energii elektrycznej stała się jednym z najbardziej palących wyzwań dla zakładów produkcyjnych w Polsce. W branżach energochłonnych – od hut szkła po zakład przetwórczy kruszyw – koszt MWh potrafi decydować o marży, a nawet o utrzymaniu produkcji. Dlatego coraz częściej słyszymy pytanie: jak zaplanować produkcję, aby wykorzystać najtańszą energię i ograniczyć ryzyko kosztowe?
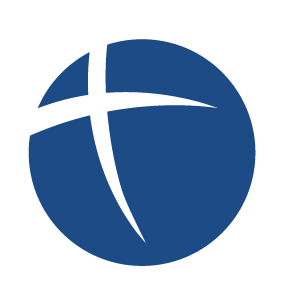
Wyjściowe wyzwanie
- Duże wahania cen: cena energii potrafi zmieniać się nawet o kilkaset procent w ciągu doby.
- Brak przejrzystych danych w czasie rzeczywistym: menedżerowie potrzebują jednego „pulpitu dowodzenia”, a nie kilku niezsynchronizowanych arkuszy i portali.
- Ograniczona elastyczność linii: wiele procesów nie może po prostu stanąć „od ręki”, ale część produkcji (np. praca na bufor) można przesunąć w czasie.
Rozwiązanie: moduł analizy i prognozy cen energii w systemie iPLAS
W odpowiedzi rozbudowaliśmy Moduł Analizy Zużycia Energii w systemie iPLAS o mechanizm pobierania i wizualizacji:
Dane | Źródło | Częstotliwość | Co dają? |
---|---|---|---|
RCE (rynkowa cena energii) | Polskie Sieci Energetyczne | codziennie ok. 14:00 | plan na kolejną dobę |
Cena Prognozowana (intra-day) | Polskie Sieci Energetyczne | co 15 min, z opóźnieniem 45–90 min | bieżąca korekta planu |
Zużycie energii | liczniki MODBUS / MBUS / PROFINET | on-line | weryfikacja realizacji planu |
Jak to działa w praktyce?
- Import prognozy RCE – po 14:00 system iPLAS pobiera ceny na jutro i automatycznie koloruje kwadranse powyżej ustalonego progu (alert).
- Symulacja obciążeń – planista widzi, które linie można „przerzucić” na tańsze godziny.
- Monitoring live – w ciągu doby system dogrywa bieżącą „Cenę Prognozowaną”, pozwalając korygować decyzje co 15 min.
- Nakładanie mocy – rzeczywiste pobory z liczników nakładane są na cenę; odstępstwa od planu widać natychmiast.
Przykładowy scenariusz (symulacja) – zakład produkcji szyb zespolonych
Uwaga: poniższe wartości są hipotetyczne i mają zilustrować potencjał oszczędności.
Parametr | Przed optymalizacją | Po wdrożeniu symulacji | Szacowany efekt* |
---|---|---|---|
Roczne zużycie energii | 7 000 MWh | 7 000 MWh | — |
Średni koszt zakupu MWh | 630 PLN | 510 PLN | -19 % |
Łączny roczny koszt energii | 4,41 mln PLN | 3,57 mln PLN | -840 tys. PLN |
*Oszczędność wynika z przesunięcia pracy do godzin o najniższej cenie RCE oraz uniknięciu szczytów taryf mocy.
Kroki symulacji:
- System iPLAS zaczytuje prognozę RCE i oznacza kwadranse powyżej 1 000 PLN/MWh.
- Planista układa plan wsadowy tak, by cykle pracy rozpoczynały się w „zielonych” oknach cenowych.
- Na bieżąco monitorowane są odchylenia mocy; w razie skoku ceny (na podstawie „Ceny Prognozowanej”) system sugeruje krótkie postoje pomocniczych urządzeń.
Dla kogo?
- Przemysł szklarski i ceramiczny – piece, suszarnie, hartownie.
- Krystalizacja i mielenie kruszyw – młyny, kruszarki.
- Chłodnie, mroźnie, HVAC – obiekty pracujące na bufor chłodu.
- Przemysł chemiczny.
Kluczowe korzyści biznesowe
- Natychmiastowe – niższa faktura za energię, bez CAPEX (wykorzystujemy istniejące liczniki).
- Strategiczne – lepsza pozycja w negocjacjach z dostawcą energii dzięki twardym danym zużycia vs ceny.
- Operacyjne – wszystkie kluczowe dane w jednym dashboardzie systemu iPLAS; koniec z „Excel-ping-pongiem”.
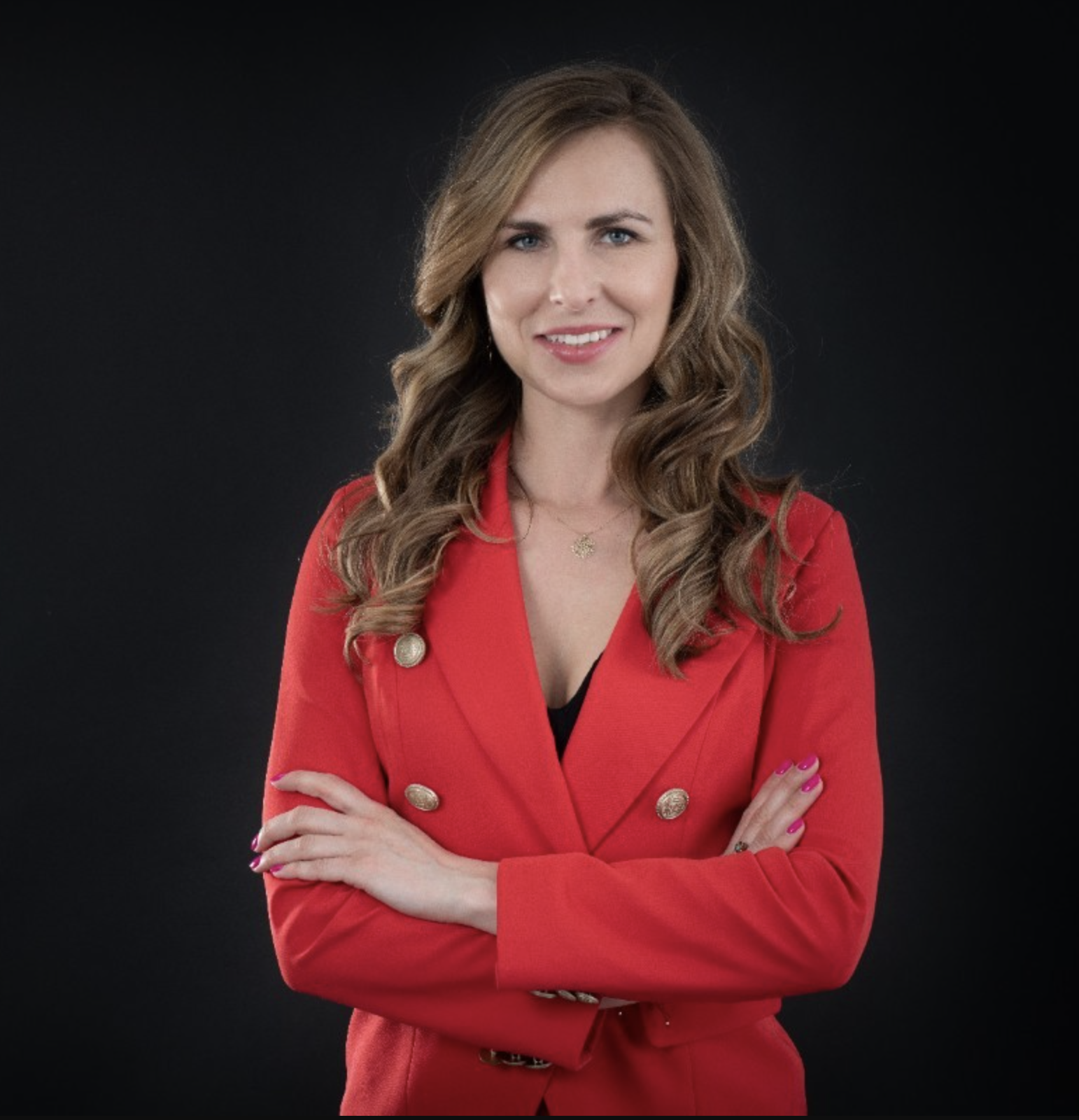
Monika Nowak
Dyrektor projektu iPLAS
Zbieraj dane z całej produkcji w jednym miejscu
iPLAS integruje dane z maszyn, procesów automatycznych i manualnych w czasie rzeczywistym. Bezpiecznie przechowujemy je w chmurze lub na Twoim serwerze, a dzięki zaawansowanemu przetwarzaniu danych zyskasz pełen wgląd w swoją produkcję.
FAQ – najczęstsze pytania o moduł prognozy cen w systemie iPLAS
Pytanie | Odpowiedź |
---|---|
1. Na ile dokładne są prognozy cen energii? | System korzysta z oficjalnych danych PSE – rynkowa cena energii (RCE) publikowana jest raz dziennie, a cena prognozowana uzupełniana co 15 min z opóźnieniem 45–90 min. W praktyce odchylenia od ceny rozliczeniowej są zwykle < 5 %. |
2. Co, jeśli cena zmieni się gwałtownie w trakcie dnia? | Algorytm iPLAS monitoruje aktualizacje PSE i może wysłać alert (SMS, e-mail, push) z propozycją korekty planu – np. krótkiego postoju młyna lub przyspieszenia cyklu pieca. |
3. Czy przesuwanie produkcji nie pogorszy OEE ani terminów dostaw? | Przesuwane są tylko te operacje, które mają bufor technologiczny (np. hartowanie szkła, mielenie kruszyw). Parametry jakości procesów ciągłych (temp., wilgotność) pozostają pod kontrolą; OEE linii głównych zwykle nie spada, a często rośnie dzięki lepszej dostępności mocy. |
4. Jakie liczniki energii są potrzebne? | Wystarczą urządzenia z protokołami MODBUS RTU/TCP, MBUS, PROFINET lub IEC 62056-21. Jeżeli zakład posiada starsze liczniki, iPLAS może pobierać dane poprzez bramkę komunikacyjną. |
5. Ile trwa wdrożenie? | Typowy harmonogram to 4–6 tyg.: 1) audyt liczników i sieci → 2) podłączenie API PSE i konfiguracja progów → 3) parametryzacja dashboardu → 4) szkolenie użytkowników i testy „na sucho”. |
7. Czy rozwiązanie działa także przy własnej fotowoltaice lub magazynie? | Tak. iPLAS potrafi uwzględnić stan SoC magazynu, aby jeszcze lepiej zoptymalizować pobór z sieci i sprzedaż nadwyżek. |
9. Co z bezpieczeństwem danych produkcyjnych? | Komunikacja odbywa się po VPN lub HTTPS z szyfrowaniem AES-256; wszystkie dane przechowywane są w centrum danych ISO 27001 (on-prem lub cloud). |
10. Czy moduł można zintegrować z istniejącym ERP lub SCADA? | Tak – dostępne są konektory REST/OPC UA oraz pliki CSV/XLS. Możliwe jest również dwukierunkowe sterowanie (np. automatyczne plany wsadowe wysyłane do PLC). |
Podsumowanie
Dynamiczny rynek energii wymusza elastyczność, ale równocześnie otwiera przestrzeń do realnych oszczędności. Moduł prognozy cen w systemie iPLAS pozwala przesunąć energochłonne operacje w najtańsze kwadranse doby, monitorować realizację planu w czasie rzeczywistym i obniżyć koszt produkcji nawet o kilkanaście–kilkadziesiąt procent. Jeśli chcesz sprawdzić, jaki potencjał drzemie w Twoim zakładzie, odezwij się – przygotujemy darmową analizę symulacyjną.
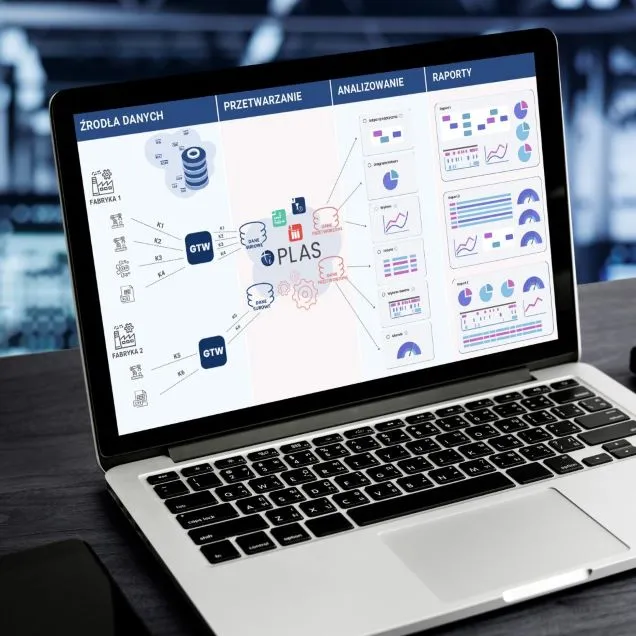
+48 883 366 717