Introduction
If you’re a business owner with a manufacturing facility, one of your top priorities should be how well your production processes are running and whether they meet the defined standards. Verifying these aspects can help reduce additional costs and minimize the risk of producing faulty products. However, in reality, very few entrepreneurs have the time to dedicate to such activities. That’s where a production monitoring system comes in, collecting crucial data from the facility in real-time and presenting it in a simplified manner to enable key decision-making. This blog post is entirely dedicated to the topic of production monitoring. Find out what you need to know about it.
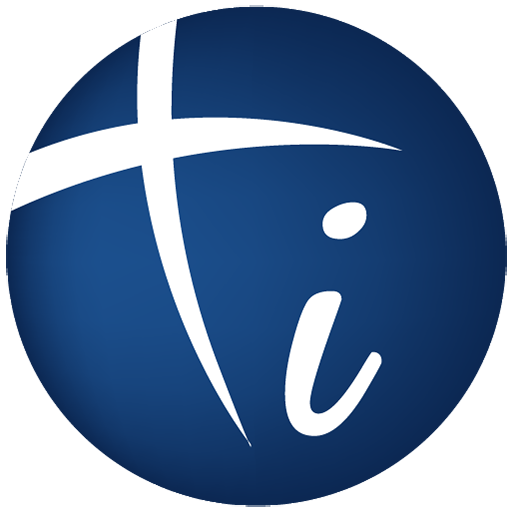
An Introduction to Production Monitoring
The primary task of production monitoring systems is to provide various parameters that allow entrepreneurs to draw conclusions and modify or improve specific areas of their business operations. These systems typically provide information about the state of production processes, the condition of equipment used, and the quality of the final product.
Methods of Tracking Production Processes
Now that you understand why data related to production processes in manufacturing facilities is collected, what are the most popular methods of production monitoring?
Traditional Monitoring Methods
Traditional methods of process monitoring in manufacturing facilities primarily rely on manual data collected by employees. In practice, a team member must manually record the number of products produced or the time spent on a particular task each day. This way, data on performance, quality, and work time is collected. However, this method of production monitoring has several drawbacks, such as the risk of data entry errors, a lack of access to real-time information, and an inability to quickly analyze and respond to problems quickly With this type of production monitoring, mistakes are highly likely. Additionally, it generates high costs for the business, as employees need to devote a significant amount of time and attention to manual data collection.
Modern Technologies and Monitoring Systems
Due to the high risk of errors associated with traditional production monitoring methods, more modern and technologically advanced systems have been implemented. Innovative solutions allow automatic data capture and real-time analysis. Information technology systems are used for this purpose, with their functionalities tailored to the specific needs of each company. Examples of modern solutions include ERP (Enterprise Resource Planning) and MES (Manufacturing Execution System), which enable the integration of various departments within the company and the collection of data on the performance of individual machines, employees, or the entire production process.
Recording Production Data
The key role of production monitoring systems is the ongoing recording of essential production data from the company’s perspective. Automatic collection of this information saves employees’ time, which can be devoted to tasks requiring more creativity, and minimizes the risk of errors. How does the data collection process work in advanced production monitoring systems?
Collecting Data from Various Sources
To gain a comprehensive understanding of a specific business’s operations, it is essential to collect data from as many sources as possible. This allows the owner of a manufacturing facility to make informed decisions, optimize costs, and effectively grow their company. Here are a few examples of sources and the data that can be collected:
- Machines – data that can be collected directly from machines, such as their performance, uptime, energy consumption, or temperature.
- Employees – data related to employees, such as working ours, productivity, or the number of errors made during production.
- Inventory – information about inventory levels, delivery time, or costs associated with storage and transportation of products can be collected from the warehouse.
- Customers – customer data includes order numbers, product preferences, or complaints.
- Quality – information about product quality can come from various sources, such as laboratory tests, durability tests, or quality control at different stages of production.
- Suppliers – supplier data includes factors such as quality, delivery timeliness, or transportation costs.
As you can see, there is quite an impressive number of sources from which data can be collected. The decision to automate the data collection process can lead to time savings and, consequently, cost savings (by optimizing employees’ working time). The IPLAS system is an innovative tool that allows business owners to monitor relevant data in real-time, resulting in the increased overall efficiency of the facility. Our specialists tailor the production monitoring system to the individual needs of each company, making it a valuable support for every business owner.
Analysis of Production Data
Data collection is one of the key functionalities of the production monitoring software. However, equally important is the accurate analysis of this data, enabling business owners to draw appropriate conclusions and make decisions regarding the company’s next steps is equally important. Modern systems present data in a way that facilitates interpretation, allowing quick identification of areas that require improvement within the company.
In the IPLAS system, every business owner can specify what data is collected and how it will be presented. Whether through charts, tables, or other types of templates, our solution enables companies to examine production data from the perspective that is crucial for their specific needs at any given time.
Managing production systems
Many business owners are apprehensive about transitioning to a new production system. The most significant concern is the time required to adapt to the changes. This reaction is entirely natural, as any modification to the existing routine requires effort from all employees, regardless of their position. However, it is crucial to think of the transition period as an investment – new habits will allow the company to develop more effectively and, ultimately, lead to cost savings.
Introducing the new production monitoring software should be done gradually. Emphasis should be placed on training and courses for all team members, ensuring that each employee gains the necessary knowledge to perform their duties in a different way than before. Business owners must be aware that mistakes are likely to occur during the initial stages. However, through learning from these mistakes, employees will undoubtedly draw conclusions more quickly and implement the necessary changes.
Choosing the right software
When selecting production data recording software, several factors should be considered, such as:
- Business requirements – Before choosing software, it is essential to determine the desired business objectives. Based on these requirements, the appropriate tool that best meets the company’s needs can be selected.
- Functionality – The software should have all the necessary features for monitoring production processes, including data collection and analysis, information visualization, and process automation.
- Integration with other systems – It is beneficial for the new tool to be capable of integrating(being integrated??) with other systems, such as ERP or MES systems, to enable comprehensive production management.
- Availability and technical support – It is important for the chosen software to be easily accessible and have a reliable technical support system to assist with problem-solving if needed.
Benefits of production monitoring
Choosing the right production monitoring system for a facility brings numerous benefits to the company. Such an investment can increase production efficiency and minimize costs associated with specific areas of the business. Continuous quality control of manufactured products reduces the risk of releasing defective items into the market.
Modern monitoring systems allow for continuous data collection and analysis, enabling the quick detection of issues in production processes and the implementation of corrective actions. Software designed for monitoring resource consumption automates production processes (such as transportation, storage, and production control), leading to increased efficiency and reduced human errors.
Furthermore, through real-time visualization of key information, managers have constant insight into production and can make prompt decisions. Lastly, but equally important, a well-selected production monitoring system can enhance a company’s competitiveness in the market, contributing to the overall business success.
+48 883 366 717