Introduction
On the basis of the experience we have gained by creating various types of systems for monitoring the consumption of technological media, in our test environment we have simulated the existence of two independent production plants (or units) with the aim of showing how, unknowingly, production companies lose a substantial amount of money due to the lack of optimization of energy consumption and resource consumption.
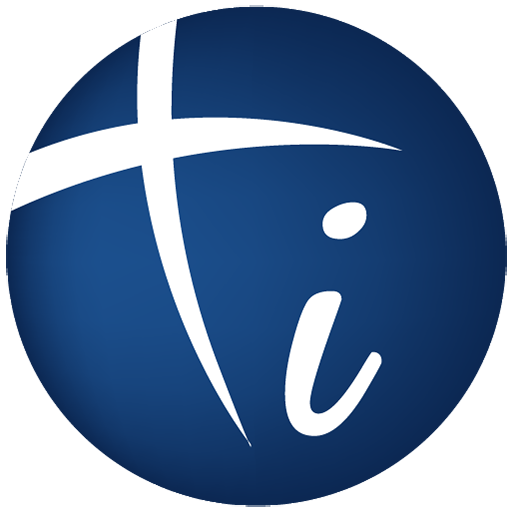
Historical background
Plant A
Plant A was established 10 years ago. The company gradually developed; compressed air was necessary to power the technological line. The compressed air installation as well as the compressor room were gradually expanded until reaching the target size – three screw compressors with a power of 40kW and a capacity of about 7.5 m3/h each. The compressors have been equipped with a superior control system controlling their operation – automatic activation depending on the demand of subsequent compressors. The system is also used to equalize the time courses of all devices, ensuring no large discrepancies in the operating hours. The devices function flawlessly and the entire system has been operating without any problems for years. Regular inspections and replacement of parts bring the desired results.
Plant B
The company develops rapidly and the need appears to increase production capacity. It already has a well-working and efficient technological layout, so a decision is made to copy the whole thing. Two years after the start of the investment process, production plant B is set up. It is equipped with a copy of the compressed air system from plant A. Due to the scale of the investment in the compressed air system, the supplier proposes to install a flow meter, in case there might be a need to measure the efficiency of the entire compressed air system in the future.
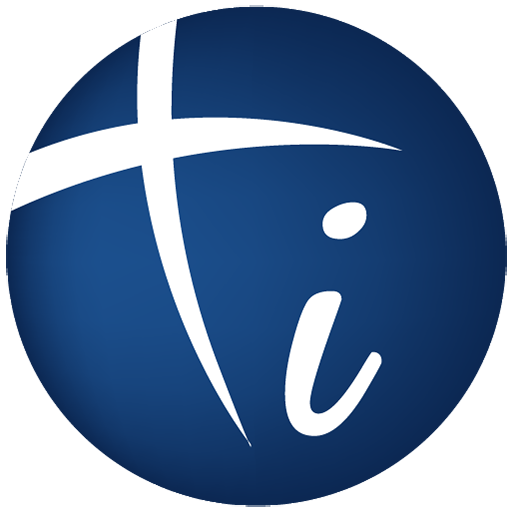
Current situation
Plant B starts operating in the target mode and soon its production results exceed those of Plant A – it coud be explained by using newer and more efficient equipment which apparently allows for the manufacturing of more products with the same amount of time and effort. Meanwhile, electricity costs start to skyrocket, at which point the Plant Manager remembers the “free” flow meter. It seems like the time for it to be used – this is when IPLAS comes into play. Having checked the communication capabilities, the flow meter starts sending data to the IPLAS system via the MODBUS protocol.
With the support of IPLAS architects, the first reports are created to monitor the temperature of compressed air coming out of the compressors, the flow rate in m3/min and the amount of daily m3 of air consumption.
Performance analysis of the installation in the production plant
The first analyzes are surprising. The system has a total capacity of about 23m3/min and the maximum instantaneous flows do not exceed 10m3/min.
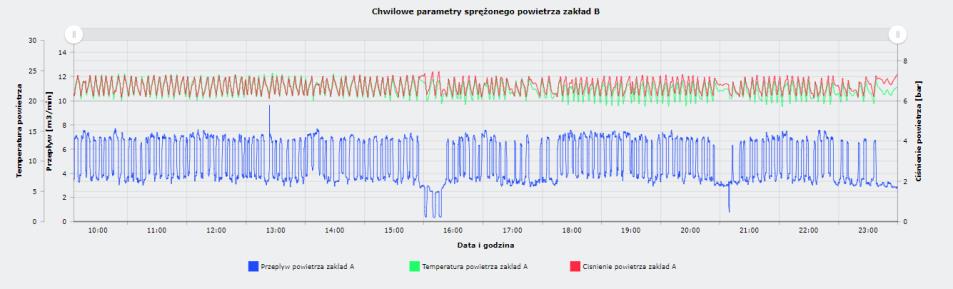
Jeszcze bardziej interesujące są te dane po uśrednieniu:
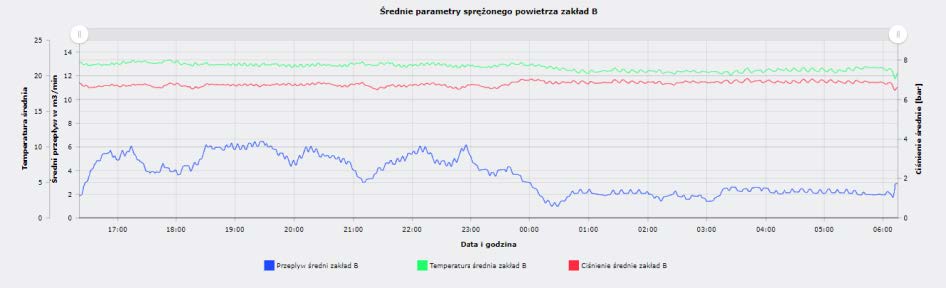
The Plant Manager starts to wonder and ask the question:
Why does the compressor room have a capacity of 23m3/min and an installed power of 120 kW when the actual demand for air is much lower? Where is the mistake? How to explain this? Have we overinvested?
How can you check if the new installation is efficient and economical? It’s simple. The IPLAS system records data in a continuous mode, which allows to see what both time courses look like during weekends and holidays. Owing to the fact that production equipment must be supplied with compressed air incessantly, the compressors run continuously.
Sunday is the day when Plant B is not working during the day, but the week starts with a night shift. This means that around 9-10 pm the air consumption starts to increase to reach the maximum average consumption in the middle of the shift (about 6 m3/min):
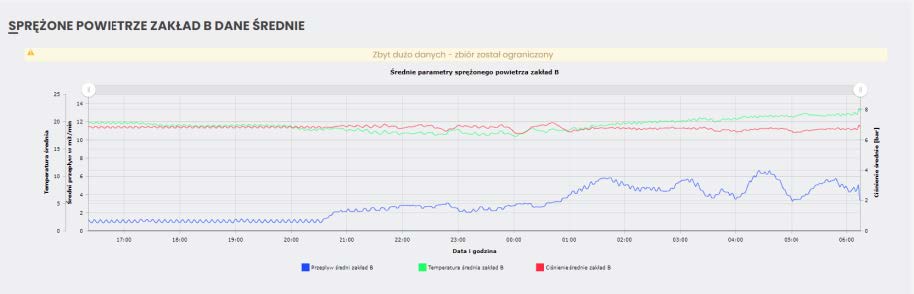
On a day off from work, an average of 0.6 m3/min flows out of the compressors – this is a very good result and relatively small loss in the compressed air system.
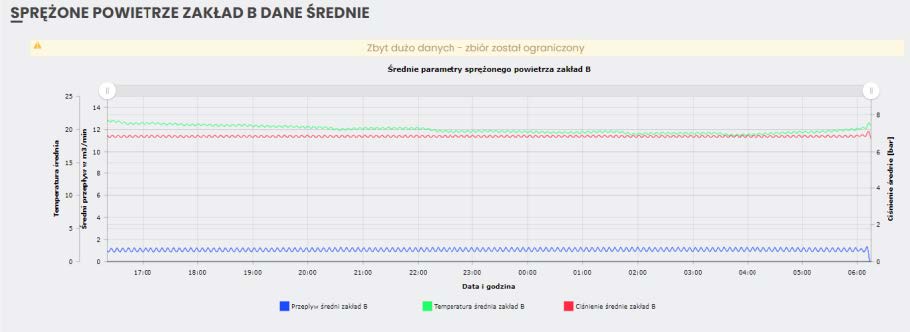
Plant Manager shares his observations with the counterpart from Plant A and together they make a decision to install the flow meter in Plant A as well. Two months later, the first data is collected and the comparison may start.
Regular production day:
Instantaneous flow values are up to 15m3/min and the average values are 10m3/min – charts below.
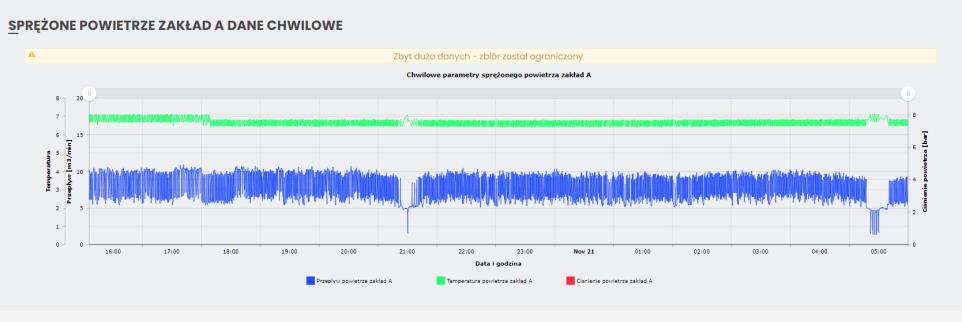
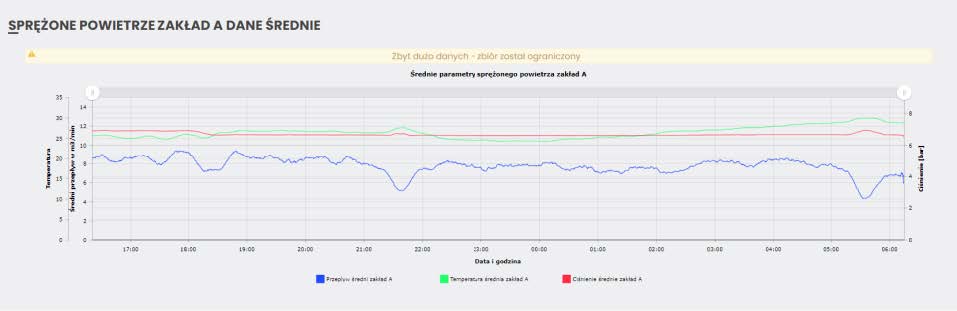
Due to a different specificity, when comparing Plant A, the data measured on Saturday is used – work on the first shift until 2pm.
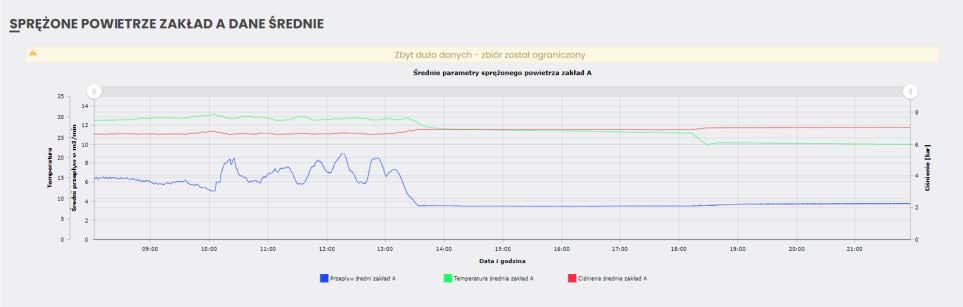
An empty Plant A has a compressed air consumption of 4 m3/min. This is a colossal difference compared to Plant B.
Summarizing the consumption in IPLAS, the managers have been able to see the difference:
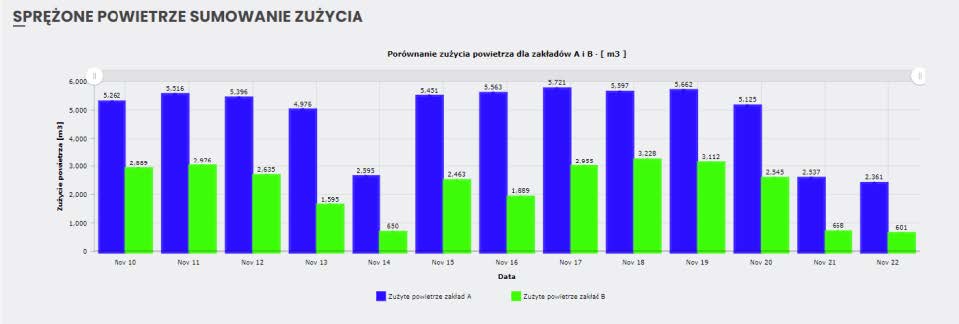
Dodatkowo porównanie kosztów:
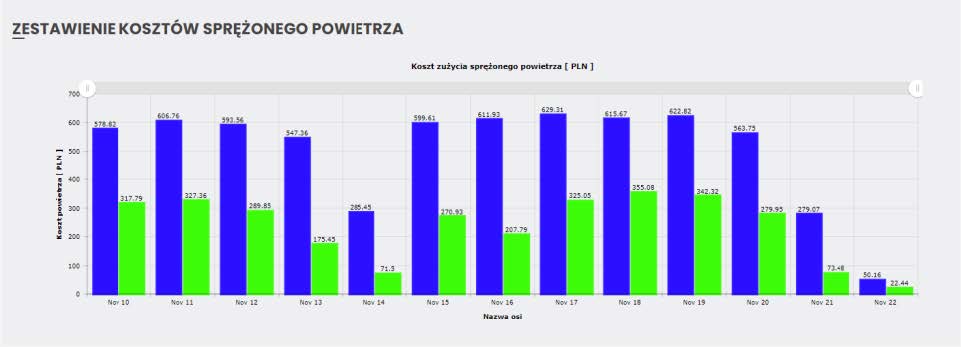
The differences in daily consumption are huge, which translates into much lower costs of producing compressed air. Assuming an average daily difference in consumption of about PLN 250-300, Plant B saves about PLN 90,000 to PLN 110,000 annually.
Where do such differences come from? These are the losses generated by the installation. All kinds of leaks and connection errors for 10 years of operation of Plant A have led to the unconscious purchase of an additional compressor, whose main task has been to replenish losses – 24 hours a day, 365 days a year. This is an obvious loss and one can only guess how long it may last.
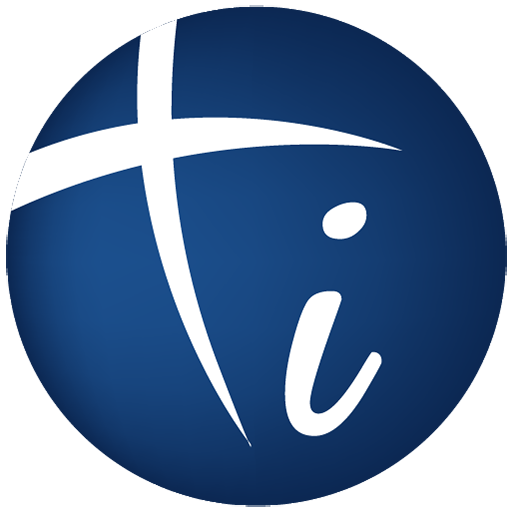
Two ways to control the efficiency of devices in the production plant
- Services of external companies involving the periodic installation of various types of measurement systems. Those, unfortunately, most often consist in copying digital signals from either contactors or solenoid valves which activate the compressor discharge/idle run. Sadly, there is no continuous monitoring and therefore it renders detection of a sudden deterioration in the condition of the installation impossible.
2. Investing in your own flowmeter and connecting it to the IPLAS system. This solution offers:- Continuous and independent measurement that is automatically archived. Access to reports from anywhere in the world.
- Automatic conversion of air consumption into kWh or PLN
- Control of the level of air consumption on non-working days – IPLAS can automatically examine the consumption/flow and inform when the set thresholds are exceeded. Thus, the reaction can be immediate
- Initial location of leak areas – when the installation is divided, part of it can be cut off and it is possible to check the amount of flow/loss. This is the first stage of locating the leak, subsequently professional leak detectors must be used.
- Continuous and independent measurement that is automatically archived. Access to reports from anywhere in the world.
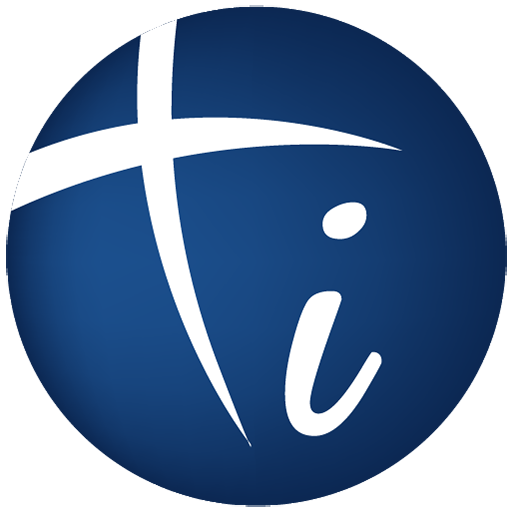
Case study summary
The situation described here is a model prepared for the needs of Case Study and our DEMO, and it is based on some of the real-life situations we have encountered during the implementation of tasks entrusted by our clients. Many of them are not aware of the great losses they suffer. Seemingly, everything works very well, but there is still room for improving the situation and it is possible to take control over the entire manufacturing process at a low cost. By connecting energy consumption meters to each compressor separately, it can be easily determined how much it costs to produce compressed air in relation to, for example, production volume. The possibilities are endless, while the potential initial cost remains low.
+48 883 366 717