Wstęp
Cyfrowy bliźniak (ang. Digital Twin) to niezwykle szczegółowy wirtualny model odzwierciedlający fizyczny obiekt, system lub proces. Tworzy się go na podstawie strumienia danych z czujników i systemów przemysłowych, dzięki czemu wirtualna replika potrafi odtworzyć rzeczywiste warunki, zachowanie i wydajność maszyn lub linii produkcyjnej w świecie cyfrowym. W przemyśle – od dużych fabryk po średnie zakłady – technologia ta odgrywa coraz większą rolę jako fundament koncepcji Przemysłu 4.0 i inteligentnej produkcji, umożliwiając monitorowanie operacji w czasie rzeczywistym, analizę “co by było gdyby” oraz ciągłe doskonalenie procesów.
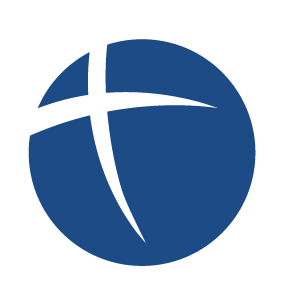
Rola cyfrowego bliźniaka w przemyśle
Cyfrowe bliźniaki stanowią wirtualne odpowiedniki fizycznych fabryk, maszyn lub procesów, działające w oparciu o rzeczywiste dane. Ich zadaniem jest łączenie świata realnego z cyfrowym w cyklu ciągłego sprzężenia zwrotnego: dane z sensorów i systemów produkcyjnych zasilają model cyfrowy, który odzwierciedla bieżący stan i zachowanie obiektu, a następnie wnioski i optymalizacje z modelu można przenieść z powrotem na produkcję. Taka dwukierunkowa wymiana informacji pozwala nie tylko monitorować procesy, ale też przewidywać przyszłe stany i wyniki. Przykładowo, producent może stworzyć cyfrowego bliźniaka swojej linii montażowej, aby obserwować wirtualnie przebieg produkcji i wprowadzać usprawnienia, zanim zastosuje je fizycznie. W efekcie decyzje opierają się na danych i symulacjach zamiast na intuicji, co zwiększa ich trafność i szybkość. Według Siemens, cyfrowe bliźniaki są dziś wykorzystywane w wielu branżach do symulowania i optymalizacji produktów oraz systemów produkcyjnych jeszcze przed inwestycją w fizyczne prototypy – pozwala to zrozumieć i przewidzieć wydajność rzeczywistych obiektów bez ponoszenia kosztów eksperymentów w realu.
Cyfrowy bliźniak w praktyce może dotyczyć zarówno pojedynczej maszyny, całego ciągu technologicznego, jak i nawet całej fabryki lub zakładu. Gartner wyróżnia np. bliźniaki dyskretne (poziomu komponentu lub urządzenia), bliźniaki systemów (obejmujące zestaw maszyn lub proces), a także bliźniaki organizacji (odwzorowujące całe przedsiębiorstwo). W kontekście produkcji najczęściej spotykamy się z modelami odwzorowującymi pracę maszyn i linii (np. prasy, pieca, tokarki, linii pakującej) lub całych wydziałów. W każdym przypadku cel jest podobny: lepsze zrozumienie procesu i możliwość interaktywnej pracy z nim w świecie wirtualnym, zanim podejmie się działania w świecie rzeczywistym.
Cyfrowy bliźniak zakładu produkcyjnego umożliwia wizualizację danych operacyjnych w czasie rzeczywistym i testowanie zmian procesu w środowisku wirtualnym (na ilustracji: platforma DELMIA prezentująca “wirtualne uruchamianie” linii produkcyjnej). Dzięki takiej integracji świata fizycznego z cyfrowym, kierownictwo może obserwować pracę maszyn na ekranie tabletu i od razu identyfikować obszary do usprawnienia bez zakłócania pracy fabryki. Rola cyfrowego bliźniaka w przemyśle obejmuje zatem wiele aspektów: od bieżącego nadzoru i sterowania (real-time monitoring) po planowanie i optymalizację. Pozwala on inżynierom i menedżerom zadawać pytania “co, jeśli…?” i natychmiast uzyskiwać odpowiedzi z modelu – np. co się stanie z wydajnością linii produkcyjnej po zwiększeniu prędkości przenośnika o 10% albo jak awaria konkretnego urządzenia wpłynie na całkowitą produkcję w ciągu dnia.
W efekcie cyfrowy bliźniak staje się narzędziem wspierania decyzji: integruje dane z wielu źródeł (produkcja, utrzymanie ruchu, jakość, energetyka) i prezentuje je w przystępnej formie, często z wykorzystaniem wizualizacji 3D lub paneli kontrolnych. Jak zauważa magazyn Automation World, kluczowe jest tu posiadanie “danych umożliwiających działanie”, co pozwala lepiej planować i realizować cele biznesowe oraz cele zrównoważonego rozwoju. Dzięki cyfrowym bliźniakom firmy mogą bowiem walidować i optymalizować projekty, przeprowadzać zdalny rozruch maszyn (virtual commissioning) oraz doskonalić procesy produkcyjne, utrzymanie ruchu i łańcuchy dostaw – wszystko to najpierw w świecie wirtualnym.
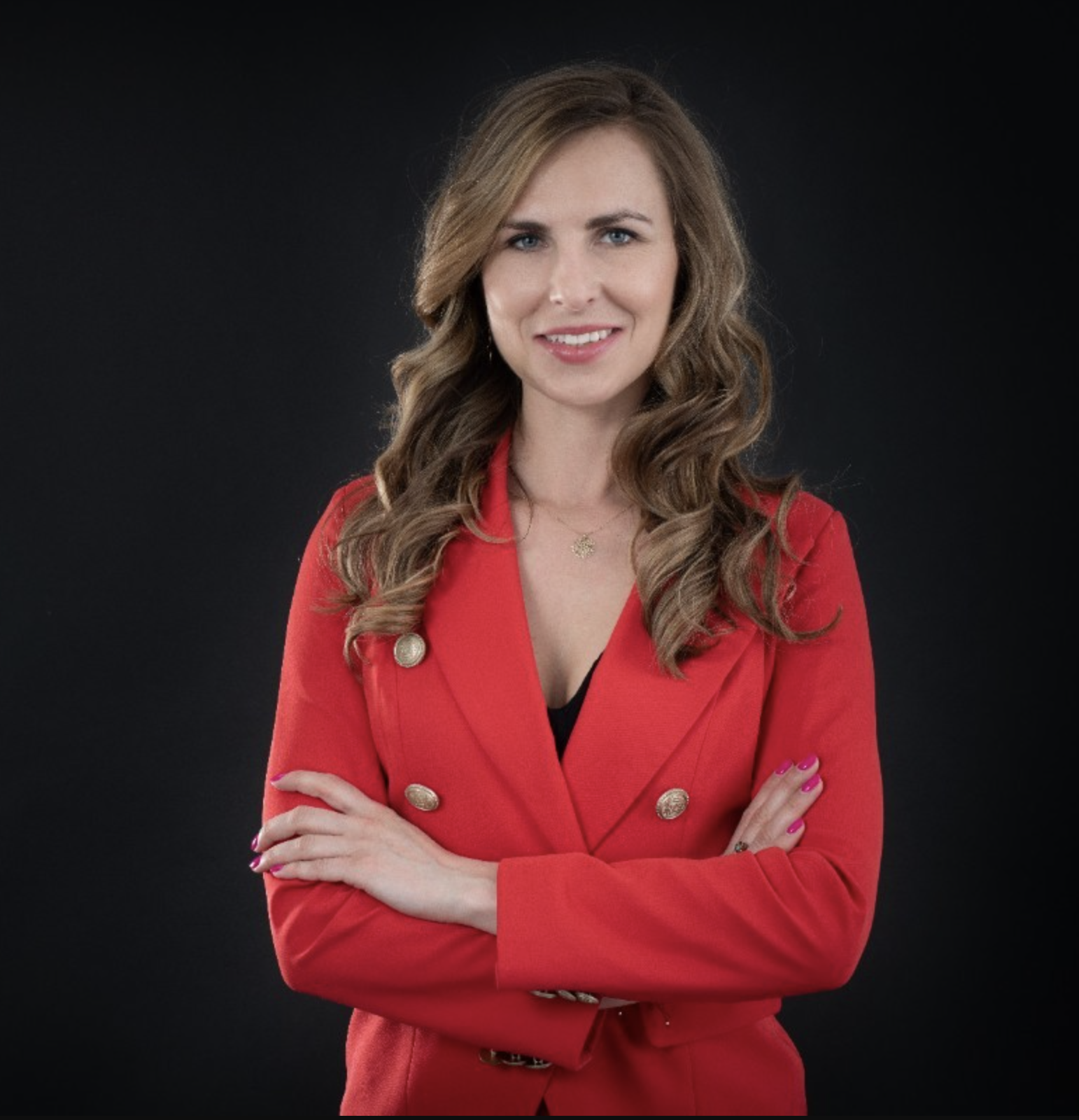
Monika Nowak
Dyrektor projektu iPLAS
Zbieraj dane z całej produkcji w jednym miejscu
iPLAS integruje dane z maszyn, procesów automatycznych i manualnych w czasie rzeczywistym. Bezpiecznie przechowujemy je w chmurze lub na Twoim serwerze, a dzięki zaawansowanemu przetwarzaniu danych zyskasz pełen wgląd w swoją produkcję.
Symulacja różnych scenariuszy z użyciem Digital Twin
Jedną z najważniejszych możliwości, jakie daje cyfrowy bliźniak, jest symulowanie rozmaitych scenariuszy operacyjnych. Oznacza to, że firma może przetestować w wirtualnym modelu sytuacje, które w realnej fabryce byłyby trudne, kosztowne lub ryzykowne do odtworzenia. Digital Twin umożliwia np. zasymulowanie:
- Awarii kluczowej maszyny lub linii produkcyjnej – model cyfrowy potrafi naśladować zachowanie systemu w razie unieruchomienia pewnego elementu. Możemy sprawdzić, jak zatrzymanie np. pieca hutniczego czy robota pakującego wpłynie na cały ciąg produkcji: czy inne maszyny przejmą obciążenie, gdzie powstaną wąskie gardła, ile produktów nie zostanie wyprodukowanych i jakie będą opóźnienia. Dzięki temu zespół jest lepiej przygotowany na realną awarię, mając gotowe plany awaryjne. Według badań, firmy wykorzystują bliźniaki cyfrowe, aby przewidywać i łagodzić skutki zakłóceń, identyfikować z wyprzedzeniem wąskie gardła oraz utrzymywać wymaganą przepustowość produkcji.
- Nagłego wzrostu obciążenia lub popytu – wirtualna fabryka pozwala przetestować scenariusz, w którym zamówienia skokowo rosną (np. wskutek sezonowego popytu lub dużego zlecenia). Kierownictwo może zwiększyć w symulacji tempo pracy maszyn, dodać wirtualną zmianę produkcyjną lub włączyć dodatkowe linie i od razu zobaczyć, gdzie pojawią się ograniczenia przepustowości (np. czy pakowalnia nadąży za produkcją, czy magazyn pomieści wyroby). Takie symulacje podpowiadają, czy i kiedy warto zainwestować w nowe moce produkcyjne, pozwalając lepiej zaplanować inwestycje kapitałowe. Co więcej, cyfrowy bliźniak może wskazać optymalne parametry produkcji przy wyższym obciążeniu – np. jak zmodyfikować harmonogram maszyn, by zminimalizować czasy przezbrojeń przy wzroście zamówień.
- Zmian w procesie technologicznym lub asortymencie – zanim wprowadzi się zmianę receptury produktu, nowy model wyrobu lub zmodyfikuje parametry procesu, można to zasymulować. Przykładowo, firma spożywcza planująca przejście na nowe opakowanie może w cyfrowym bliźniaku sprawdzić, czy obecne linie pakujące poradzą sobie z innym formatem opakowania, czy potrzebne będą przeróbki maszyn, a także ile to potencjalnie zajmie czasu i będzie kosztować (np. w postaci przestojów). Wirtualny model linii produkcyjnej pozwala ocenić konsekwencje zmian bez przerywania rzeczywistej pracy. Analogicznie, zmiana ustawień procesowych (np. temperatury pieca w hucie szkła czy prędkości taśmy produkcyjnej) może zostać przetestowana cyfrowo – zobaczymy wpływ na wydajność, zużycie energii, jakość produktu itp. i wybierzemy optymalne parametry.
- Ekstremalnych warunków operacyjnych – cyfrowy bliźniak daje możliwość zasymulowania sytuacji rzadkich lub skrajnych, takich jak praca urządzenia w warunkach ponadnormatywnych. Jedna z głównych zalet Digital Twin w utrzymaniu ruchu to możliwość testowania różnych warunków pracy maszyny – np. sprawdzenia, jak zachowa się silnik, gdy temperatura otoczenia przekroczy 40°C albo jak prasa poradzi sobie przy szczególnie wysokim obciążeniu. Pozwala to zidentyfikować limity wydajności i newralgiczne punkty systemu w bezpiecznych warunkach symulacji. Inżynierowie mogą z wyprzedzeniem wychwycić potencjalne słabe ogniwa – elementy, które jako pierwsze ulegną przeciążeniu lub zużyciu przy ekstremalnej eksploatacji – i zaplanować odpowiednie działania (np. dodatkowe chłodzenie, częstsze przeglądy, modernizację komponentu).
- Różnych strategii produkcyjnych lub logistycznych – cyfrowe bliźniaki sprawdzają się nie tylko w symulowaniu zdarzeń awaryjnych, ale także w testowaniu alternatywnych sposobów prowadzenia produkcji. Przykładowo, zakład może zasymulować zmianę kolejności operacji technologicznych, wdrożenie innego harmonogramu produkcji lub reorganizację layoutu hali i zobaczyć, jaki to przyniesie efekt. W obszarze łańcucha dostaw bliźniaki potrafią odzwierciedlić cały przepływ materiałów i produktów, umożliwiając testowanie scenariuszy w stylu “co jeśli dostawca X zawiedzie” lub “co jeśli popyt na produkt Y wzrośnie o 50%”. Dzięki temu firmy mogą lepiej przygotować się na niepewne czasy – jak wskazuje raport Deloitte, technologia cyfrowych bliźniaków jest obecnie przemyślana na nowo właśnie po to, by symulować kluczowe decyzje strategiczne i pomagać firmom nawigować w warunkach niepewności. Innymi słowy, od poziomu hali produkcyjnej aż po poziom zarządzania strategicznego, symulacje na bliźniakach cyfrowych ułatwiają przewidywanie skutków decyzji w różnych scenariuszach otoczenia biznesowego.
Wszystkie powyższe przykłady łączy wspólny mianownik: możliwość bezpiecznego eksperymentowania na wirtualnym obiekcie zamiast na fizycznym. To trochę jak symulator lotu w lotnictwie – pilot może przećwiczyć sytuacje awaryjne w symulatorze, co przygotuje go na realny lot. Podobnie, zespół produkcyjny może w symulatorze fabryki przetestować awarię czy zmianę procesu, dzięki czemu w rzeczywistości nie zostanie zaskoczony i będzie dysponował zweryfikowanymi rozwiązaniami.
Korzyści z testowania scenariuszy „na sucho”
Dlaczego warto przeprowadzać testy „na sucho” na cyfrowych bliźniakach? Istnieje szereg wymiernych korzyści biznesowych wynikających z takiego podejścia:
Ograniczenie ryzyka i awarii
Najbardziej oczywistym plusem jest minimalizacja ryzyka niepowodzeń przy wprowadzaniu zmian. Zanim firma zainstaluje nową linię technologiczną, zmieni parametry procesu czy wprowadzi innowację, może przetestować to cyfrowo. Jeśli symulacja wykaże problemy (np. że nowy układ maszyn powoduje zatory), unikniemy kosztownego błędu w realnej skali. Jak podkreślają eksperci BCG, przedsiębiorstwa wykorzystują cyfrowe bliźniaki do przewidywania ryzyka i potencjalnych zatorów, co przekłada się na mniejsze opóźnienia i wyższy poziom niezawodności dostaw. Innymi słowy, dzięki bliźniakom uczymy się na błędach popełnionych w wirtualnym świecie, a do rzeczywistości wprowadzamy już rozwiązania pozbawione wykrytych wad. Redukuje to ryzyko awarii i przestojów, bo wiele problemów zostaje wyeliminowanych zawczasu, na etapie testów symulacyjnych.
Niższe koszty i oszczędność zasobów
Przeprowadzanie prób i eksperymentów w realnej fabryce bywa bardzo drogie: zużywa się materiały, energię, czas pracy ludzi i obciąża maszyny. Co gorsza, nieudany eksperyment może spowodować uszkodzenia sprzętu lub produkcję dużej partii braków. Bliźniak cyfrowy umożliwia przeniesienie tych testów do świata wirtualnego, gdzie koszt dodatkowej symulacji jest praktycznie zerowy. Jak zauważa inżynier firmy Dassault Systèmes, przeniesienie testów i walidacji do sfery cyfrowej jest znacznie mniej kosztowne niż wyłapywanie problemów dopiero na fizycznej linii produkcyjnej – dodatkowo skraca to łączny czas wdrożenia zmian. Innymi słowy, zamiast metodą prób i błędów w realu (co może generować straty), lepiej przeprowadzić dziesiątki symulacji „na sucho” i znaleźć optymalne rozwiązanie przy minimalnym zużyciu zasobów. Pewne studium World Economic Forum potwierdza, że fabryki wdrażające bliźniaki cyfrowe potrafią zmniejszyć zużycie energii o 30%, ograniczyć marnotrawstwo surowców i jednocześnie obniżyć koszty, osiągając lepszą efektywność ekonomiczną i ekologiczną równocześnie.
Szybsze podejmowanie decyzji
W tradycyjnym ujęciu przygotowanie analizy czy prognozy dla skomplikowanego procesu zajmowało tygodnie lub miesiące (zbieranie danych, budowa modeli w arkuszach kalkulacyjnych, testy pilotowe). Cyfrowe bliźniaki drastycznie przyspieszają ten cykl – dzięki zautomatyzowanym symulacjom i ciągłemu dostępowi do aktualnych danych, menedżerowie mogą uzyskać odpowiedzi na “What if?” w ciągu godzin, a nawet minut, zamiast tygodni. W rezultacie decyzje inwestycyjne czy operacyjne mogą zapaść znacznie szybciej, co jest kluczowe w dynamicznym otoczeniu rynkowym. Jak zwraca uwagę jeden z liderów transformacji cyfrowej, jeszcze niedawno opracowanie pełnej analizy scenariuszowej trwało miesiącami, a dziś za pomocą modelu cyfrowego można przeprowadzić kilkanaście różnych scenariuszy w ciągu jednego dnia. Ta szybkość dostarczania informacji zwrotnych przekłada się na zwinność biznesową – firmy mogą reagować na zmiany warunków natychmiastowymi decyzjami popartymi symulacjami, zamiast działać na wyczucie lub z opóźnieniem.
Lepsze planowanie inwestycji i zasobów
Testowanie „na sucho” pozwala podejmować trafniejsze decyzje dotyczące alokacji kapitału i zasobów. Przykładowo, jeśli rozważamy zakup nowej maszyny, możemy w modelu ocenić, czy rzeczywiście zwiększy ona wąskie gardło produkcji i o ile skróci czas cyklu – może się okazać, że lepszy efekt da inna inwestycja (np. dodatkowy operator lub modernizacja innego etapu procesu). Symulacje pomagają priorytetyzować wydatki na te obszary, które przyniosą największy zwrot. Również w planowaniu długoterminowym (np. budowy nowej hali, rozbudowy mocy) bliźniak cyfrowy bywa nieoceniony: można zbudować cyfrowy model planowanej fabryki i sprawdzić różne warianty layoutu i wyposażenia, wybierając najbardziej efektywny. BCG opisuje podejście “digital-first”, gdzie niektórzy producenci najpierw optymalizują wirtualny system produkcyjny, a dopiero potem odtwarzają go fizycznie, dzięki czemu unikają kosztownych przeróbek – to odwrócenie tradycyjnej kolejności przynosi wymierne oszczędności i redukuje ryzyko błędnych inwestycji.
Doskonalenie procesów i produktywności
Sam fakt istnienia cyfrowego bliźniaka zmusza organizację do głębszego zrozumienia swoich procesów (modelowania ich) i zbierania wysokiej jakości danych. Już to często ujawnia ukryte rezerwy. Ponadto symulacje pozwalają wygenerować usprawnienia, które trudno byłoby odkryć bez takiego narzędzia. Na przykład optymalizacja harmonogramu produkcji czy ustawień maszyn poprzez testowanie tysięcy kombinacji w modelu może przynieść dodatkowe kilka procent wydajności więcej, niż osiągamy dotąd. W jednym z wywiadów eksperci podkreślają, że bliźniak cyfrowy dostarcza szczegółowych spostrzeżeń i prognoz opartych na danych, które są nieocenione w planowaniu strategicznym, a cyfrowy model staje się wręcz katalizatorem wewnętrznych usprawnień. W praktyce oznacza to np. szybsze usuwanie problemów jakościowych, krótsze przestoje dzięki predykcji awarii (o czym niżej) czy skrócenie czasu wprowadzania nowych produktów na rynek. Ta ostatnia kwestia jest szczególnie istotna: cyfrowy bliźniak pozwala przeprowadzić wirtualne testy prototypów i procesów produkcyjnych dla nowego wyrobu, co może znacząco skrócić fazę uruchomienia – zanim zbudujemy fizyczne przyrządy i narzędzia, mamy już zoptymalizowany proces wirtualny gotowy do wdrożenia.
Poprawa komunikacji i podejścia do innowacji
Warto wspomnieć też o miękkich korzyściach. Posiadając cyfrowy model, łatwiej jest komunikować się między działami (produkcja może np. pokazać działowi inwestycji albo zarządowi zasymulowane efekty planów – to bardziej przekonujące niż raport na papierze). Bliźniaki sprzyjają też kulturze innowacyjności – pracownicy chętniej eksperymentują i zgłaszają usprawnienia, gdy mają możliwość sprawdzenia pomysłu na modelu bez strachu przed konsekwencjami niepowodzenia. Ponadto, modele 3D i wirtualne symulacje ułatwiają szkolenia nowych pracowników – mogą oni uczyć się obsługi skomplikowanych maszyn lub reagowania na sytuacje awaryjne w VR/AR (wirtualnej lub rozszerzonej rzeczywistości) sprzężonej z cyfrowym bliźniakiem, co podnosi ich kompetencje bez ryzyka dla prawdziwej linii produkcyjnej.
Podsumowując, testowanie scenariuszy „na sucho” na cyfrowym bliźniaku to podejście zapewniające bezpieczną przestrzeń do eksperymentów, dające szybkie odpowiedzi i minimalizujące koszty błędów. Dla decydentów i menedżerów oznacza to większą pewność decyzji i tempo działania, a dla przedsiębiorstwa – bardziej efektywne i odporne operacje. W istocie, jak celnie ujęto w jednym z raportów, to właśnie możliwość przeprowadzania scenariuszy testowych bez kosztów i ryzyka realnych eksperymentów jest najsilniejszą stroną cyfrowych bliźniaków.
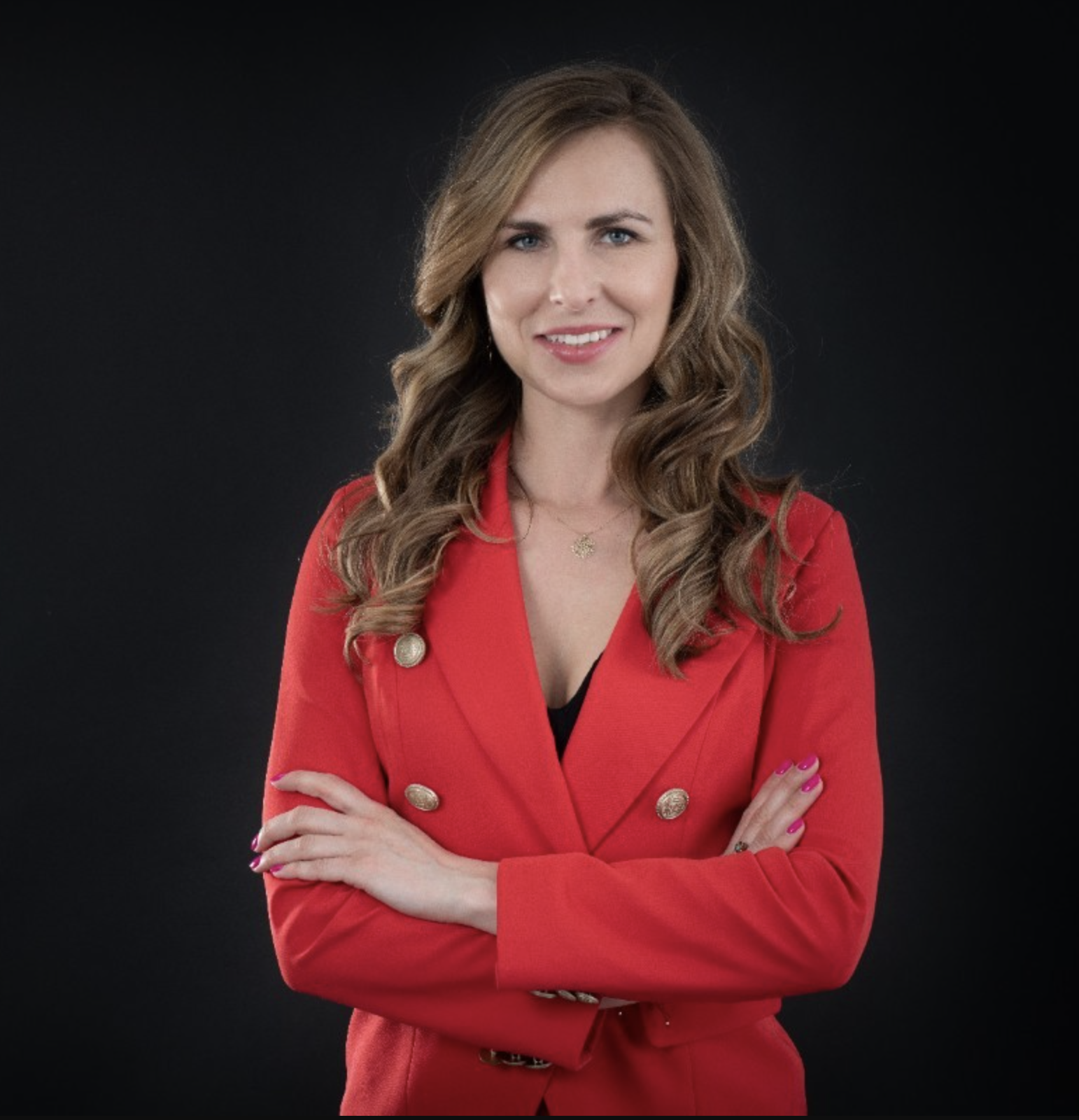
Monika Nowak
Dyrektor projektu iPLAS
Zbieraj dane z całej produkcji w jednym miejscu
iPLAS integruje dane z maszyn, procesów automatycznych i manualnych w czasie rzeczywistym. Bezpiecznie przechowujemy je w chmurze lub na Twoim serwerze, a dzięki zaawansowanemu przetwarzaniu danych zyskasz pełen wgląd w swoją produkcję.
Przykłady zastosowania cyfrowego bliźniaka – scenariusze hipotetyczne
Aby lepiej zilustrować praktyczne zastosowanie tej technologii, rozważmy dwa hipotetyczne przykłady firm produkcyjnych – pierwsza z branży szklarskiej, druga z sektora spożywczego. Choć to różne obszary przemysłu, w obu przypadkach cyfrowy bliźniak może przynieść wymierne korzyści poprzez symulację i optymalizację procesów.
Przykład 1: Fabryka szyb zespolonych (szkło izolacyjne).
Wyobraźmy sobie średniej wielkości zakład produkujący szyby zespolone do okien. Proces obejmuje cięcie szkła, mycie, łączenie tafli z ramką dystansową i uszczelnianie. W takiej fabryce krytycznym sercem jest piec do zgrzewania szyb (autoklaw) oraz linia montażu. Firma wdraża cyfrowy bliźniak swojej linii produkcyjnej, odwzorowując w modelu m.in. piec, stoły montażowe, roboty nakładające uszczelnienie i magazyn wyrobów gotowych.
Symulacja awarii pieca: Piec autoklawowy jest newralgiczny – jego awaria oznacza zatrzymanie produkcji. Bliźniak cyfrowy pozwala zasymulować scenariusz, w którym piec niespodziewanie przestaje działać na 8 godzin. W modelu widać, jak szybko zapełniają się bufory półproduktów przed piecem, po jakim czasie brakuje miejsca na hali i które zamówienia będą opóźnione. Symulacja sugeruje, że po 3 godzinach przerwy cały przepływ się blokuje. Dzięki temu firma opracowuje plan awaryjny: np. decyzję o przekierowaniu części produkcji do zaprzyjaźnionego zakładu partnerskiego, gdyby awaria potrwała dłużej niż 2 godziny, albo przygotowanie dodatkowego mobilnego regału na tymczasowe magazynowanie szyb czekających na zgrzanie. Bliźniak pozwala również przetestować różne warianty reakcji (np. skierowanie pracowników do innych zadań w czasie awarii, aby nie tracić efektywności) i wybrać najlepszy.
Optymalizacja wydajności linii: Zakład chce zwiększyć dzienną produkcję szyb o 15% w odpowiedzi na rosnące zamówienia. Zamiast od razu inwestować w nowy piec (kosztowny) czy dodatkową zmianę, najpierw wykorzystuje cyfrowy bliźniak do wyszukania rezerw. Symulacje ujawniają, że wąskim gardłem nie jest piec (ma pewną niewykorzystaną przepustowość), ale sekcja składania ramek i mycia szkła – tam tworzą się kolejki. Model testuje kilka usprawnień: dodanie drugiego stanowiska mycia, skrócenie czasu ustawiania ramek poprzez przeprogramowanie robota, zmiana logistyki dostarczania szkła na linię. Po sprawdzeniu kombinacji pomysłów bliźniak wskazuje optymalny plan: dołożenie jednego operatora przy stacji ramek i drobna modyfikacja sekwencji pracy robota uszczelniającego dają 10% wzrostu wydajności bez inwestycji w nowy sprzęt. Resztę brakującej zdolności firma postanawia uzyskać, wydłużając nieco pracę pieca w nadgodzinach, co również zasymulowano (wpływ na koszty energii i eksploatację pieca okazał się akceptowalny). Dzięki digital twin przedsiębiorstwo uniknęło pochopnego zakupu nowej maszyny za kilkaset tysięcy złotych – zamiast tego zoptymalizowało istniejący proces.
Poprawa jakości i redukcja braków: Model cyfrowy pozwolił także analizować, gdzie powstają ewentualne wady szyb (np. zanieczyszczenia między taflami). Zbierając dane o każdej sztuce (np. pomiary czystości, wilgotności, temperatury na poszczególnych etapach) i łącząc je w bliźniaku, odkryto korelację: najwięcej reklamacji dotyczy szyb produkowanych tuż po przerwie obiadowej. Symulacja zachowania cząstek kurzu i przepływów powietrza w hali zasugerowała przyczynę – wzmożony ruch pracowników po przerwie podnosi kurz, który trafia między tafle przed zgrzewaniem. Wirtualny eksperyment z instalacją dodatkowej kurtyny powietrznej przy wejściu na halę wykazał znaczącą poprawę. Firma wdrożyła tę zmianę realnie i odnotowała spadek braków o połowę. Ten przykład pokazuje, że cyfrowy bliźniak może służyć nie tylko wielkim strategiom, ale i drobnym usprawnieniom poprawiającym jakość oraz ograniczającym straty materiałowe.
Przykład 2: Zakład pakujący żywność.
Rozważmy średniej skali firmę, która zajmuje się konfekcjonowaniem i pakowaniem żywności (np. pakowanie orzechów, suszonych owoców i bakalii do torebek). Taki zakład ma kilka równoległych linii pakujących, na których produkty są dozowane, ważone, wsypywane do opakowań i zgrzewane. Jest też etykietowanie i kartonowanie do wysyłki. Firma postanawia wykorzystać cyfrowego bliźniaka do poprawy efektywności i elastyczności swojego procesu, szczególnie że popyt na produkty jest sezonowy (szczyt przed świętami).
Harmonogramowanie produkcji i zmiany asortymentu: Cyfrowy bliźniak linii pakujących pozwala zasymulować różne plany produkcyjne. W modelu można wprowadzić np. że w tym tygodniu 70% produkcji to mieszanki orzechowe w małych paczkach, a 30% – suszone owoce w dużych paczkach, a w następnym tygodniu odwrotnie, i zobaczyć jak przebalansować obłożenie linii. Symulacje wykazały, że częste przełączanie linii na inny produkt generuje straty czasu na przezbrojenia (czyszczenie, zmiana ustawień maszyn dozujących). Model zasugerował bardziej efektywny harmonogram: grupowanie produkcji produktów podobnych (np. najpierw seria wszystkich małych opakowań orzechów, potem zmiana formatów i seria dużych opakowań owoców) minimalizuje liczbę zmian formatów. Dzięki temu realnie udało się zwiększyć wydajność pakowania o ~8% w skali miesiąca, bo czas przestojów na przezbrojenia się zmniejszył. Co ważne, bliźniak pokazał też wpływ takiego planu na czasy realizacji zamówień poszczególnych klientów – pozwolił więc znaleźć kompromis między efektywnością produkcji a terminowością dostaw.
Symulacja awarii maszyny pakującej: W zakładzie stoi kilka automatycznych pakowaczek. Awaria jednej z nich w sezonie wzmożonych zamówień mogłaby utrudnić wywiązanie się z dostaw. Firma wykorzystała bliźniaka do symulacji scenariusza: co jeśli jedna z maszyn (np. linia nr 3) padnie na dwa dni? Model pokazał, że pozostałe linie mogą przejąć tylko około 60% wolumenu z uszkodzonej linii, mimo pracy na 3 zmiany – czyli produkcja spadnie o ok. 40%, co grozi opóźnieniami. Jednak symulując dalej, znaleziono rozwiązanie: tymczasowe przezbrojenie jednej z linii (nr 2) na “dwupak”, czyli jednoczesne pakowanie dwóch mniejszych porcji w jeden większy worek (co podwaja wydajność maszynową, choć wymaga dodatkowego ręcznego rozdzielenia później). Taka niekonwencjonalna opcja została przetestowana w cyfrowym bliźniaku i okazała się możliwa – wymagała zmiany oprogramowania maszyny i dodatkowych prac ręcznych, ale pozwalała utrzymać 90% normalnej produkcji. Firma przygotowała z góry procedurę i przeszkolenie załogi na taką ewentualność, co istotnie zwiększyło odporność operacji. Gdy po kilku miesiącach faktycznie doszło do awarii jednej z linii, plan awaryjny wdrożono w ciągu kilku godzin, minimalizując straty produkcyjne.
Optymalizacja zużycia materiałów i kontrola jakości: Cyfrowy bliźniak pomógł także w analizie zużycia materiałów opakowaniowych i jakości pakowania. Symulując różne ustawienia maszyn dozujących i zgrzewających, odkryto np. że zmniejszenie tolerancji odważania produktu (bardziej precyzyjne porcje) może rocznie zaoszczędzić kilkaset kilogramów produktu, który dotąd był “dodawany gratis” powyżej nominalnej wagi netto (przy luźnych nastawach maszyny firma dodawała np. średnio 2 gramy więcej orzechów na paczkę, by na pewno nie zejść poniżej deklaracji wagi). Bliźniak zasugerował ustawienie precyzyjniejszych wag i częstsze autokalibracje – co wdrożono, zyskując istotną oszczędność surowca. Dodatkowo, model pozwolił przewidzieć wpływ prędkości linii na szczelność zgrzewów: przy zbyt wysokiej szybkości odrzut wadliwie zamkniętych torebek gwałtownie rósł. Dzięki symulacji znaleziono punkt optymalny – prędkość minimalnie niższą od maksymalnej, przy której zgrzewy pozostają pewne. W efekcie ilość odpadów (uszkodzonych opakowań do wyrzucenia) spadła, a ogólna efektywność linii wzrosła.
Choć powyższe przykłady są hipotetyczne, dobrze obrazują realne możliwości technologii cyfrowych bliźniaków. Firmy różnej wielkości, od zakładów produkujących szkło po fabryki spożywcze, mogą skorzystać na takim wirtualnym “poligonie doświadczalnym”. Niezależnie od branży, schemat jest podobny: budujemy model procesu, karmimy go danymi z rzeczywistej produkcji, a następnie zadajemy pytania i testujemy warianty, które w prawdziwym świecie byłyby trudne lub kosztowne do sprawdzenia.
Warto zaznaczyć, że korzyści nie ograniczają się tylko do wydajności czy kosztów – dotyczą także zrównoważonego rozwoju, o czym poniżej.
Cyfrowy bliźniak a zrównoważony rozwój
Technologie cyfrowe odgrywają coraz większą rolę we wspieraniu zrównoważonego rozwoju przemysłu – i nie inaczej jest z cyfrowymi bliźniakami. W jaki sposób digital twin wpisuje się w strategię zrównoważonego rozwoju? Przede wszystkim poprzez optymalizację wykorzystania zasobów (energii, materiałów, czasu maszyn) oraz ograniczanie marnotrawstwa i negatywnego wpływu na środowisko.
Efektywność energetyczna
Bliźniaki cyfrowe pozwalają monitorować i modelować zużycie energii przez maszyny oraz całe procesy. Dzięki temu firmy mogą identyfikować obszary o największej energochłonności (np. urządzenia grzewcze, sprężarki, silniki) i szukać sposobów ich ulepszenia. Symulacje mogą pokazać wpływ zmian parametrów procesu na pobór mocy – np. obniżenie temperatury procesu o kilka stopni lub wyłączenie urządzeń pomocniczych na czas przestojów. Według analiz Światowego Forum Ekonomicznego, wykorzystanie bliźniaków w fabrykach pozwala na wgląd w rzeczywiste zużycie energii w czasie rzeczywistym i poszukiwać ulepszeń, co przekłada się nie tylko na oszczędności finansowe, ale i bardziej ekologiczną produkcję. W jednym z przykładów fabryka LG Electronics dzięki integracji bliźniaka z danymi produkcyjnymi zdołała zredukować zużycie energii o 30% bez utraty wydajności – to efekt uboczny optymalizacji procesu, która pierwotnie miała na celu głównie poprawę produktywności i jakości (te zresztą też się poprawiły). Pokazuje to, że efektywna produkcja często idzie w parze ze zrównoważoną produkcją: mniej marnowanej energii to zarówno niższe koszty, jak i mniejszy ślad węglowy.
Mniejsze marnotrawstwo materiałów i odpadów
Jak wspomniano wyżej, bliźniak cyfrowy pomaga zmniejszyć odsetek braków i wad produkcyjnych poprzez lepszą kontrolę procesu (symulacje zapewniają warunki do precyzyjnego dostrajania parametrów). To oznacza, że zużywamy mniej surowców na produkcję wyrobu o wymaganej jakości – mniej odpadów produkcyjnych trafia do kosza, mniej materiału idzie na marne. Ponadto symulacje pomagają projektować bardziej efektywne produkty (np. lżejsze, o mniejszym zużyciu materiałów) i procesy ich wytwarzania. W efekcie przemysł może wytwarzać tę samą ilość wyrobów przy mniejszym zużyciu surowców. Bliźniaki mogą również monitorować w czasie rzeczywistym wskaźniki odpadu i wykorzystania materiałów, co daje menedżerom wgląd w to, gdzie są straty – i co można poprawić. Wspomniane WEF podaje, że cyfrowe bliźniaki umożliwiają firmom uzyskać wgląd w zużycie materiałów i energii praktycznie w czasie rzeczywistym, prowadząc do oszczędności ekonomicznych oraz bardziej ekologicznej i zrównoważonej działalności. Przykładowo, jeśli model wykryje, że pewna maszyna generuje dużo odpadu (np. skrawki, ścinki), można spróbować zmienić parametry pracy lub harmonogram konserwacji, aby to ograniczyć – a wcześniej przetestować efekt takiej zmiany na modelu.
Redukcja awarii i wydłużenie życia urządzeń
Zrównoważony rozwój to nie tylko kwestia środowiska, ale i efektywnego gospodarowania majątkiem. Dzięki cyfrowym bliźniakom możliwe jest wdrożenie zaawansowanej predykcyjnej konserwacji (predictive maintenance) – czyli serwisowania maszyn dokładnie wtedy, gdy jest to potrzebne, zanim dojdzie do awarii. Bliźniak analizuje dane o pracy urządzeń (wibracje, temperatura, obciążenie, błędy) i przy użyciu AI przewiduje, kiedy dany komponent może zawieść. Pozwala to zapobiegać poważnym awariom (a więc unikać nagłych przestojów, które dezorganizują produkcję i generują straty) oraz wydłużać cykl życia maszyn – bo sprzęt jest serwisowany optymalnie, nie za późno (co grozi awarią), ale też nie za wcześnie (unikamy zbędnej wymiany części, która mogłaby jeszcze pracować). To ważne z punktu widzenia zrównoważonego rozwoju: maksymalne wykorzystanie trwałości maszyn i części oznacza mniej odpadów elektronicznych i metalowych, rzadszą konieczność produkcji nowych części zamiennych, a więc i mniejsze zużycie zasobów naturalnych. Dodatkowo, mniej awarii to mniej przestojów, a więc bardziej stabilna produkcja – co przekłada się na mniejsze zużycie energii w trybie “rozruch-zatrzymanie” i ogólnie bardziej płynne, wydajne działanie zakładu.
Optymalizacja logistyki i transportu
Choć to nie zawsze część bliźniaka produkcyjnego, coraz częściej firmy rozszerzają koncepcję digital twin na cały łańcuch dostaw. Pozwala to symulować np. transport i dostawy, co ma wpływ na ślad węglowy (optymalne trasy, pełniejsze wykorzystanie ładowności). Przedsiębiorstwo może również, korzystając z bliźniaka, lepiej synchronizować produkcję z dostawami surowców i wysyłką wyrobów – aby unikać ekspresowych transportów (bardziej emisyjnych) i np. zmniejszyć potrzebę dodatkowego magazynowania. Krótko mówiąc, cyfrowe bliźniaki wspierają przejście na bardziej zrównoważony model produkcji: mniej energii, mniej odpadów, mniej emisji przy zachowaniu (a często poprawie) wyników biznesowych.
Warto podkreślić, że te “zielone” korzyści często pojawiają się jako naturalny efekt uboczny optymalizacji procesów. Gdy firma dąży do lepszej efektywności i niższych kosztów poprzez bliźniaka, zwykle równolegle osiąga redukcję zużycia energii czy materiałów. Jednak coraz więcej przedsiębiorstw świadomie wykorzystuje digital twin stricte w celach zrównoważonościowych – np. do monitorowania śladu węglowego produkcji w czasie rzeczywistym i poszukiwania metod jego obniżenia. Granica między “bliźniakiem dla wydajności” a “bliźniakiem dla ekologii” zaciera się: najpełniejsze efekty daje połączenie obu podejść. Eksperci wskazują, że traktowanie osobno bliźniaków produkcyjnych i tych nastawionych na zrównoważony rozwój to stracona szansa – najlepsze rezultaty osiąga się, gdy metyki z obu obszarów są integrowane w jednym modelu. Przykładowo, optymalizując linię pod kątem wydajności, od razu monitorujemy wpływ zmian na zużycie energii i emisje – i szukamy rozwiązania, które równocześnie zwiększy wydajność i zmniejszy emisje (co często jest możliwe dzięki sprytnym innowacjom).
Podsumowując, cyfrowy bliźniak staje się ważnym narzędziem w dążeniu do przemysłu zrównoważonego. Ułatwia on firmom osiągnięcie tzw. podwójnej korzyści (double win): poprawy wyników finansowych przy jednoczesnym zmniejszeniu negatywnego wpływu na środowisko. W czasach, gdy efektywność energetyczna i redukcja emisji są równie ważne co produktywność, technologie cyfrowe takie jak digital twin będą odgrywać kluczową rolę w budowaniu nowoczesnych, odpowiedzialnych fabryk przyszłości.
Jakie dane i systemy są potrzebne, by Digital Twin działał efektywnie?
Aby cyfrowy bliźniak mógł spełniać swoją rolę, potrzebuje ciągłego dopływu wiarygodnych danych z wielu źródeł oraz infrastruktury informatycznej do ich gromadzenia, przetwarzania i symulacji. Innymi słowy – technologia digital twin nie działa w próżni. Poniżej kluczowe elementy (dane i systemy), które stanowią fundament działania cyfrowego bliźniaka w środowisku produkcyjnym:
Czujniki i urządzenia Industrial IoT (IIoT)
To one monitorują parametry maszyn i procesów w czasie rzeczywistym i dostarczają danych do bliźniaka. Mogą to być czujniki temperatury, ciśnienia, wibracji, przepływu, pozycjonowania, kamery wizyjne itp. zainstalowane na krytycznych maszynach. Dzięki IoT bliźniak otrzymuje na bieżąco informacje o tym, co dzieje się na hali produkcyjnej – np. aktualną prędkość linii, wydajność maszyn, zużycie energii przez dane urządzenie. Ważne są również czujniki środowiskowe (np. wilgotność, temperatura otoczenia) oraz czujniki jakości (np. detektory wad). Im więcej relewantnych danych zbieramy, tym dokładniejsze odwzorowanie rzeczywistości osiąga cyfrowy model.
Systemy zbierające dane produkcyjne i energetyczne
W praktyce dane z czujników muszą trafić do centralnych systemów IT. Służą do tego m.in. systemy SCADA i MES do monitorowania produkcji, które zbierają sygnały z PLC i urządzeń w zakładzie. Również liczniki mediów i systemy zarządzania energią dostarczają istotnych danych (np. profil zużycia energii elektrycznej, gazu, sprężonego powietrza). Te wszystkie informacje są gromadzone w bazach danych (często w tzw. historianach procesowych, hurtowniach danych przemysłowych) i udostępniane bliźniakowi. Solidna infrastruktura do akwizycji i przechowywania danych jest więc niezbędna – musi zapewnić spójne i częste próbkowanie danych (w wielu zastosowaniach odczyty co sekundę lub częściej) oraz integrację różnych formatów danych.
Systemy utrzymania ruchu i zarządzania aktywami (CMMS/ERP)
Cyfrowy bliźniak powinien być zasilany danymi o stanie sprzętu i historii awarii, aby skutecznie przewidywać usterki. Dlatego integruje się go z systemem CMMS (Computerized Maintenance Management System) lub modułem utrzymania ruchu w ERP, gdzie rejestrowane są awarie, przestoje, wykonane przeglądy i wymiany części. Dzięki temu model wie np., że dana maszyna ma nowo wymienione łożysko albo ile godzin przepracował silnik od ostatniej naprawy. Te informacje są kluczowe do trenowania algorytmów predykcyjnych i symulowania scenariuszy typu “kiedy nastąpi awaria, jeśli trend wibracji się utrzyma”. Integracja z CMMS bywa wyzwaniem (różne formaty danych), ale jest bardzo wartościowa. W ogóle, pełen cyfrowy bliźniak zakładu często pobiera dane z wielu systemów IT przedsiębiorstwa – nie tylko CMMS, ale i z ERP (dane o zleceniach produkcyjnych, stanach magazynowych), a nawet z systemów jakości (dane o kontrolach jakości, wynikach laboratoryjnych) czy PLM (informacje o konstrukcji produktu). Im pełniejszy obraz danych uda się zintegrować, tym potężniejsze możliwości analityczne bliźniaka.
Platforma integracyjno-analityczna (Big Data, AI/ML)
Posiadanie danych to jedno, ale trzeba je jeszcze przetworzyć na wiedzę. Dlatego w architekturze cyfrowego bliźniaka kluczowe jest środowisko software’owe, które łączy dane z różnych źródeł i analizuje je w czasie rzeczywistym. Może to być dedykowana platforma IoT/IIoT, rozwiązanie chmurowe lub lokalne serwery z odpowiednim oprogramowaniem. Wykorzystuje się narzędzia Big Data do składowania i przetwarzania strumieni danych, a nad tym warstwę analityczną z algorytmami AI/ML do wykrywania wzorców, anomalii i predykcji. Przykładowo, algorytmy uczenia maszynowego analizują dane czujników, by wykryć, że kombinacja drgań i temperatury silnika wskazuje na zużycie łożyska, po czym generują alert o potrzebie wymiany. Sztuczna inteligencja może też pomóc w optymalizacji – np. uczenie ze wzmocnieniem może szukać najlepszego ustawienia parametrów procesu, testując je na modelu cyfrowym. Wszystko to dzieje się na tej platformie analitycznej. Nierzadko wykorzystuje się w tym celu istniejące narzędzia BI (Business Intelligence) rozszerzone o moduły czasu rzeczywistego, biblioteki IoT (np. Apache Kafka do streamingu danych) oraz frameworki AI (TensorFlow, PyTorch) do tworzenia modeli predykcyjnych. Istotne jest, by platforma ta umożliwiała płynną integrację danych historycznych i bieżących – tylko wtedy bliźniak może jednocześnie uczyć się z przeszłości i reagować na teraźniejszość.
Moduły symulacyjne i modele procesów
Sercem cyfrowego bliźniaka są modele symulacyjne odzwierciedlające fizykę procesu czy logikę działania systemu. Mogą to być modele oparte na równaniach inżynierskich (np. model pieca do szkła oparty na termodynamice), modele dyskretne (symulacja kolejek i przepływu zleceń w hali) albo hybrydowe. W przemyśle często korzysta się z oprogramowania do symulacji (jak MATLAB/Simulink, AnyLogic, FlexSim, software CFD/FEA do symulacji zjawisk fizycznych, itp.) zintegrowanego w środowisku bliźniaka. Coraz popularniejsze stają się również modele emulacyjne PLC – tzn. cyfrowe repliki kodu sterowników maszyn – co pozwala testować sekwencje sterowania na bliźniaku przed wgraniem ich na prawdziwe PLC (to jest właśnie wspomniane wirtualne uruchomienie linii produkcyjnej). Modele symulacyjne muszą wiernie odwzorowywać zachowanie maszyny/procesu – są więc często kalibrowane na podstawie danych z rzeczywistości (tzw. model cyfrowy w pętli). Ważne jest także, by synchronizacja między modelem a rzeczywistością była odpowiednio częsta i dokładna – np. model może być uaktualniany danymi co sekundę i musi być na tyle precyzyjny, by drobne różnice nie kumulowały się w błędy predykcji.
Krótko mówiąc, cyfrowy bliźniak to ekosystem wielu technologii. Jak podaje jeden z przeglądów, w skład typowego stacku technologicznego digital twin wchodzą: czujniki IoT, oprogramowanie przemysłowe (w tym ERP/MES/CMMS) integrujące dane, narzędzia analityczne big data, algorytmy AI/ML oraz zaawansowane modele symulacyjne. Przed wdrożeniem bliźniaka firmy muszą zatem zadbać o fundamenty w postaci infrastruktury danych. Często pierwszym krokiem jest cyfryzacja samej produkcji – wyposażenie maszyn w czujniki, połączenie sterowników do sieci, wdrożenie systemów rejestrujących kluczowe informacje. Bez tego nawet najlepszy algorytm nie pomoże. Potwierdza to przykład przytoczony przez Unit8 (case study z branży szklarskiej): podjęto próbę zbudowania modelu optymalizującego wydajność linii, ale zbyt niska jakość i kompletność danych z czujników uniemożliwiła osiągnięcie od razu zakładanych rezultatów – projekt musiał najpierw skupić się na poprawie infrastruktury pomiarowej.
Dodatkową kwestią jest integracja rozmaitych systemów. Dane z produkcji mogą pochodzić z dziesiątek różnych urządzeń i aplikacji – dlatego konieczne jest zastosowanie standardów komunikacyjnych i integracyjnych (OPC UA, MQTT, API baz danych itp.) tak, aby cyfrowy bliźniak mógł swobodnie pobierać informacje ze wszystkich działów. W praktyce często wykorzystuje się platformy IoT przemysłowego lub middleware, które łączą te klocki w całość. Istotna bywa też wydajność infrastruktury IT – symulacje w czasie rzeczywistym i analiza dużej ilości danych wymagają mocy obliczeniowej. Firmy coraz częściej korzystają z chmury obliczeniowej do hostowania części swojego bliźniaka (zwłaszcza komponentów AI i big data), co zapewnia skalowalność mocy, jednak wiąże się z potrzebą bezpiecznej transmisji danych z fabryki do chmury (cyberbezpieczeństwo nie może być pominięte).
Reasumując, bez odpowiednich danych cyfrowy bliźniak jest tylko piękną wizualizacją bez pokrycia w rzeczywistości. Dlatego przedsiębiorstwo pragnące wdrożyć Digital Twin powinno najpierw upewnić się, że ma “cyfrowy krwioobieg” – sieć sensorów, systemów i integracji – który będzie go zasilał. Na szczęście rozwój IoT i systemów monitoringu przemysłowego bardzo to ułatwia. Już dziś dostępne są rozwiązania, które pozwalają zbierać dane ze wszystkich ważnych źródeł i procesów produkcyjnych w czasie rzeczywistym i konsolidować je w jednym miejscu – stanowiąc tym samym bazę do budowy bliźniaka cyfrowego.
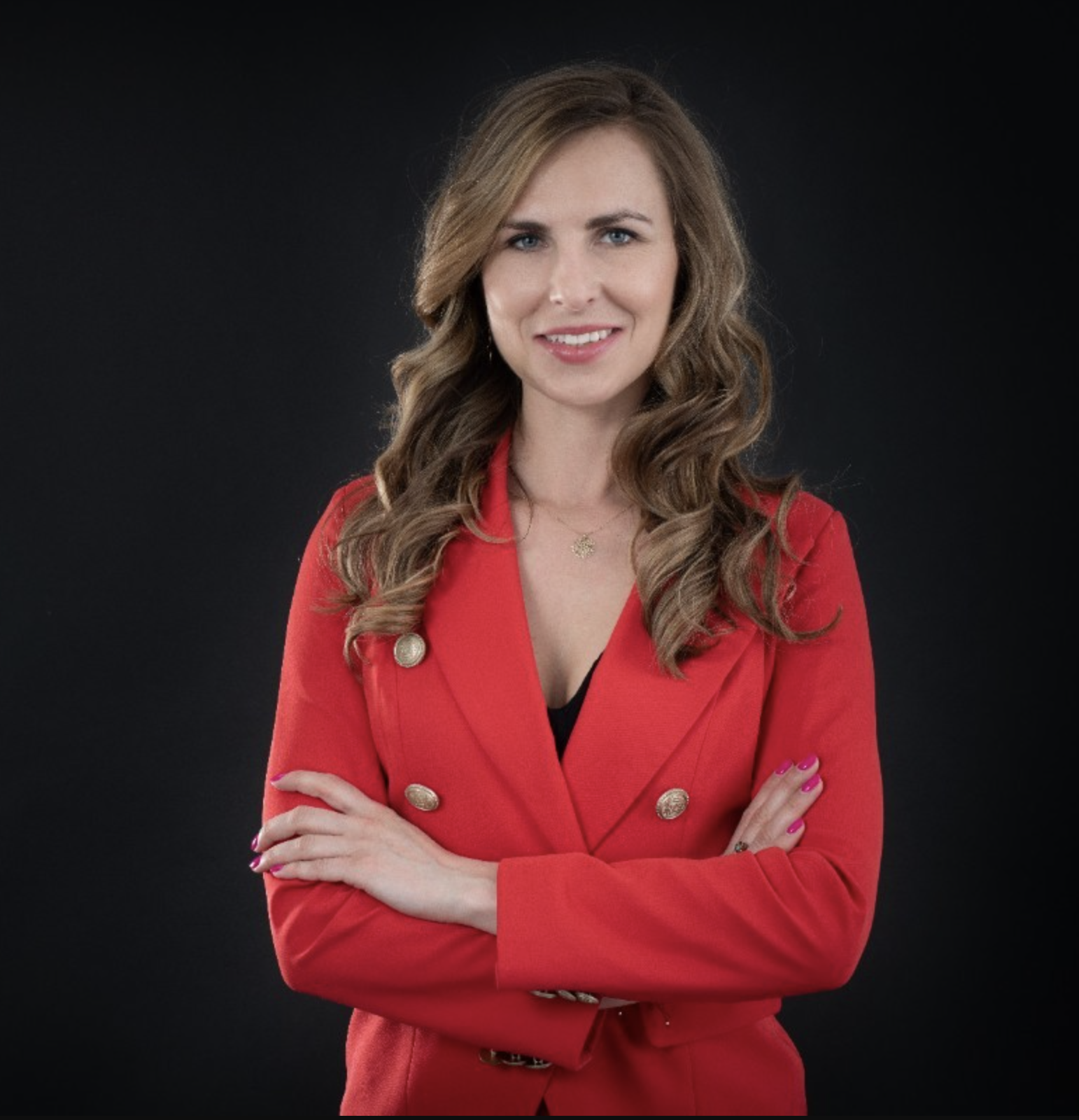
Monika Nowak
Dyrektor projektu iPLAS
Zbieraj dane z całej produkcji w jednym miejscu
iPLAS integruje dane z maszyn, procesów automatycznych i manualnych w czasie rzeczywistym. Bezpiecznie przechowujemy je w chmurze lub na Twoim serwerze, a dzięki zaawansowanemu przetwarzaniu danych zyskasz pełen wgląd w swoją produkcję.
Fundament pod cyfrowego bliźniaka – rozwiązania takie jak iPLAS
Skuteczne wdrożenie cyfrowego bliźniaka wymaga nie tylko wizji, ale też solidnych fundamentów technologicznych – przede wszystkim narzędzi do zbierania i zarządzania danymi. W Iplas od lat rozwijamy rozwiązanie, które dokładnie w tym pomaga – nasz system do monitorowania produkcji i zużycia zasobów w czasie rzeczywistym.
iPLAS umożliwia pozyskiwanie danych z każdego etapu procesu – zarówno z maszyn i automatyki przemysłowej, jak i z operacji wykonywanych manualnie (za pomocą paneli operatorskich, kodów QR, RFID). Konsolidujemy te informacje w jednej centralnej bazie, dając firmom pełen obraz sytuacji – jedno spójne źródło prawdy o tym, co dzieje się na hali produkcyjnej.
Dzięki naszej platformie dużo łatwiej jest zbudować cyfrowego bliźniaka – dane o produkcji, zużyciu energii, przestojach czy awariach są już dostępne, ustrukturyzowane i gotowe do wykorzystania w modelach symulacyjnych. Udostępniamy także wizualizacje i intuicyjne pulpity nawigacyjne, które pozwalają śledzić kluczowe wskaźniki w czasie rzeczywistym – niezależnie od tego, czy korzysta z nich operator, kierownik zmiany, czy dyrektor zakładu.
Nasze rozwiązanie jest modułowe, co oznacza, że można je łatwo rozbudować – o integracje z systemami CMMS, ERP, SCADA czy zaawansowane analizy AI/ML. Dzięki temu iPLAS stanowi nie tylko system do monitoringu, ale fundament pod wdrożenie cyfrowych bliźniaków – zapewniając dopływ danych, który jest niezbędny do ich działania.
Dla wielu naszych klientów właśnie wdrożenie iPLAS było pierwszym krokiem do większej cyfryzacji – pozwalając im zyskać pełną widoczność procesów i zacząć świadomie zarządzać danymi operacyjnymi. Stopniowo dodając kolejne warstwy analityczne i symulacyjne, firmy mogą z czasem dojść do pełnoprawnego cyfrowego bliźniaka swojego zakładu.
Co więcej, wspieramy naszych partnerów na każdym etapie tej transformacji – od podłączenia maszyn, przez integracje z istniejącymi systemami IT, aż po konfigurację modeli danych. Wiemy, jak wiele można zyskać dzięki cyfrowym bliźniakom – nie tylko lepszą efektywność, ale też większą odporność na zakłócenia i bardziej świadome decyzje inwestycyjne.
Podsumowując – cyfrowy bliźniak to dziś jedno z najpotężniejszych narzędzi w rękach menedżerów przemysłowych. Umożliwia testowanie zmian „na sucho”, znajdowanie najlepszych rozwiązań i eliminację błędów jeszcze przed ich pojawieniem się w rzeczywistości. Praktyczne przykłady – od zakładów szklarskich po firmy pakujące żywność – pokazują, że niezależnie od branży, technologia ta może przynieść wymierne korzyści.
W erze rosnących wymagań dotyczących efektywności energetycznej i ograniczania śladu węglowego, cyfrowe bliźniaki stają się również ważnym narzędziem wspierającym zrównoważony rozwój. Dzięki iPLAS – naszej platformie monitoringu produkcji i zużycia zasobów – pomagamy naszym klientom zbudować solidne podstawy pod takie wdrożenia i skutecznie przejść do przemysłu przyszłości.
Źródła:
- https://www.esa-automation.com/en/the-integration-of-digital-twins-and-iiot-in-predictive-maintenance/
- https://www.automationworld.com/design/article/33037045/why-digital-twins-are-becoming-essential-for-testing-and-commissioning
- https://knowhow.distrelec.com/internet-of-things/6-ways-digital-twins-are-revolutionising-manufacturing-in-2024/
- https://www.weforum.org/stories/2024/06/digital-twins-and-industrial-clusters-are-about-to-change-the-face-of-manufacturing/
- https://www2.deloitte.com/us/en/insights/topics/strategy/racing-digital-twin-technology.html
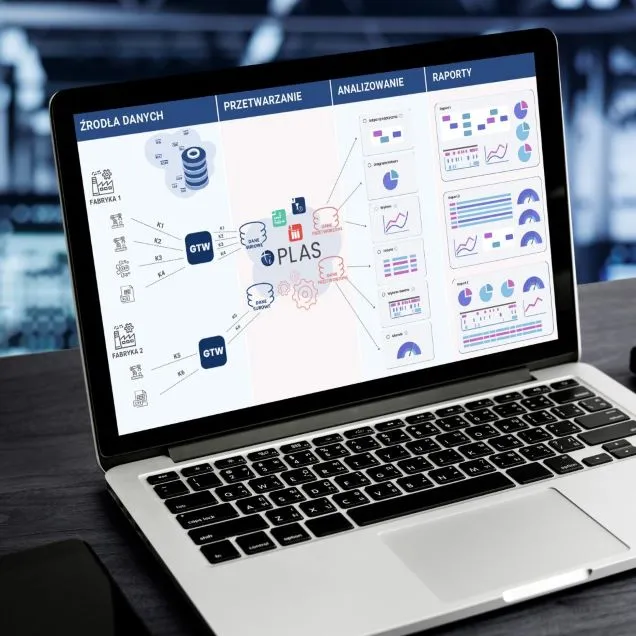
+48 883 366 717