Wstęp
System ERP (Enterprise Resource Planning) integruje kluczowe obszary firmy – finanse, sprzedaż, zaopatrzenie, magazyn czy kadry – w jednym rozwiązaniu biznesowym, zapewniając jednolity przepływ informacji i „jedno źródło prawdy” dla przedsiębiorstwa. Dzięki temu decydenci dysponują pełnym obrazem operacji biznesowych i mogą sprawnie planować zasoby (finansowe, ludzkie, materiałowe).
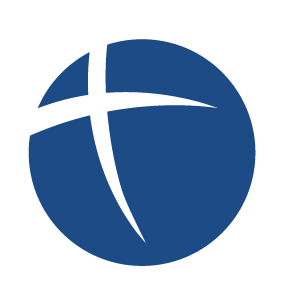
System MES (Manufacturing Execution System) działa natomiast na hali produkcyjnej: zarządza, monitoruje i synchronizuje przebieg procesów produkcyjnych w czasie rzeczywistym. Zbiera dane bezpośrednio z maszyn i stanowisk, śledzi realizację zleceń, identyfikuje przestoje i wspiera kontrolę jakości. Dzięki MES produkcja jest bardziej zautomatyzowana i przejrzysta, a kierownicy mogą szybko reagować na wąskie gardła. Z kolei systemy CMMS (Computerized Maintenance Management System) wspomagają planowanie i realizację utrzymania ruchu – rejestrują przeglądy, awarie, stan części zamiennych oraz organizują pracę służb serwisowych. Każde z tych rozwiązań pełni inną funkcję: ERP steruje procesami biznesowymi i logistycznymi, MES – operacjami produkcyjnymi, a CMMS – utrzymaniem parku maszyn.
Konsekwencje braku integracji
Jeśli systemy ERP, MES i CMMS nie są ze sobą zintegrowane, powstają silosy danych – każde z narzędzi gromadzi informacje na swoim poziomie i „trzyma je tylko dla siebie”. Taka fragmentacja danych uniemożliwia menedżerom uzyskanie spójnego obrazu firmy i może prowadzić do opóźnień w podejmowaniu decyzji. Przykładowo, dział zakupów może nie widzieć aktualnych potrzeb produkcji, a produkcja nie ma informacji o stanach magazynowych z ERP. Brak płynnej wymiany informacji blokuje szybkie reagowanie na problemy – kadra kierownicza nie ma kompleksowych danych, na których mogłaby oprzeć decyzje. W rezultacie pojawiają się błędy planistyczne (np. nadmiarowe zapasy lub niedobory materiałów), nadmierne przestoje oraz ogólne obniżenie efektywności operacyjnej. Dopiero integracja zapewnia swobodny przepływ danych w całym cyklu produkcyjnym, co otwiera drogę do „fabryki przyszłości” opartej na ciągłym doskonaleniu procesów.
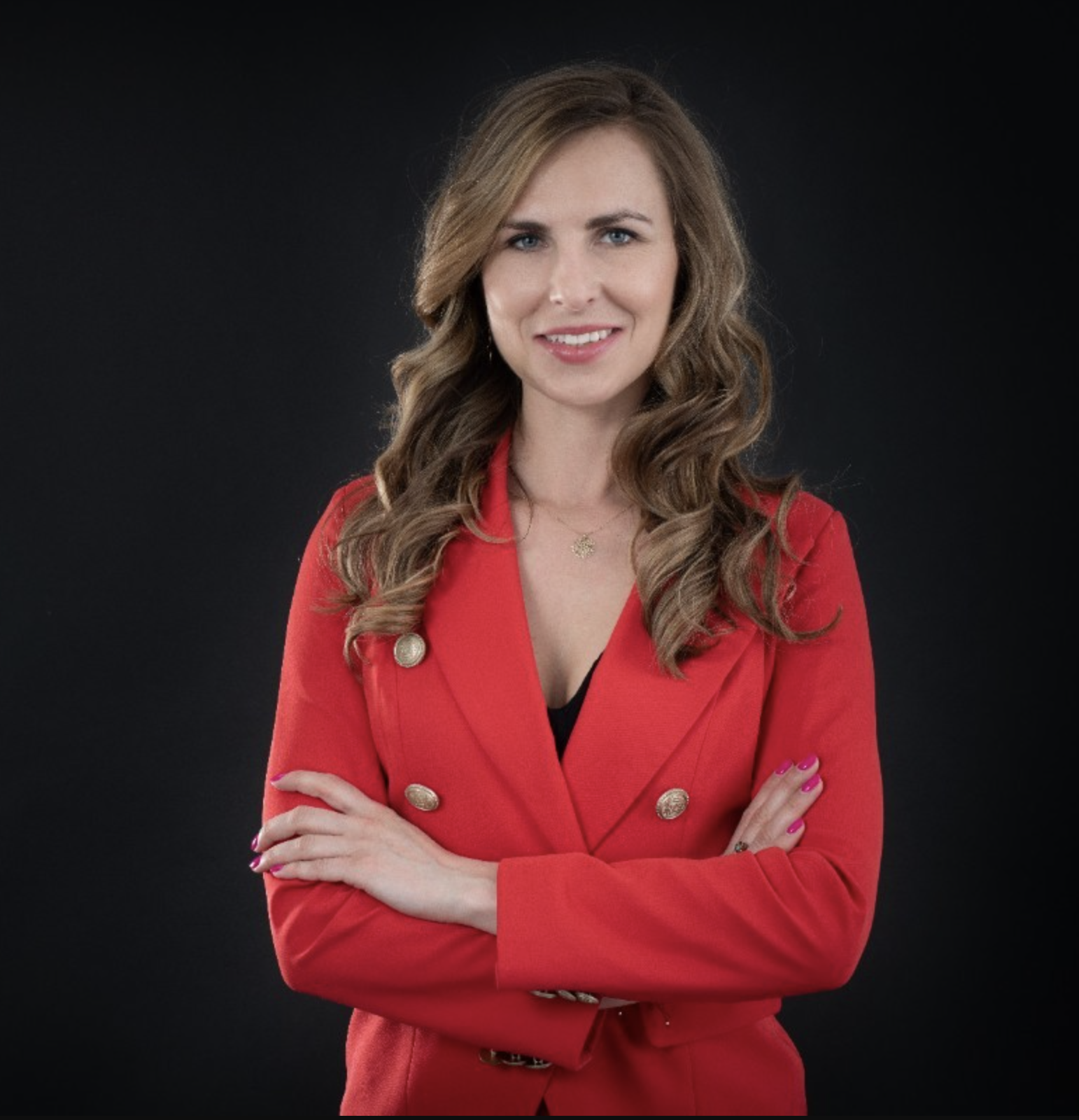
Monika Nowak
Dyrektor projektu iPLAS
Zbieraj dane z całej produkcji w jednym miejscu
iPLAS integruje dane z maszyn, procesów automatycznych i manualnych w czasie rzeczywistym. Bezpiecznie przechowujemy je w chmurze lub na Twoim serwerze, a dzięki zaawansowanemu przetwarzaniu danych zyskasz pełen wgląd w swoją produkcję.
Kluczowe procesy do synchronizacji
Integracja systemów ERP, MES i CMMS synchronizuje wszystkie kluczowe procesy produkcyjne i biznesowe. Przykładowo, pozwala na pełne powiązanie planowania produkcji z wykonaniem zleceń – harmonogram zleceń generowany w ERP automatycznie trafia do MES, który realizuje go w czasie rzeczywistym. Dane o stanach magazynowych i gospodarka materiałowa są wspólne: MES raportuje zużycie surowców, a ERP odświeża zapasy i potrzeby zakupowe. Równocześnie systemy wspierają zarządzanie utrzymaniem ruchu – zlecenia serwisowe z CMMS uwzględniają priorytety produkcyjne, a dostępność maszyn jest widoczna w planie produkcji. Integracja obejmuje też kontrolę jakości i śledzenie partii (traceability) – informacje o defektach z MES czy CMMS trafiają do ERP, co pozwala szybko identyfikować źródła problemów. Wreszcie, wszystkie dane z produkcji (np. czas pracy maszyn, wydajność, wskaźniki OEE) mogą być zbierane i raportowane jako KPI w jednym miejscu. Dzięki temu kierownictwo otrzymuje jednorodne raporty o efektywności całej fabryki i może podejmować decyzje operacyjne oraz strategiczne na podstawie pełnych, aktualnych informacji.
- Zsynchronizowane planowanie: ERP i MES wspólnie harmonogramują produkcję i realizują zadania zgodnie z rzeczywistą wydajnością maszyn.
- Zarządzanie materiałami: Automatyczna wymiana informacji o zapasach i zużyciu materiałów eliminuje nadmiarowe magazynowanie i niedobory.
- Utrzymanie ruchu: Zlecenia serwisowe (przeglądy, naprawy) w CMMS uwzględniają plany produkcji z ERP/MES, co minimalizuje przestoje.
- Kontrola jakości i traceability: Wyniki testów i błędy produkcji zgłaszane w MES są widoczne w ERP, co przyspiesza korekty procesów.
- Raportowanie KPI: Wskaźniki wydajności (OEE, czasy przestojów itp.) z MES są automatycznie przesyłane do ERP/BI, umożliwiając spójne monitorowanie kluczowych parametrów.
Korzyści z pełnej synchronizacji
Synchronizacja danych i procesów między ERP (planowanie zasobów), MES (realizacja produkcji) i CMMS (utrzymanie ruchu) przekłada się bezpośrednio na efektywność operacyjną, jakość decyzji i konkurencyjność rynkową. Poniżej przedstawiamy najważniejsze korzyści, jakie niesie ze sobą pełna integracja tych systemów – zarówno dla zarządu, jak i zespołów operacyjnych.
Korzyść | Opis |
---|---|
Jedno źródło informacji | Zintegrowany system zapewnia spójność danych – unika się podwójnego wpisywania informacji i błędów wynikających z niespójnych danych. Wszyscy pracownicy i działy pracują na tych samych danych, co zwiększa zaufanie do raportów. |
Szybsze decyzje biznesowe | Dostęp do aktualnych, pełnych danych z produkcji i zaplecza biznesowego pozwala menedżerom reagować błyskawicznie na zmiany (np. modyfikować plany produkcji w odpowiedzi na nagłe awarie czy opóźnienia). |
Większa przejrzystość operacyjna | Połączenie systemów ERP–MES–CMMS umożliwia pełny przegląd procesów firmy i szybkie generowanie kompleksowych raportów. Dzięki temu łatwiej identyfikować wąskie gardła, unikać marnotrawstwa oraz optymalnie zarządzać zasobami (maszynami, materiałami i personelem). |
Lepsza efektywność i konkurencyjność | Zintegrowane dane pozwalają wdrażać strategię Lean i ciągłego doskonalenia – skracają czas realizacji zamówień, redukują przestoje i koszty operacyjne. W rezultacie firma szybko osiąga wyższą wydajność przy niższych kosztach. |
Podejście do integracji systemów
- Architektura warstwowa (ISA-95): Przyjęcie podejścia warstwowego ułatwia projektowanie integracji – standard ISA‑95 definiuje poziomy od produkcji (czujniki, maszyny) przez systemy realizacji produkcji (MES/MOM) aż do systemów biznesowych (ERP). Dzięki temu wiadomo, jakie informacje wymieniać między każdą warstwą, co stanowi podstawę do opracowania jednolitych interfejsów ERP–MES.
- Integracja przez API lub platformę pośredniczącą: Dane można wymieniać bezpośrednio za pomocą interfejsów programistycznych (API) obydwu systemów lub przy użyciu pośredniczącego oprogramowania integracyjnego (tzw. szyna ESB). Taka architektura middleware ułatwia elastyczne mapowanie danych i skalowanie integracji między MES, ERP i innymi systemami.
- Gotowe konektory („plug & play”): Wiele popularnych systemów ERP (np. SAP, Microsoft Dynamics, Infor M3) oferuje standardowe konektory do integracji, co znacząco przyspiesza wdrożenie połączenia z MES lub CMMS. Dzięki temu można stosunkowo szybko skonfigurować wymianę danych (np. zleceń produkcyjnych, stanów magazynowych) bez konieczności budowania wszystkiego od podstaw.
Przygotowanie do integracji
- Analiza procesów i danych: Przed wdrożeniem integracji warto zidentyfikować kluczowe procesy produkcyjne do połączenia (np. planowanie zleceń, gospodarka magazynowa, utrzymanie ruchu) oraz określić, jakie dane i w jakim formacie będą wymieniane między MES, ERP i CMMS. Taka analiza ustala zakres projektu i cele biznesowe integracji.
- Zaangażowanie zespołów IT i operacyjnych: W proces integracji powinni być zaangażowani zarówno specjaliści IT, jak i użytkownicy biznesowi z działów produkcji, logistyki czy utrzymania ruchu. Niezbędne jest zapewnienie dostępu do dokumentacji systemów oraz ustalenie ścisłej współpracy obu stron już na etapie planowania. Kluczowe jest też szkolenie personelu – pracownicy muszą wiedzieć, jak korzystać z nowego, zintegrowanego rozwiązania i jakie korzyści z niego płyną.
- Mapowanie i jakość danych: Trzeba ustalić jednolitą strukturę danych – dane powinny być wprowadzane w systemie jednorazowo i automatycznie przesyłane do pozostałych, aby uniknąć duplikacji. Już na etapie przygotowania wskazane jest zapewnienie pełnej automatyzacji przepływów danych oraz weryfikacja jakości informacji. Dzięki temu po uruchomieniu integracji raporty i analizy będą wiarygodne i przydatne do podejmowania dalszych decyzji.
✅ Checklista: Jak przygotować firmę do integracji ERP–MES–CMMS
Krok | Zadanie | Status |
---|---|---|
1 | Zidentyfikuj cele biznesowe integracji – np. skrócenie czasu realizacji zleceń, lepsze raportowanie, redukcja przestojów | ☐ |
2 | Zmapuj kluczowe procesy i dane – jakie informacje powinny przepływać między systemami i w jakim kierunku | ☐ |
3 | Sprawdź, jakie interfejsy posiadają obecne systemy (API, pliki, bazy danych) | ☐ |
4 | Zaangażuj zespoły IT, produkcji, UR i jakości – utwórz interdyscyplinarny zespół projektowy | ☐ |
5 | Określ priorytety i zakres pierwszego etapu (MVP) – np. tylko wymiana zleceń i raportów OEE | ☐ |
6 | Zaplanuj sposób integracji – np. bezpośrednio przez API czy przez platformę middleware | ☐ |
7 | Zadbaj o jakość danych – ujednolicenie jednostek, kodów produktów, słowników | ☐ |
8 | Zdefiniuj wskaźniki sukcesu (KPI) – np. % błędów w danych, czas raportowania, czas reakcji na awarie | ☐ |
9 | Przeprowadź testy na małej skali – np. jedna linia, jedno gniazdo produkcyjne | ☐ |
10 | Zapewnij szkolenie użytkowników końcowych i nadzór wdrożeniowy | ☐ |
Podsumowanie
Pełna integracja ERP, MES i CMMS pozwala wyeliminować bariery informacyjne między produkcją a biznesem, co jest fundamentem efektywnej cyfrowej transformacji. Kluczowe jest tu kompleksowe podejście: zrozumienie ról poszczególnych systemów, synchronizacja wszystkich istotnych procesów (planowania, realizacji zleceń, logistyki, UR, jakości), wybór odpowiedniej architektury i staranne przygotowanie organizacyjne. Tak skoordynowane działanie przekłada się na wzrost przejrzystości operacyjnej, wyższą produktywność oraz lepsze decyzje zarządcze, co w efekcie wzmacnia konkurencyjność przedsiębiorstwa.
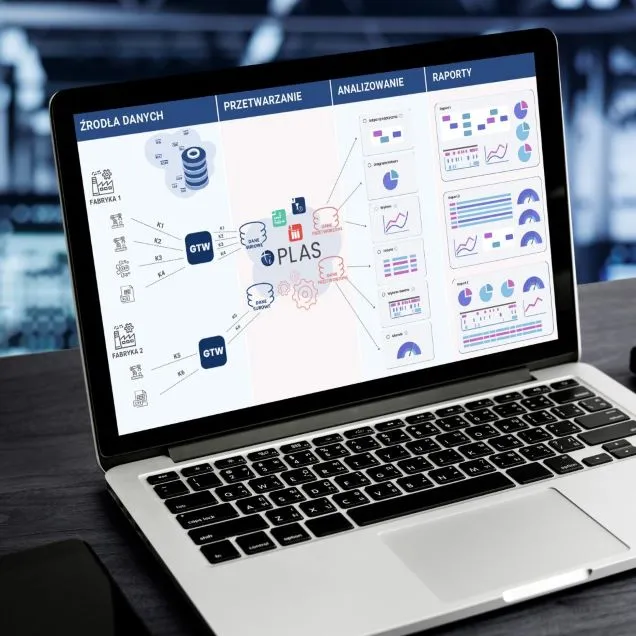
+48 883 366 717