Wstęp
W nowoczesnym przemyśle cyfrowa kontrola jakości jest kluczem do optymalizacji produkcji i redukcji defektów. Systemy MES (Manufacturing Execution System) i QMS (Quality Management System) pełnią w tym procesie różne, ale uzupełniające się role. Ich integracja tworzy „zamkniętą pętlę” planowania, wykonania i analizy, co pozwala eliminować wąskie gardła jakościowe, unikać błędów ludzkich i szybciej reagować na odchylenia. Jak pokazują doświadczenia praktyków, połączenie MES z QMS pomaga poprawić śledzenie produkcji, automatyzować raportowanie niezgodności i wspiera ciągłe doskonalenie procesów. Dzięki temu możliwe jest istotne ograniczenie liczby wadliwych wyrobów oraz zwiększenie powtarzalności i stabilności produkcji.
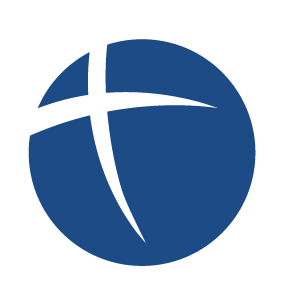
Czym są MES i QMS?
MES (Manufacturing Execution System) to zaawansowane narzędzie do zarządzania i nadzoru produkcji w czasie rzeczywistym. Pozyskuje dane bezpośrednio z hali produkcyjnej – zarówno z maszyn (przez czujniki i automatyzację), jak i od operatorów – i przekazuje je do systemów biznesowych (np. ERP) oraz do pozostałych systemów produkcyjnych. Dzięki MES można śledzić postęp zleceń, monitorować efektywność maszyn, rejestrować zużycie materiałów i automatycznie raportować zdarzenia czy przestoje. System ten zapewnia menedżerom pełną widoczność produkcji i umożliwia podejmowanie szybkich decyzji na podstawie aktualnych danych.
QMS (Quality Management System) to natomiast zbiór procedur, polityk i procesów potrzebnych do planowania i realizacji jakości w firmie. Zgodnie ze standardem ISO 9001 QMS obejmuje wszystko, co wpływa na spełnianie wymagań klienta – od polityki jakości, przez zarządzanie dokumentacją, audyty, po procedury postępowania z reklamacjami. Innymi słowy, QMS definiuje, jak ma przebiegać proces produkcji i kontroli jakości: określa normy, plany kontrolne, wytyczne oraz zasady postępowania w przypadku wykrycia defektów. Jednakże sam system QMS bezpośrednio nie egzekwuje tych procedur w zakładzie – to rola MES-u, aby zapewnić ich realizację na hali produkcyjnej.
Granice odpowiedzialności między MES i QMS
MES i QMS nie konkurują ze sobą, lecz wzajemnie się uzupełniają. QMS stanowi „wyznacznik” jakości: definiuje ogólnofirmowe normy, cele, procedury i wymagania jakościowe. To w QMS powstają plany kontroli, instrukcje pracy, dokumentacja audytów oraz procesy CAPA (Korekty i Działania Zapobiegawcze). MES natomiast operacjonalizuje te założenia – zamienia zapisy z QMS na konkretne akcje i instrukcje na linii produkcyjnej. MES dostarcza operatorom cyfrowe instrukcje krok po kroku, automatycznie weryfikuje wykonanie poszczególnych zadań i od razu rejestruje wyniki realizacji. Dzięki temu MES „pilnuje” na bieżąco, aby każdy krok procesu był zgodny z planem jakościowym, dokumentując przebieg produkcji oraz wszystkie odchylenia.
Korzyści wynikające z integracji: Połączenie MES i QMS tworzy zamknięty cykl planowania, wykonania i doskonalenia. Z jednej strony QMS definiuje standardy, z drugiej MES egzekwuje ich przestrzeganie na hali i gromadzi dane zwrotne. Taka integracja zapewnia pełną widoczność i kontrolę: od definicji procesu, przez dane z jego realizacji, aż po analizę wyników i wprowadzenie poprawek. Integrując systemy, unikamy duplikacji danych i „silosów” informacyjnych – co znacznie poprawia komunikację między działami jakości i produkcji.
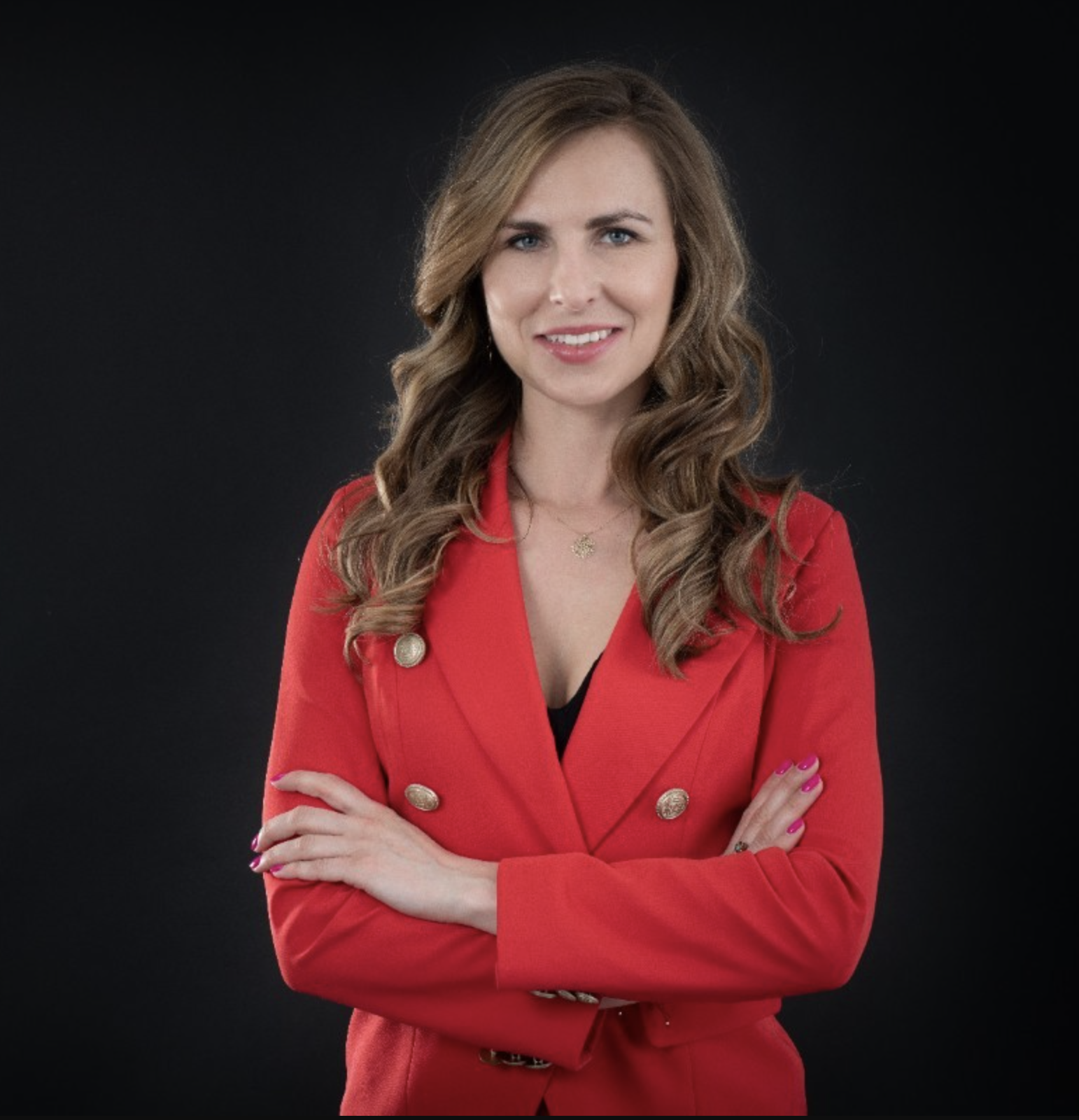
Monika Nowak
Dyrektor projektu iPLAS
Zbieraj dane z całej produkcji w jednym miejscu
iPLAS integruje dane z maszyn, procesów automatycznych i manualnych w czasie rzeczywistym. Bezpiecznie przechowujemy je w chmurze lub na Twoim serwerze, a dzięki zaawansowanemu przetwarzaniu danych zyskasz pełen wgląd w swoją produkcję.
Jakie dane wymieniają się między MES i QMS?
Integracja MES–QMS pozwala na automatyczny przepływ wielu danych, które dotąd bywały rozłącznie gromadzone. Przykładowo:
- Z MES do QMS: system przesyła wszystkie dane produkcyjne i kontrolne z biegu linii. Należą do nich ścieżki traceability (numer partii, identyfikator zlecenia, operator, maszyna, godziny realizacji) oraz zmierzone parametry procesu (np. wymiary i wagi z kontroli SPC). MES także rejestruje każdy wypadek przekroczenia normy i może automatycznie zgłosić zdarzenia jakościowe – np. wygenerować raport niezgodności (NCR) czy uruchomić procedurę CAPA w QMS, gdy wykryje odchylenie. Dane te trafiają do QMS, wzbogacając jego repozytorium o informacje potwierdzające rzeczywisty przebieg produkcji i pomagając w analizie przyczyn problemów.
- Z QMS do MES: system jakości z kolei przekazuje MES plany kontroli i normy, które powinny być respektowane na hali. Mogą to być elektroniczne instrukcje kontrolne, limity tolerancji, listy kontrolne dla operatorów czy harmonogramy audytów. Dzięki temu MES wie, jakie kryteria jakościowe sprawdzać przy realizacji każdego zlecenia i może natychmiast weryfikować, czy produkt spełnia założenia. W niektórych rozwiązaniach QMS występuje nawet w postaci modułu MES (jeden producent oferuje QMS jako rozszerzenie MES), co zapewnia pełną spójność danych i interfejs użytkownika.
Dane te można też zobrazować przykładowo: gdy operator przenosi partię do kolejnego etapu produkcji, MES automatycznie zbiera parametry z urządzeń, uzupełnia je w wykresach SPC i przesyła wyniki do QMS. W razie wykrycia odchylenia system wstrzymuje partię i sygnalizuje konieczność działania korygującego. Dzięki temu mamy pełną historię procesu (tzw. eDHR – elektroniczną kartę historii urządzenia/wyrobu), a zespół jakości otrzymuje szczegółowy kontekst do analizy i raportowania.
Redukcja błędów operatorskich i odchyleń dzięki integracji
Zintegrowane MES–QMS znacząco ogranicza błędy ludzkie i odchylenia od normy. Oto jak to działa w praktyce:
- Automatyczne instrukcje i walidacje: MES dostarcza operatorom szczegółowe, cyfrowe instrukcje wykonania (work instructions) z wbudowanymi kontrolami. Operator wprowadza wyniki pomiarów i inne dane przez terminale, które od razu są sprawdzane przez system. Jeśli wpisana wartość wykracza poza dozwolone granice, MES może natychmiast zasygnalizować błąd, przerwać proces i wygenerować alarm jakości. W rezultacie typowe błędy ręcznego wypełniania dokumentacji czy pomiaru przez człowieka (omission of steps, literówki, błędy w zapisie) są niemal wyeliminowane. Jak podkreślają specjaliści, “błędy ludzkie są unikane dzięki automatycznemu wsparciu operatora i walidacji wprowadzanych wartości”.
- Reakcja na odchylenia w czasie rzeczywistym: Dzięki stałemu monitorowaniu parametrów MES natychmiast wykrywa przekroczenia norm (np. różnice w wymiarach czy wadliwe serie). System może automatycznie wstrzymać partię produkcyjną i powiadomić zespół jakości. Równocześnie uruchamiany jest proces CAPA (korekty i działania zapobiegawcze), oparty na danych traceability. Taka automatyczna obsługa problemu na linii ogranicza koszty związane z późniejszymi reklamacjami i minimalizuje propagację defektu.
- Elektroniczne rejestry zamiast papieru: W zintegrowanym środowisku wszystkie zapisy jakościowe są gromadzone elektronicznie. Operatorzy wypełniają formularze jakościowe online (np. rejestracja niezgodności, wyniki kontroli końcowej), a MES automatycznie uzupełnia je o dane pobrane z maszyn (np. wskazania wag czy czujników). Oznacza to, że tradycyjne błędy w przepisywaniu wyników czy drukowaniu dokumentów zostają zminimalizowane – kluczowe informacje pobierane są „z automatu”, a pracownik musi tylko potwierdzić lub uzupełnić specyficzne szczegóły.
Dzięki takim mechanizmom integracja MES–QMS realnie zmniejsza liczbę wadliwych wyrobów. Mniej niezgodności to wymierne oszczędności – mniej odpadów materiału, mniejsza liczba reklamacji i niższe koszty gwarancji czy poprawek. Jednocześnie proces staje się bardziej powtarzalny i przewidywalny, co poprawia wskaźniki efektywności (np. wskaźnik pierwszego przejścia bez poprawek) i pozwala szybciej wprowadzać usprawnienia.
Zmiany organizacyjne wspierające integrację
By integracja MES i QMS przyniosła oczekiwane efekty, konieczne są także zmiany po stronie organizacyjnej:
- Unikanie silosów i współpraca: Należy zapewnić, aby działy produkcji, utrzymania ruchu i jakości nie pracowały w izolacji. Jak radzą eksperci, „zapobiegaj silosom danych – integruj systemy (MES, QMS, ERP) i dbaj, by działy dzieliły się informacjami”. W praktyce oznacza to utworzenie międzydziałowych zespołów lub komórek zarządzania jakością i produkcją, które wspólnie analizują bieżące KPI i podejmują decyzje. Mogą to być regularne przeglądy jakościowo-produkcyjne, gdzie wykorzystuje się wspólne dane z obydwu systemów.
- Wspólne pulpity menedżerskie i KPI: Dobrą praktyką jest stworzenie dashboardów, które łączą kluczowe wskaźniki z obu obszarów. Dzięki temu kierownicy jakości i produkcji mogą na jednym ekranie śledzić np. wskaźnik wydajności OEE, wskaźniki First-Pass Yield oraz liczbę odrzuconych zleceń. Wyzwanie jakościowe można wyłapać „gołym okiem” na interaktywnych wykresach – jak pokazuje przykład z branży motoryzacyjnej, codzienne monitorowanie dynamicznych dashboardów KPI pozwoliło szybciej wychwytywać odchylenia i skrócić czas wprowadzania nowych produktów.
- Nowe role i kompetencje: Wdrożenie zintegrowanego systemu często wymaga powołania nowych ról lub funkcji. Mogą to być np. analityk ds. danych produkcyjnych lub koordynator integracji IT (osoba odpowiedzialna za utrzymanie połączeń między systemami). Kluczowe jest też szkolenie pracowników – zgodnie z zaleceniami, warto „angażować ludzi – wytłumacz, dlaczego zmiana jest korzystna, i zapewnij im szkolenia oraz wsparcie”. Dzięki temu operatorzy i inżynierowie jakości lepiej zrozumieją wartość automatycznych narzędzi i bardziej je polubią, co przekłada się na mniej oporów przy adaptacji nowych procedur.
- Analiza przyczyn źródłowych (RCA): Po integracji dane z MES i QMS można wykorzystać do pogłębionej analizy problemów. Zamiast zgadywać, co poszło nie tak, zespół może użyć narzędzi takich jak diagramy przyczynowo-skutkowe (5 Why, Ishikawa) bazując na połączonych danych. Na przykład w procesie RCA łatwiej ustalić, że przekroczenie tolerancji wynikało z błędnych ustawień parametrów na maszynie, co zarejestrował MES, albo z wykorzystania niecertyfikowanego materiału zgłoszonego w QMS.
Jak rozpocząć integrację MES i QMS?
Realizacja pełnej integracji powinna odbywać się w sposób przemyślany i stopniowy. Oto kilka praktycznych wskazówek na start:
- Zdefiniuj cele i priorytety: Ustal, które braki jakościowe są obecnie najkosztowniejsze i wpływają na jakość wyrobów. Cel może być np. redukcja odchyłek konkretnych parametrów lub skrócenie czasu reakcji na awarie. Wyraźny cel pozwoli skupić się na najbardziej wartościowych elementach integracji.
- Działaj iteracyjnie: Zamiast wdrażać od razu pełną integrację, warto rozpocząć od pilota na wybranej linii lub procesie. Na początek można np. połączyć MES ze systemem QMS dla jednej partii kontrolnej, śledzić działania i mierzyć efekty. Takie małe kroki „testuj na mniejszej skali, mierz efekty i dopiero potem się rozwijaj” pozwalają uniknąć problemów wdrożeniowych.
- Scenariusze danych: Na początek dobrze sprawdzają się proste scenariusze integracyjne, np. synchronizacja numerów zleceń i wyników finalnej kontroli. MES może automatycznie przekazywać QMS status wybranych partii, a QMS z kolei zwraca do MES informacje o wynikach audytów czy uwagach jakościowych. Inną strategią jest wymiana danych z zakresu traceability: np. każdy wyprodukowany komponent w MES od razu trafia do historii w QMS.
- Narzędzia integracyjne: Wybór technologii komunikacji to klucz. Możliwości jest wiele – od prostych plików wymienianych między systemami, przez gotowe REST API, po zaawansowane szyny integracyjne (ESB). Jeśli oba systemy udostępniają interfejsy API, warto je wykorzystać do dwustronnej wymiany danych. Wielu dostawców MES/QMS oferuje dziś standardowe konektory lub możliwości integracji w chmurze. Chmura (SaaS) również ułatwia połączenie systemów z racji dostępności API. Niezależnie od narzędzi, ważne jest, by na etapie projektowania uwzględnić kwestie bezpieczeństwa (np. autoryzacja dostępu) oraz przyszłej skalowalności.
- Współpraca z dostawcami: Już na etapie wyboru systemów warto ustalić sposób ich integracji. Jednym z najprostszych rozwiązań technicznie jest wdrożenie QMS jako modułu w ramach MES (jedna aplikacja) – eliminuje to problemy z komunikacją. Jeśli decydujemy się na oddzielne systemy, kluczowe jest zaprojektowanie kanałów wymiany: np. MES publikuje w czasie rzeczywistym dane produkcyjne, a QMS je pobiera (lub odwrotnie). Często przydaje się baza wspólnych master data (np. lista produktów, maszyn), aby uniknąć duplikacji i niezgodności.
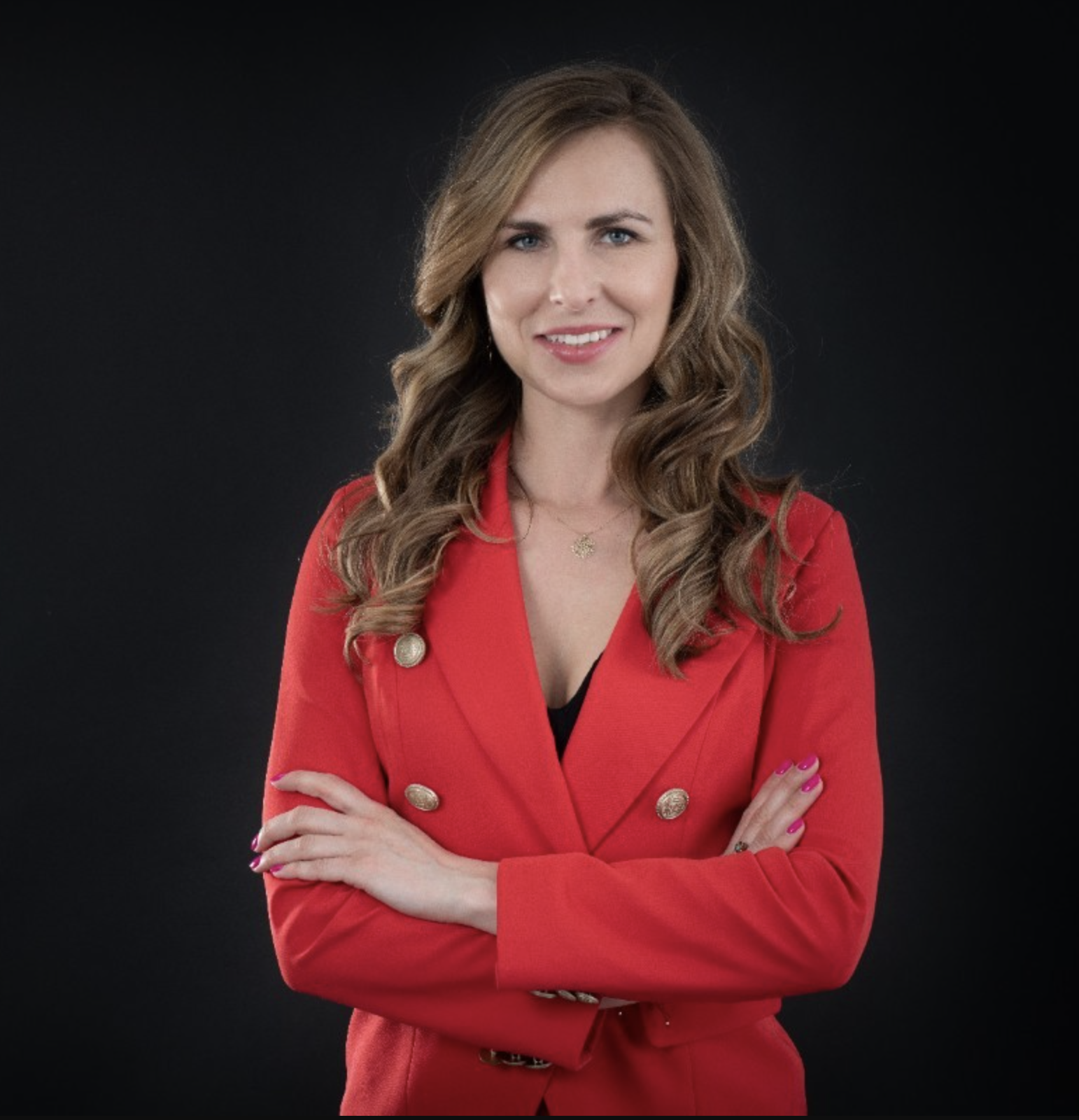
Monika Nowak
Dyrektor projektu iPLAS
Zbieraj dane z całej produkcji w jednym miejscu
iPLAS integruje dane z maszyn, procesów automatycznych i manualnych w czasie rzeczywistym. Bezpiecznie przechowujemy je w chmurze lub na Twoim serwerze, a dzięki zaawansowanemu przetwarzaniu danych zyskasz pełen wgląd w swoją produkcję.
Podsumowanie
Integracja MES i QMS to strategiczny kierunek cyfryzacji produkcji, który bezpośrednio przekłada się na wyższą jakość wyrobów. Pozwala uzyskać wgląd „od zamówienia do dostarczenia”, łącząc zamierzenia jakościowe z ich realizacją. Dzięki wspólnemu zbiorowi danych możliwe jest szybkie identyfikowanie błędów, podejmowanie działań naprawczych jeszcze na linii oraz skuteczne zapobieganie ich powstawaniu. W praktyce oznacza to mniej braków produkcyjnych, rzadsze reklamacje i niższe koszty napraw gwarancyjnych. Przykładowo, firmy wykorzystujące pełną automatyzację kontroli jakości potrafią zmniejszyć odsetek wad nawet o 25–30%, co przekłada się na znaczne oszczędności materiałowe i logistyczne.
Wdrożenie tej integracji wymaga zaangażowania zarówno działu IT, jak i specjalistów od jakości i produkcji. Kluczem jest podejście iteracyjne: zaczynamy od małych kroków, definiując konkretne przypadki użycia i mierząc efekty. Z czasem buduje się złożoną sieć wymiany informacji – od sygnałów z maszyn, przez parametry SPC, po raporty z audytów. Dzięki temu system staje się elastyczny i otwarty na kolejne usprawnienia. Ostatecznie łącząc MES z QMS, uzyskujemy spójny mechanizm, który nie tylko wykrywa i zgłasza problemy jakościowe, ale przede wszystkim pozwala je skutecznie wyeliminować i stale podnosić powtarzalność procesów produkcyjnych.
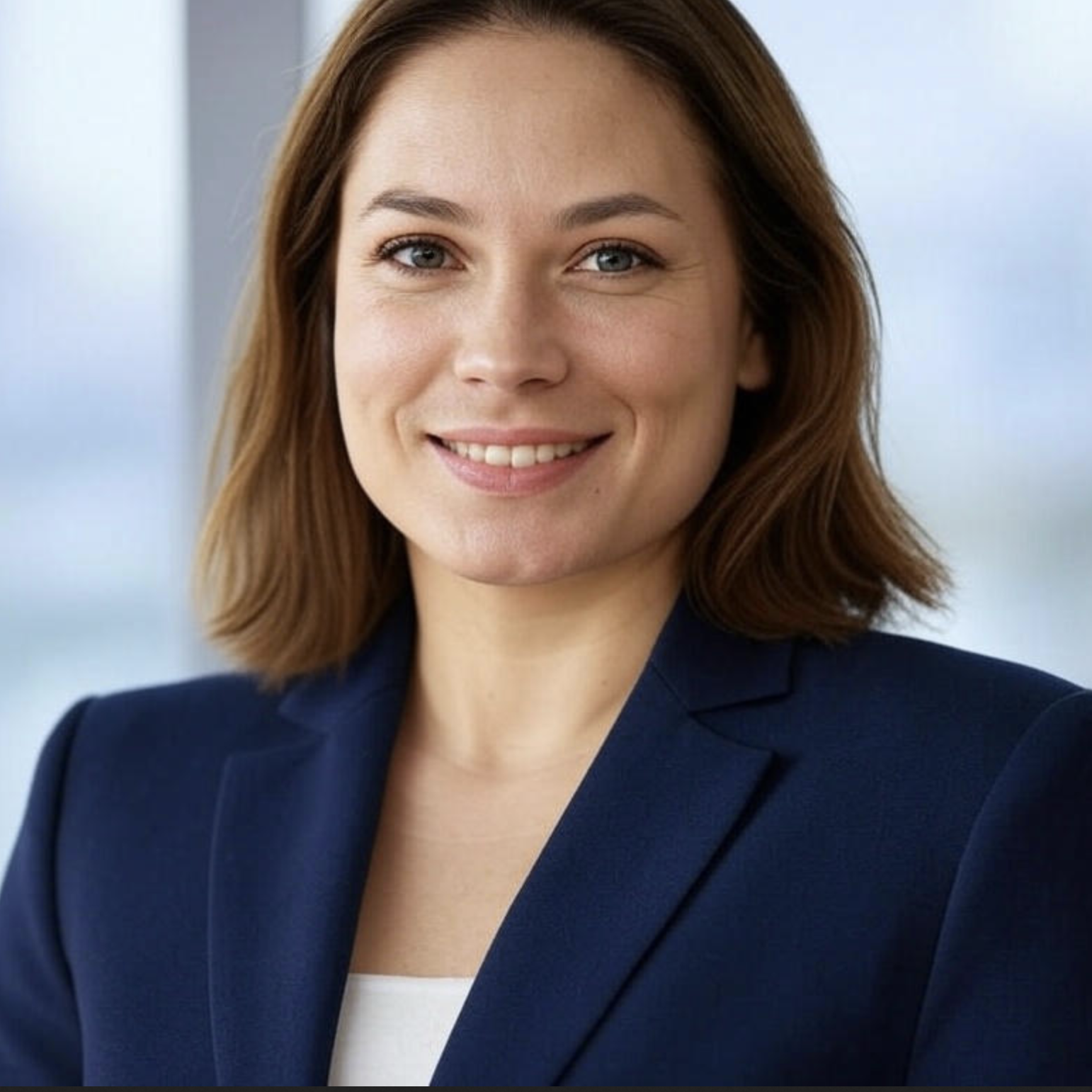
Anna Polczyńska – specjalistka od rozwiązań MES szytych na miarę. Ekspertka z zamiłowaniem do pracy z danymi, która z precyzją analizuje i projektuje. Po godzinach zamienia klawiaturę na rower, realizując swoją pasję jako zapalona kolarka.
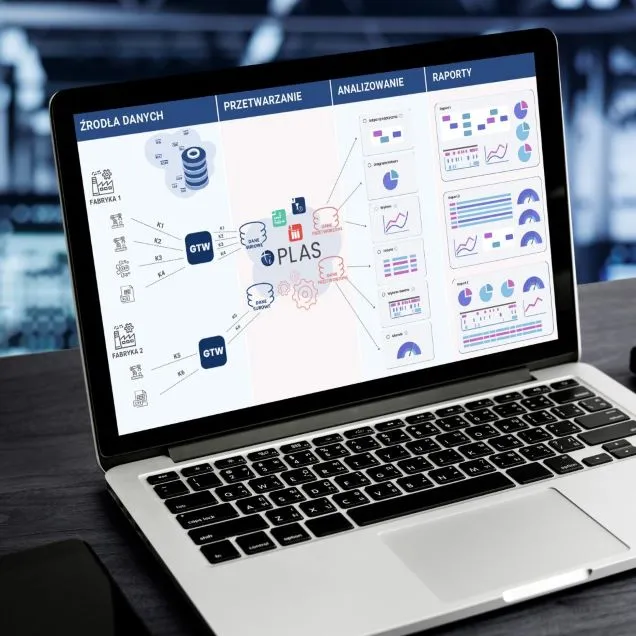
+48 883 366 717