Wstęp
Bazując na doświadczeniach jakie zdobyliśmy tworząc różnego rodzaju systemy monitorującej zużycie mediów technologicznych, w naszym środowisku testowym zasymulowaliśmy istnienie 2 niezależnych zakładów (lub jednostek) produkcyjnych by przedstawić jak w nieświadomy sposób firmy produkcyjne tracą całkiem spore środki finansowe przez brak optymalizacji zużycia energii i zasobów.
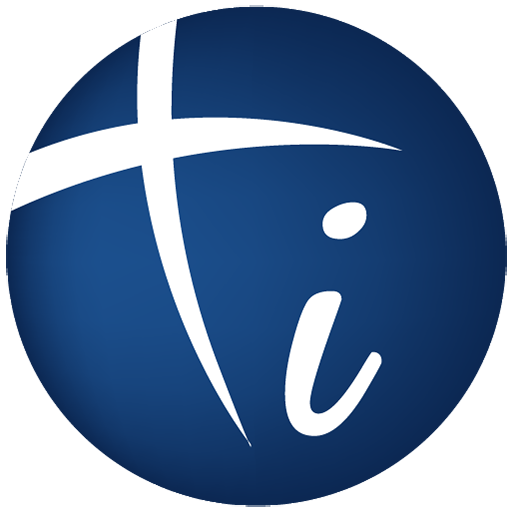
Zarys historyczny
Zakład A
Zakład A powstał 10 lat temu. Firma stopniowo rozwijała się, a ponieważ do zasilania ciągu technologicznego niezbędne było sprężone powietrze. Instalacja oraz sprężarkownia były stopniowo powiększane aż do osiągnięcia docelowego rozmiaru – 3 sprężarek śrubowych o mocy 40kW i wydajności około 7,5 m3/h każda. Sprężarki zostały wyposażone w nadrzędny układ sterowania kontrolujący ich pracę – automatyczne załączanie w zależności od zapotrzebowania kolejnych sprężarek. System wyrównuje również przebiegi wszystkich urządzeń dbając o to by nie było zbyt dużych rozbieżności w motogodzinach. Urządzenia funkcjonują bezawaryjnie i cały układ od lat pracuje praktycznie bezproblemowo. Regularne przeglądy, wymiany materiałów eksploatacyjnych przynoszą pożądane rezultaty.
Zakład B
Następuje gwałtowny rozwój firmy i powstaje konieczność zwiększenia mocy produkcyjnych. Mając już sprawdzony layout technologiczny podjęta zostaje decyzja – kopiujemy całość, skoro wszystko pracuje wydajnie i efektywnie. Po 2 latach od rozpoczęcia procesu inwestycyjnego powstaje zakład produkcyjny B wyposażony w kopię systemu sprężonego powietrza z zakładu A. W związku ze skalą inwestycji w system sprężonego powietrza dostawca proponuje montaż przepływomierza, gdyby w przyszłości zaistniała potrzeba pomiaru wydajności całego systemu sprężonego powietrza.
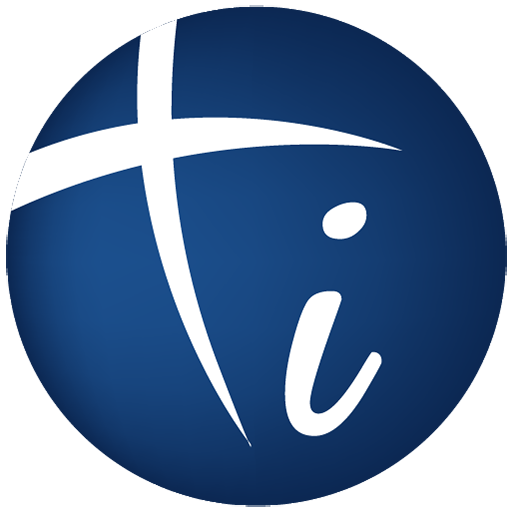
Sytuacja obecna
Zakład B zaczyna pracować w docelowym trybie i wkrótce wyniki produkcyjne przewyższają nawet wyniki zakładu A – wiadomo, nowsze i bardziej wydajne urządzenia umożliwiają wyprodukowanie większej ilości produktów, przy tym samym nakładzie czasu i pracy. W międzyczasie gwałtownie zaczynają rosnąć koszty energii elektrycznej, więc wtedy Plant Manager przypomina sobie o “darmowym” przepływomierzu. Czas go wykorzystać – w ten sposób do gry wkracza IPLAS. Po sprawdzeniu możliwości komunikacyjnych przepływomierz za pośrednictwem protokołu MODBUS zaczyna przesyłać dane do systemu IPLAS.
Przy wsparciu architektów IPLAS powstają pierwsze raporty monitorujące temperaturę sprężonego powietrza wychodzącego ze sprężarek, wielkość przepływu w m3/min oraz ilość dziennego zużycia m3 powietrza.
Analiza wydajności instalacji w zakładzie produkcyjnym
Pierwsze analizy budzą zaskoczenie. Układ ma wydajność całkowitą około 23m3/min a maksymalne przepływy chwilowe nie przekraczają 10m3/min.
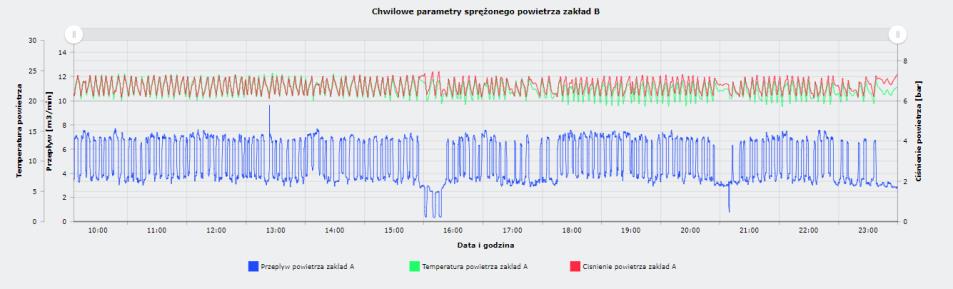
Jeszcze bardziej interesujące są te dane po uśrednieniu:
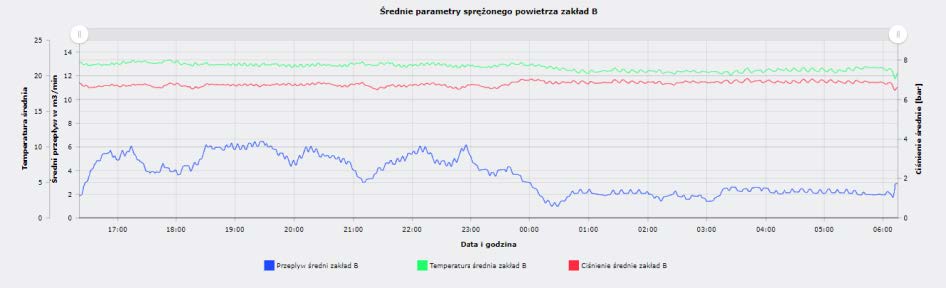
Plant Manager zaczyna się zastanawiać i zadawać pytanie:
Dlaczego sprężarkownia ma wydajność 23m3/min i moc zainstalowaną na poziomie 120 kW skoro rzeczywiste zapotrzebowanie na powietrze jest znacznie mniejsze. Gdzie jest błąd? Jak to wyjaśnić? Przeinwestowaliśmy?
Jak można sprawdzić czy nowa instalacja jest wydajna i oszczędna? To proste. System IPLAS rejestruje dane w trybie ciągłym więc, zobaczymy jak wyglądają oba przebiegi czasowe w trakcie weekendów i dni wolnych. Ponieważ urządzenia produkcyjne muszą być ciągle zasilane w sprężone powietrze, to sprężarki pracują w trybie ciągłym.
Niedziela – w ciągu dnia zakład B nie pracuje, ale tydzień rozpoczyna się od nocnej zmiany więc około godziny 21-22 zaczyna wzrastać zużycie powietrza by osiągnąć max średni pobór w środku zmiany (około 6 m3/min):
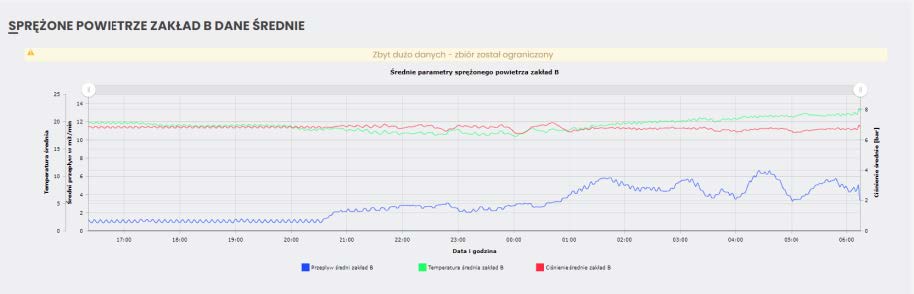
W dniu wolnym od pracy ze sprężarek wypływa średnio 0,6m3/min – to bardzo dobry wynik i naprawdę niewielkie straty w instalacji sprężonego powietrza.
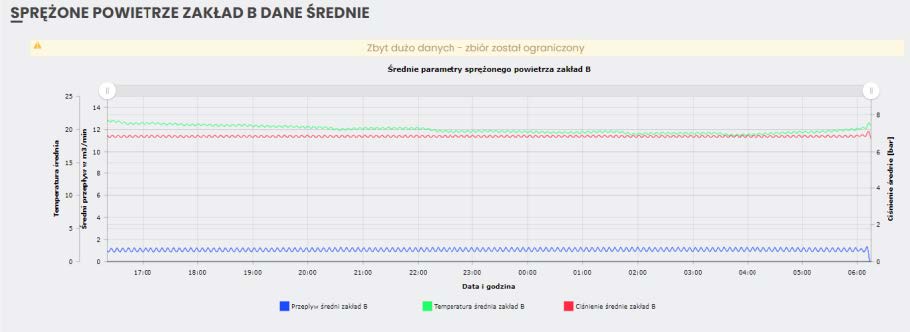
Plant Manager dzieli się swoim spostrzeżeniami z odpowiednikiem z zakładu A i wspólnie podejmują decyzję - montujemy przepływomierz również w zakładzie A. Po 2 miesiącach są już zebrane pierwsze dane i można zacząć porównywać.
Normalny dzień produkcyjny:
Wartości chwilowe przepływu dochodzą do 15m3/min a wartości uśrednione są na poziomie 10m3/min – wykresy poniżej.
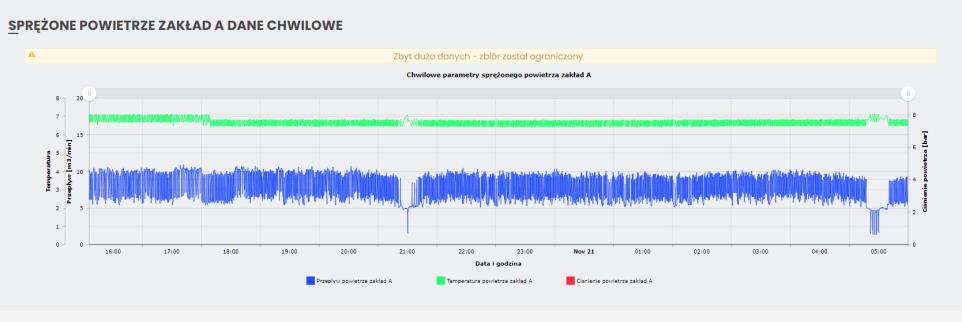
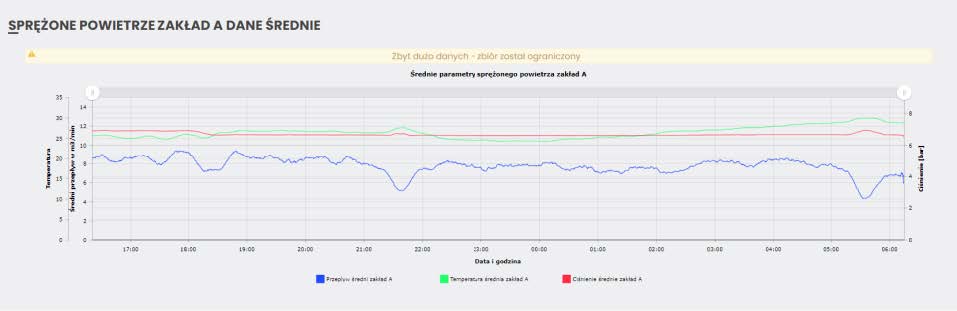
Ze względu na inną specyfikę porównując zakład A korzystamy z danych zmierzonych w sobota – praca na 1wszej zmianie do godziny 14.00:
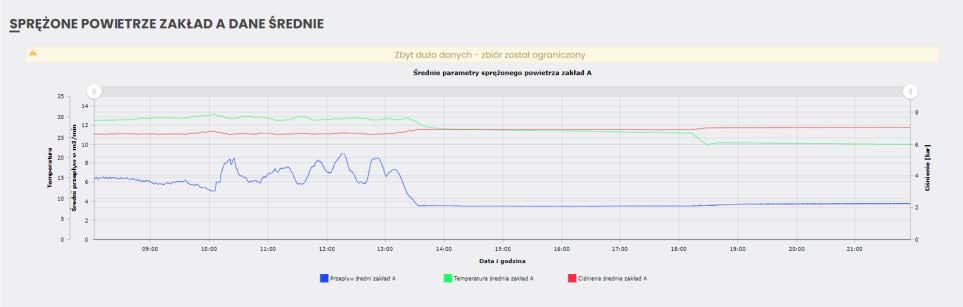
Pusty zakład A ma zużycie sprężonego powietrza na poziomie 4 m3/min. To kolosalna różnica w porównaniu do zakładu B.
Sumując zużycie w IPLAS managerowie zobaczyli różnicę:
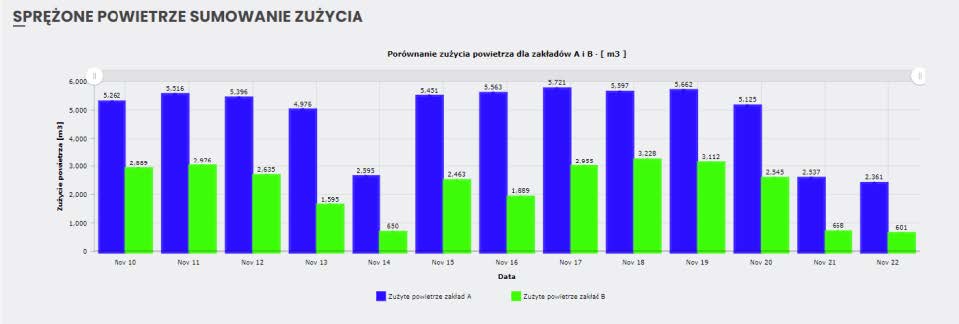
Dodatkowo porównanie kosztów:
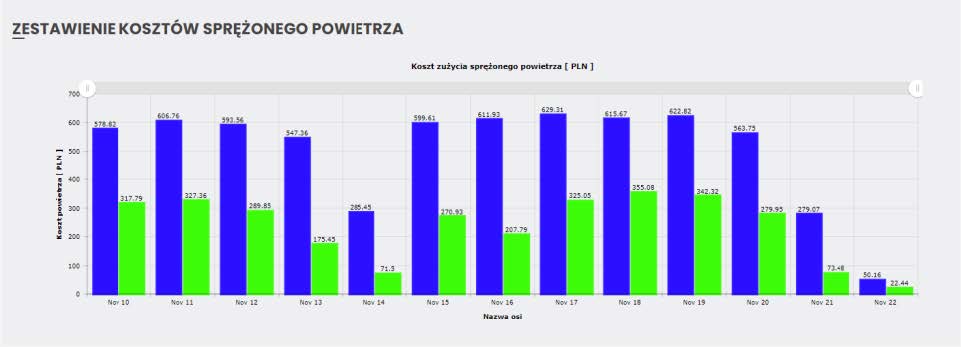
Różnice w zużyciu dziennym są ogromne co przekłada się na znacznie mniejsze koszty wytwarzania sprężonego powietrza. Przyjmując średnią dzienną różnicę zużycia na poziomie około 250-300zł Zakład B oszczędza rocznie około 90 000 do 110 000 PLN.
Skąd się biorą takie różnice? To straty jakie generuje instalacja. Wszelkiego rodzaju nieszczelności i błędy połączeniowe przez 10 lat funkcjonowania Zakładu nr 1 doprowadziły do nieświadomego zakupu dodatkowej sprężarki, której głównym zadaniem jest uzupełniania ubytków – 24h/dobę, 365 dni w roku. To oczywista strata i możemy się tylko domyślać od jakiego okresu może to trwać.
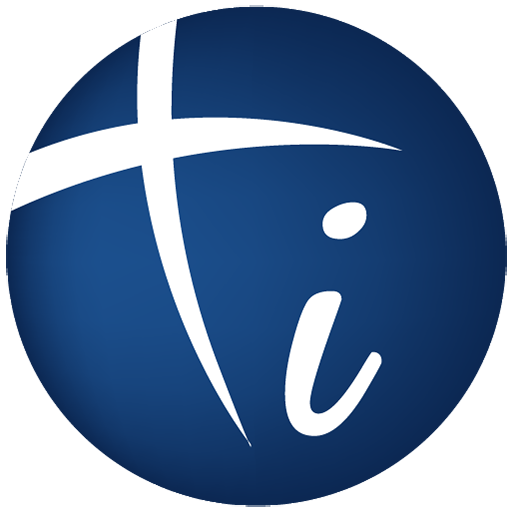
Dwa sposoby na kontrolę wydajności urządzeń w zakładzie produkcyjnym
- Usługi firm zewnętrznych polegające na okresowym montażu różnego rodzaju systemów pomiarowych, które niestety najczęściej polegają na kopiowaniu sygnałów cyfrowych ze styczników lub elektrozaworów aktywujących tłoczenie/bieg jałowy sprężarki. Niestety nie mamy wtedy ciągłego monitoringu i nigdy nie będzie możliwości wykrycia nagłego pogorszenia stanu instalacji.
- Zainwestować we własny przepływomierz oraz podpiąć go do systemu IPLAS. Co uzyskamy:
- Ciągły i niezależny pomiar automatycznie archiwizowany. Dostęp do raportów z każdego miejsca na ziemi.
- Możliwość automatycznego przeliczania zużycia powietrza na kWh lub PLN
- Kontrolę poziomu zużycia powietrza w dni wolne od pracy – IPLAS może automatycznie badać zużycie/przepływ i informować, gdy zadane progi zostaną przekroczone. Nasza reakcja może więc być natychmiastowa
- Wstępną lokalizację obszarów występowania nieszczelności – gdy instalacja jest podzielona możemy odcinać część instalacji i sprawdzać wielkość przepływu/ubytku. To pierwsze etap lokalizacji, później trzeba już skorzystać z profesjonalnych wykrywaczy nieszczelności.
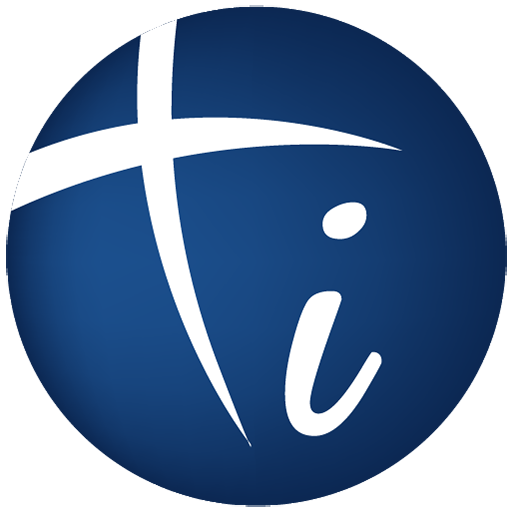
Podsumowanie case study
Wspomniana sytuacja jest modelem przygotowanym na potrzeby Case Study i naszego DEMO, bazuje na rzeczywistych sytuacjach z jakimi spotkaliśmy w trakcie realizacji zadań powierzonych przez naszych klientów. Wielu z nich nie zdaje sobie nawet sprawy, jak wielkie straty ponoszą. Pozornie wszystko funkcjonuje bardzo dobrze, jednak nie oznacza to, że nie można poprawić sytuacji i niewielkim kosztem przejąć kontrolę nad całym procesem wytwarzania. Podpinając liczniki zużycia energii pod każdą ze sprężarek osobno, możemy w prosty sposób wyznaczać koszt wytworzenie sprężonego powietrza w odniesieniu np. do wielkości produkcji. Możliwości są naprawdę ogromne, a ewentualne koszty początkowe niewielkie.
+48 883 366 717