Wstęp
Przemysł produkcyjny stoi u progu kolejnej wielkiej zmiany. Coraz częściej mówi się o „czwartej rewolucji przemysłowej” czy „Przemyśle 4.0” jako o kierunku rozwoju nowoczesnych fabryk. Dla dyrektorów operacyjnych, kierowników zakładów i osób odpowiedzialnych za strategię w firmach produkcyjnych pojawia się pytanie: co tak naprawdę kryje się za pojęciem Przemysłu 4.0 i jak może ono wpłynąć na naszą organizację? Niniejszy artykuł wyjaśnia, czym jest czwarta rewolucja przemysłowa – łącząc perspektywę technologiczną i strategiczną. Unikamy jednak nadmiernych szczegółów technicznych, skupiając się na praktycznym znaczeniu koncepcji. Dowiesz się tu zarówno, jakie kluczowe technologie definiują Przemysł 4.0, jak i jakie zmiany organizacyjne i kulturowe są niezbędne, by w pełni skorzystać z jego potencjału. Omówimy również najczęstsze wyzwania i mity związane z transformacją cyfrową oraz zasugerujemy od czego zacząć wdrażanie Przemysłu 4.0 w swoim przedsiębiorstwie.
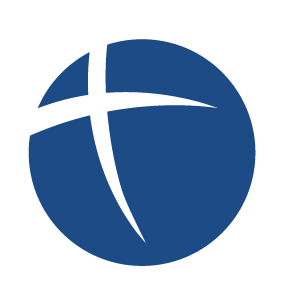
Od maszyny parowej do inteligentnej fabryki – krótki rys historyczny
Mianem Przemysłu 4.0 (czwartej rewolucji przemysłowej) określamy więc nową epokę w dziejach produkcji, w której zaawansowane technologie cyfrowe przenikają każdy aspekt działalności przemysłowej. Termin narodził się około dekadę temu w Niemczech jako element strategii unowocześnienia przemysłu, mającej zwiększyć produktywność i konkurencyjność fabryk. Dziś koncepcja ta zyskała globalne znaczenie i jest odpowiedzią na nową fazę rozwoju przemysłu, rozgrywającą się na naszych oczach. W odróżnieniu od poprzednich rewolucji, które dotyczyły mechanizacji, elektryfikacji czy automatyzacji pojedynczych procesów, Przemysł 4.0 oznacza kompleksową cyfryzację i integrację całych systemów produkcyjnych oraz łańcuchów wartości. Mówiąc najprościej, fizyczna produkcja i operacje zostają połączone z inteligentnymi technologiami cyfrowymi, uczeniem maszynowym i analizą ogromnych zbiorów danych, tworząc bardziej holistyczny, zintegrowany ekosystem przemysłowy. Co ważne, zakres Przemysłu 4.0 wykracza poza samą halę produkcyjną. Obejmuje on cały cykl życia produktu oraz pełny łańcuch dostaw – od fazy projektowania i planowania, przez zarządzanie zaopatrzeniem i produkcją, aż po sprzedaż, logistykę oraz obsługę klienta przed i po sprzedaży. Innymi słowy, czwarta rewolucja przemysłowa wpływa na wszystkie obszary funkcjonowania przedsiębiorstwa produkcyjnego i wymusza spojrzenie na biznes w nowy sposób. To nie tylko automatyzacja maszyn, ale także cyfryzacja informacji o produktach, procesach i klientach oraz tworzenie zupełnie nowych modeli biznesowych opartych na tych danych.Kluczowe cechy i technologie Przemysłu 4.0
Przemysł 4.0 bywa w skrócie kojarzony z terminami takimi jak „Internet Rzeczy” czy „inteligentna produkcja”, ale w istocie stanowi zbiór wielu powiązanych technologii i koncepcji. To właśnie ich integracja napędza przemysłową transformację cyfrową. Poniżej przedstawiamy najważniejsze technologie definiujące Przemysł 4.0 – z krótkim objaśnieniem ich roli w nowoczesnej fabryce:- Internet Rzeczy (IoT) – sieć fizycznych urządzeń połączonych z internetem, które komunikują się i wymieniają dane. W przemyśle oznacza to czujniki i maszyny zdolne do zbierania informacji (np. o stanie maszyn, warunkach produkcji czy lokalizacji produktów) i przesyłania ich w czasie rzeczywistym do innych systemów. Dzięki IoT fabryka staje się „uzbrojona” w zmysły – możliwe jest zdalne monitorowanie pracy urządzeń, śledzenie parametrów procesów oraz szybkie wychwytywanie anomalii. Dane zebrane przez IoT stanowią podstawę do dalszej analizy i optymalizacji procesów.
- Big Data i analityka danych – pod tą nazwą kryje się zdolność do gromadzenia oraz przetwarzania olbrzymich zbiorów danych produkcyjnych. W nowoczesnej fabryce dane pochodzą z maszyn, linii technologicznych, systemów IT, czujników IoT, a nawet od klientów. Analiza Big Data (często z użyciem AI) pozwala dostrzec wzorce i zależności niemożliwe do wykrycia gołym okiem. Przykładowo, dzięki analizie danych historycznych można prognozować awarie maszyn (predictive maintenance), optymalizować parametry produkcji, lepiej planować zaopatrzenie czy personalizować ofertę pod indywidualne potrzeby odbiorców. Dane stały się nowym „paliwem” przemysłu – to na ich podstawie podejmowane są decyzje usprawniające działanie firm.
- Sztuczna inteligencja (AI) i uczenie maszynowe – czyli algorytmy zdolne do wyciągania wniosków z danych i podejmowania decyzji. W przemyśle 4.0 AI analizuje zbierane dane (np. wyniki pomiarów jakości, parametry pracy urządzeń, zmienne rynkowe) i na tej podstawie rekomenduje lub automatycznie wprowadza usprawnienia. Uczenie maszynowe może służyć do wykrywania wad produktów na liniach montażowych (systemy wizyjne z AI), przewidywania popytu na podstawie trendów sprzedaży lub optymalizacji harmonogramu produkcji w zależności od dziesiątek czynników. W efekcie komputery „uczą się” procesów produkcyjnych, by stale je ulepszać – szybciej, niż byłby to w stanie zrobić człowiek.
- Chmura obliczeniowa (cloud computing) – model dostarczania mocy obliczeniowej i przestrzeni do przechowywania danych przez internet, bez konieczności utrzymywania kosztownej infrastruktury IT na miejscu. W kontekście fabryk chmura pozwala na centralne gromadzenie i przetwarzanie danych z wielu źródeł (maszyn, systemów, czujników) w jednym wirtualnym środowisku. Umożliwia to dostęp do informacji w czasie rzeczywistym z dowolnej lokalizacji (także z poziomu urządzeń mobilnych), ułatwia współdzielenie danych między działami czy nawet firmami (dostawcy, klienci) oraz korzystanie z zaawansowanych narzędzi analitycznych bez budowania własnych serwerowni. Chmura to także elastyczność – moce obliczeniowe można skalować w górę lub w dół w zależności od potrzeb biznesu.
- Automatyzacja i robotyzacja – choć automatyzacja procesów nie jest nowością (trwa od lat 70. XX w.), w ramach Przemysłu 4.0 zyskuje nowy wymiar dzięki integracji z systemami informatycznymi i AI. Roboty przemysłowe stają się coraz bardziej autonomiczne, precyzyjne i skomunikowane – potrafią same zgłaszać potrzebę serwisu czy dostosowywać swoje działania na podstawie danych. Pojawiają się roboty współpracujące (coboty), które mogą pracować ramię w ramię z ludźmi, przejmując ciężkie lub monotonne czynności. Automatyzacji podlegają nie tylko fizyczne operacje (jak montaż, pakowanie), ale też procesy administracyjne – dzięki systemom klasy RPA (Robotic Process Automation) możliwe jest zautomatyzowanie powtarzalnych zadań biurowych, planistycznych czy logistycznych. Celem jest zwiększenie wydajności i odciążenie ludzi od zadań, które może lepiej wykonać maszyna.
- Cyfrowe bliźniaki (digital twins) – wirtualne repliki fizycznych obiektów, procesów lub systemów. Technologia cyfrowych bliźniaków umożliwia stworzenie w komputerze dokładnego modelu np. maszyny, linii produkcyjnej czy całej fabryki, który zachowuje się tak jak realny odpowiednik. Dzięki temu inżynierowie i menedżerowie mogą symulować zmiany (np. testować nowy układ linii, parametry pracy urządzenia, scenariusze awarii) w świecie wirtualnym, bez ryzyka przestojów i kosztów w świecie rzeczywistym. Cyfrowy bliźniak pozwala też na bieżąco monitorować proces – model pobiera dane z sensorów maszyny i pokazuje jej stan w czasie rzeczywistym. To narzędzie potężnie wspierające utrzymanie ruchu, planowanie produkcji i projektowanie – pozwala „przewidzieć przyszłość” zanim dokona się realnych zmian w fabryce.
- Sieci 5G i komunikacja bezprzewodowa – szybkie, niezawodne sieci przemysłowe są krwiobiegiem inteligentnej fabryki. Standard 5G, w porównaniu do dotychczasowych Wi-Fi czy 4G, oferuje znacznie większą przepustowość, niezawodność oraz minimalne opóźnienia. Dla Przemysłu 4.0 oznacza to możliwość bezprzewodowego łączenia tysięcy urządzeń (czujników, maszyn, pojazdów AGV) w czasie rzeczywistym na terenie zakładu. 5G umożliwia np. zdalne sterowanie maszynami i robotami z minimalnym opóźnieniem, błyskawiczną komunikację między autonomicznymi wózkami czy monitorowanie procesów produkcyjnych online bez przerw. Dzięki temu fabryka staje się jeszcze bardziej elastyczna – łatwiej przeorganizować linię (urządzenia nie muszą być “na kablu”), a dane płyną nieprzerwanie nawet w dynamicznym, ruchomym środowisku.
- Integracja systemów (IT/OT) – fundamentem Przemysłu 4.0 jest wzajemne połączenie wszystkich elementów ekosystemu produkcyjnego w jedną sieć wymiany informacji. Integracja ta zachodzi na dwóch poziomach: pionowym (wewnątrz organizacji, od poziomu czujników i maszyn na hali aż po systemy zarządcze i analityczne na poziomie biura) oraz poziomym (między firmą a zewnętrznymi partnerami – dostawcami, klientami, operatorami logistycznymi). W praktyce integracja pionowa oznacza, że dane płyną z maszyn i sterowników produkcyjnych do systemów IT przedsiębiorstwa (np. ERP, MES) i odwrotnie – decyzje zarządcze (np. plan produkcji) automatycznie trafiają do maszyn. Z kolei integracja pozioma oznacza łączenie się systemów różnych firm wzdłuż łańcucha wartości – np. udostępnianie dostawcom informacji o bieżącym zapotrzebowaniu, zdalny wgląd klienta w status produkcji zamówionego produktu, itp. Ta wszechstronna integracja rozbija tradycyjne silosy informacyjne i pozwala działać całemu łańcuchowi dostaw jak jednemu spójnemu organizmowi. Przemysł 4.0 w dużej mierze polega właśnie na płynnym przepływie danych pomiędzy ludźmi, maszynami i systemami w całej sieci tworzenia wartości – tak, aby właściwe informacje docierały w odpowiednim czasie tam, gdzie są potrzebne.
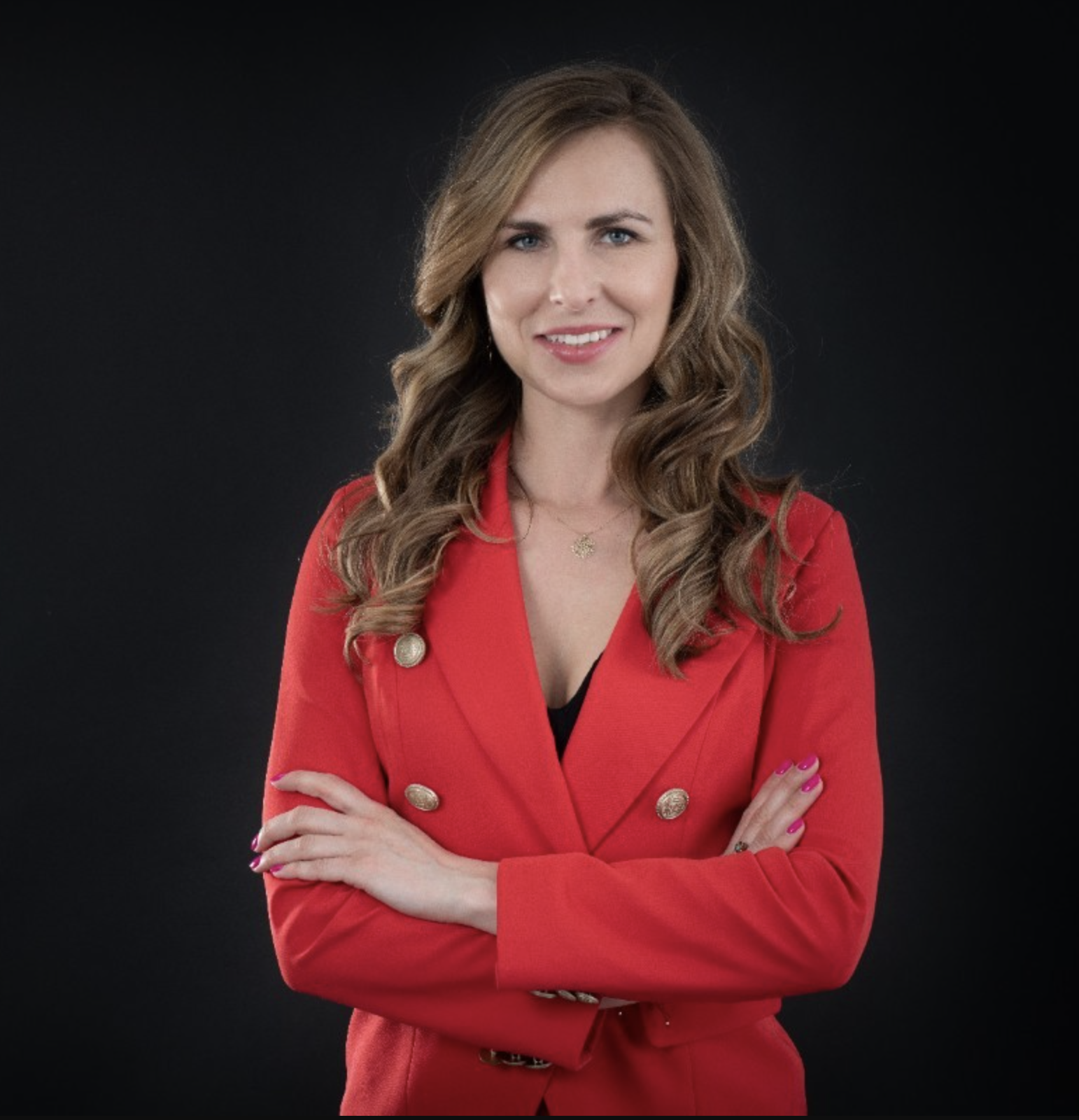
Monika Nowak
Dyrektor projektu iPLAS
Zbieraj dane z całej produkcji w jednym miejscu
iPLAS integruje dane z maszyn, procesów automatycznych i manualnych w czasie rzeczywistym. Bezpiecznie przechowujemy je w chmurze lub na Twoim serwerze, a dzięki zaawansowanemu przetwarzaniu danych zyskasz pełen wgląd w swoją produkcję.
Zmiany organizacyjne, kompetencyjne i kulturowe w erze 4.0
Wdrożenie rozwiązań Przemysłu 4.0 nie sprowadza się wyłącznie do zakupu nowoczesnych urządzeń czy instalacji nowych systemów IT. To przede wszystkim głęboka transformacja całego przedsiębiorstwa – jego kultury, struktury organizacyjnej oraz kompetencji pracowników. Jak zauważają eksperci, transformacja w kierunku Przemysłu 4.0 będzie wymagała zmiany kultury organizacyjnej firmy, rozwoju nowych kompetencji oraz nowych sposobów działania zespołów. Innymi słowy, firmy muszą ewoluować nie tylko technologicznie, ale i organizacyjnie, by wykorzystać potencjał czwartej rewolucji. O jakich zmianach mówimy konkretnie? Poniżej kluczowe aspekty przemiany organizacyjnej w dobie Przemysłu 4.0:- Nowe kompetencje i role pracowników: W cyfrowej fabryce rośnie zapotrzebowanie na umiejętności z pogranicza IT i inżynierii. Pracownicy produkcyjni muszą coraz częściej rozumieć działanie systemów informatycznych, analizować dane czy nadzorować zautomatyzowane procesy zamiast wykonywać wyłącznie manualne operacje. Pojawiają się nowe role, takie jak analitycy danych przemysłowych, inżynierowie ds. IoT, specjaliści od AI, a także koordynatorzy integracji IT/OT. Firmy stają przed wyzwaniem doskonalenia kwalifikacji obecnej kadry (upskilling) lub pozyskiwania nowych talentów z rynku posiadających kompetencje 4.0. W praktyce oznacza to inwestycje w szkolenia, bliską współpracę działów HR z działami technicznymi oraz budowanie ścieżek rozwoju dla pracowników w obszarach automatyzacji i cyfryzacji.
- Zmiana kultury organizacyjnej: Sukces wdrożenia Przemysłu 4.0 w dużej mierze zależy od kultury panującej w firmie. Organizacja musi stać się bardziej otwarta na zmiany i innowacje, skłonna do eksperymentowania i ciągłego uczenia się. Tradycyjne silosy działowe (produkacja vs. IT vs. utrzymanie ruchu) powinny ustąpić miejsca zespołom międzyfunkcyjnym, które wspólnie rozwiązują problemy i wdrażają usprawnienia. Ważna jest też kultura oparta na danych – decyzje podejmowane na podstawie rzetelnych analiz zamiast wyłącznie na doświadczeniu czy intuicji. Menedżerowie muszą promować postawę, że technologia jest sojusznikiem pracownika, a nie zagrożeniem. Otwartość komunikacji, zaufanie i zaangażowanie załogi w proces zmian są czynnikami krytycznymi – bez nich nawet najlepsza strategia cyfryzacji może utknąć w martwym punkcie.
- Elastyczna struktura i zarządzanie zmianą: Firmy wdrażające Przemysł 4.0 często przechodzą reorganizację struktur, aby lepiej integrować kompetencje informatyczne z produkcyjnymi. Pojawiają się dedykowane działy lub zespoły ds. transformacji cyfrowej, które koordynują projekty 4.0 w całej organizacji. Jednocześnie przedsiębiorstwo musi zyskać zdolność do zwinnego działania (agile) – szybkiego testowania nowych rozwiązań w małej skali i ich iteracyjnego usprawniania. Tradycyjne hierarchie i długie łańcuchy decyzyjne bywają zbyt ociężałe w obliczu konieczności dynamicznych zmian – stąd trend do spłaszczania struktur i delegowania uprawnień bliżej „gemba” (miejsca, gdzie dzieje się realna wartość). Kluczowe jest też aktywne zarządzanie zmianą: czyli planowe komunikowanie celów transformacji, angażowanie pracowników na wczesnym etapie wdrożeń oraz świętowanie nawet drobnych sukcesów, aby budować pozytywne nastawienie do nowych technologii.
Wyzwania i błędne przekonania związane z Przemysłem 4.0
Mimo rosnącej świadomości korzyści, jakie niesie cyfryzacja produkcji, w wielu firmach pokutują różne obawy i mity na temat Przemysłu 4.0. Warto się z nimi zmierzyć, gdyż mogą one hamować decyzje o inwestycjach i utrudniać transformację. Poniżej omówiono kilka najczęstszych błędnych przekonań – wraz z wyjaśnieniem, jak jest naprawdę:- Mit: „Przemysł 4.0 to tylko roboty na hali produkcyjnej”. Rzeczywistość: owszem, robotyzacja jest ważnym elementem czwartej rewolucji, ale jej istotą nie są wyłącznie roboty. Przemysł 4.0 obejmuje cały ekosystem technologii: od czujników IoT, przez systemy analityczne i AI, po platformy komunikacyjne i chmurowe. Już kilka lat temu autorzy koncepcji zauważyli, że Przemysł 4.0 to nie tylko roboty i wzrost produktywności, ale zupełnie nowe podejście do działalności produkcyjnej, wpływające na otoczenie i wzmacniające potencjał ludzki. Innymi słowy – to rewolucja nie tylko technologiczna, ale i biznesowa. Same roboty były już w trzeciej rewolucji; czwarta polega na uczynieniu z maszyn elementów inteligentnej, połączonej sieci, gdzie dane są równie ważne jak fizyczne produkty.
- Mit: „Czwarta rewolucja jest tylko dla wielkich korporacji”. W rzeczywistości transformacja 4.0 jest możliwa i potrzebna także w małych i średnich firmach. Często spotykamy się z przekonaniem, że tylko globalne koncerny stać na zaawansowane technologie, a mniejsze zakłady „jeszcze nie dorosły” do robotów czy systemów AI. To błędne myślenie – istnieje już wiele przykładów MŚP, które z powodzeniem wprowadziły elementy inteligentnej produkcji i odniosły dzięki temu sukces. Jak podkreślają eksperci, nie tylko wielkie korporacje mogą z powodzeniem wdrażać założenia Przemysłu 4.0. Co więcej, mniejszym firmom często sprzyja większa zwinność i krótsze ścieżki decyzyjne – mogą szybciej testować innowacje na swojej skali produkcji. Wiele nowoczesnych technologii (np. czujniki IoT, usługi chmurowe) stało się też dostępnych „na wyciągnięcie ręki” – ich koszty spadły, pojawiły się modele wynajmu czy abonamentu zamiast dużych inwestycji jednorazowych. Ważne jest zatem nastawienie: zaczynać od małych kroków, tam gdzie widzimy potencjał poprawy, zamiast czekać, aż „inni przetrą szlaki”.
- Mit: „Wdrożenie Przemysłu 4.0 wymaga wymiany całego parku maszynowego i kosztuje fortunę”. To jedna z częstszych obaw – że cyfryzacja oznacza wyrzucenie dotychczasowych maszyn i ogromne nakłady. Owszem, pewne inwestycje są konieczne, ale podejście all-or-nothing jest niewskazane. Wcale nie trzeba przeprowadzać radykalnej rewolucji od razu – często wystarczy jedno dobrze dobrane rozwiązanie, by znacząco usprawnić wybrany proces. Przykładowo, do istniejących urządzeń można dodawać czujniki (retrofitting IoT), by zacząć zbierać dane, zamiast kupować od razu nowe „smart machines”. Można też korzystać z modeli finansowania (leasing sprzętu, wynajem robotów, chmura obliczeniowa zamiast własnych serwerów), co redukuje początkowe koszty wejścia. Istnieją dziś rozwiązania modułowe, skalowalne, które pozwalają unowocześnić nawet starsze linie produkcyjne stopniowo. Krótko mówiąc: transformacja 4.0 nie musi być „rewolucją za miliony” – lepiej myśleć o niej jako o ciągłej ewolucji, gdzie inwestycje rozłożymy w czasie i skupimy na najbardziej opłacalnych obszarach.
- Mit: „Automatyzacja zabierze ludziom pracę”. Obawa przed zastąpieniem pracowników przez maszyny towarzyszy automatyzacji od zawsze. Przemysł 4.0 także rodzi pytania o przyszłość pracy. Jak wygląda prawda? Dotychczasowe doświadczenia pokazują, że człowiek nadal pozostaje kluczowym ogniwem inteligentnej fabryki – zmienia się jednak charakter jego pracy. W przedsiębiorstwach, które wdrażają rozwiązania 4.0, człowiek nie przestał być potrzebny i nie przestanie – do zarządzania zautomatyzowaną produkcją, integrowania systemów i tworzenia sieci potrzebnych jest wielu świetnie wykształconych pracowników. Automatyzacja przejmuje zadania monotonne, niebezpieczne lub wymagające wielkiej siły, co pozwala ludziom skupić się na zadaniach o wyższej wartości dodanej (np. analiza danych, doskonalenie procesów, nadzór nad nowymi projektami). Równocześnie powstają nowe miejsca pracy, które wcześniej nie istniały – od programistów robotów po specjalistów od utrzymania infrastruktury IoT. Według raportu Światowego Forum Ekonomicznego, rozwój automatyzacji i nowych technologii netto może zwiększyć zatrudnienie – szacuje się, że na każde 75 mln „zanikających” miejsc pracy przypadnie 133 mln nowych, o innym profilu. Oczywiście wymaga to przekwalifikowania części pracowników, ale wiele firm stawia na retraining swojej załogi, zamiast redukcji. W praktyce Przemysł 4.0 oznacza więc raczej zmianę kwalifikacji niż masowe bezrobocie. Warto komunikować załodze te pozytywy i angażować ją w proces zmian, aby obawy przed nowościami nie blokowały postępu.
- Mit: „Cyfrowa transformacja to głównie problem działu IT, a produkcja może działać jak dawniej”. W niektórych organizacjach pokutuje przekonanie, że wdrożenie systemów informatycznych czy analityki danych to zadanie dla specjalistów IT, bez większego wpływu na codzienną pracę produkcji. Jest to bardzo błędne podejście. Przemysł 4.0 wymaga ścisłego partnerstwa między zespołami produkcyjnymi a zespołami IT. Granica między klasycznym OT (Operational Technology – maszyny, urządzenia, sterowniki) a IT zaciera się – fabryka przyszłości potrzebuje kompetencji hybrydowych. Jeśli produkcja i utrzymanie ruchu nie będą zaangażowane w cyfrowe projekty, systemy mogą zostać źle dopasowane do realiów hali fabrycznej i nie przyniosą oczekiwanej wartości. Z kolei specjaliści IT muszą dobrze rozumieć procesy produkcyjne, by tworzyć rozwiązania odpowiadające na faktyczne potrzeby operacyjne. Dlatego transformacja cyfrowa powinna być traktowana jako wspólna strategia całej firmy, a nie odizolowany projekt działu informatyki. Tylko wtedy innowacje rzeczywiście zakorzenią się w procesach i przyniosą trwałe rezultaty.
- Wyzwanie: bezpieczeństwo danych i systemów. Wraz z postępującą cyfryzacją rośnie też ekspozycja firm na ryzyka cybernetyczne. Cyberbezpieczeństwo staje się kluczowym elementem Przemysłu 4.0, ponieważ zwiększona łączność i automatyzacja procesów stwarzają nowe możliwości ataków hakerskich. Awaria lub włamanie do systemu sterowania produkcją może zatrzymać fabrykę; wyciek danych technologicznych może narazić firmę na straty konkurencyjne. Dlatego każdy plan transformacji powinien obejmować inwestycje w zabezpieczenia – od szyfrowania komunikacji i segmentacji sieci OT/IT, po systemy wykrywania intruzów i szkolenia personelu z zasad bezpieczeństwa. Świadomość zagrożeń musi iść w parze z wdrażaniem nowych technologii. Na szczęście rośnie dostępność rozwiązań chroniących przemysłowe systemy (tzw. Industrial Security), a także dobrych praktyk (jak regularne audyty bezpieczeństwa, aktualizacje oprogramowania urządzeń, polityki haseł itp.). Wyzwanie polega na tym, by bezpieczeństwo nie było traktowane jako dodatek, lecz integralna część każdej wdrażanej technologii.
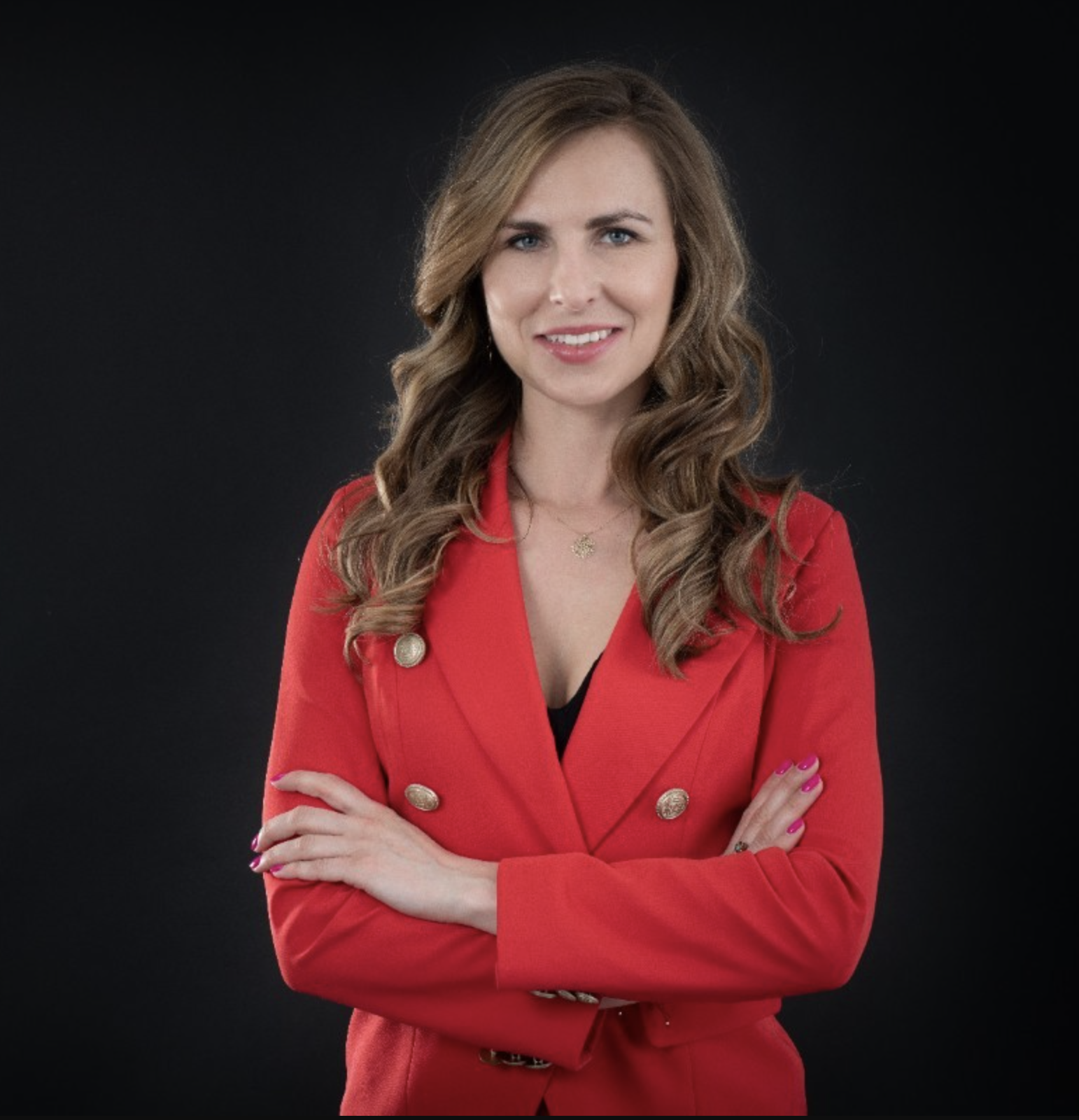
Monika Nowak
Dyrektor projektu iPLAS
Zbieraj dane z całej produkcji w jednym miejscu
iPLAS integruje dane z maszyn, procesów automatycznych i manualnych w czasie rzeczywistym. Bezpiecznie przechowujemy je w chmurze lub na Twoim serwerze, a dzięki zaawansowanemu przetwarzaniu danych zyskasz pełen wgląd w swoją produkcję.
Jak zacząć transformację 4.0 – praktyczne podejście dla firm
Skala zmian, jakie niesie Przemysł 4.0, może wydawać się przytłaczająca. Każda firma jest inna – różni się poziomem automatyzacji, kulturą, możliwościami finansowymi – więc nie ma jednej uniwersalnej ścieżki wdrożenia. Istnieje jednak kilka ogólnych zasad i kroków, które pomogą skutecznie zaplanować i przeprowadzić transformację cyfrową przedsiębiorstwa. Przede wszystkim należy pamiętać, że cyfryzacja to proces długofalowy, a nie jednorazowy projekt – wymaga przemyślanej strategii i zaangażowania wielu poziomów organizacji. Dobrze przeprowadzona zmiana obejmie zarówno inwestycje w technologie, jak i zmiany w strukturze organizacyjnej i kompetencjach ludzi. Jak się za to zabrać w praktyce? Poniżej proponowane kroki, od których warto zacząć:- Zdefiniuj cele biznesowe i wizję Przemysłu 4.0 w swojej firmie. Każda transformacja powinna zaczynać się od precyzyjnego określenia celów, które chcemy osiągnąć. Zastanów się, co ma dać Twojej firmie wdrożenie koncepcji 4.0 – czy chodzi o zwiększenie wydajności i obniżenie kosztów? Poprawę jakości wyrobów? Większą elastyczność produkcji i szybsze reagowanie na potrzeby klientów? A może rozwój zupełnie nowych usług (np. serwisowanie predykcyjne, produkcja spersonalizowana)? Cele powinny wynikać z ogólnej strategii biznesowej firmy – transformacja cyfrowa ma służyć strategii, a nie odwrotnie. Sformułuj 2–3 główne priorytety (np. redukcja przestojów o 20% w 2 lata, skrócenie czasu realizacji zamówienia o połowę, wejście na rynek usług cyfrowych dla klienta). Ważne, by cele były mierzalne i realistyczne, ale zarazem na tyle ambitne, aby motywowały organizację do działania.
- Przeprowadź diagnozę stanu obecnego (tzw. assessment cyfrowy). Zanim ruszysz do przodu, zobacz gdzie jesteś teraz. Oceń szczero ze swoim zespołem, na jakim etapie dojrzałości cyfrowej jest Twoje przedsiębiorstwo. Przeanalizuj kluczowe obszary: poziom automatyzacji maszyn, stopień wykorzystywania danych do podejmowania decyzji, integrację systemów (czy produkcja „rozmawia” z ERP, czy dane z maszyn są gdzieś gromadzone i analizowane), kompetencje cyfrowe kadry, kulturę organizacyjną (czy pracownicy są otwarci na zmiany, czy panuje raczej zachowawczość?). Możesz skorzystać z dostępnych modeli oceny dojrzałości Przemysłu 4.0 lub poprosić o audyt zewnętrzny. Taka diagnoza wskaże mocne strony, które można rozbudować oraz luki, które wymagają uzupełnienia. Przykładowo, audyt może wykazać, że masz nowoczesny park maszynowy, ale dane z niego nie są nigdzie zbierane i analizowane – to cenna informacja gdzie leży potencjał.
- Wybierz obszary o najwyższym potencjale i zacznij od pilotażu. Mając zidentyfikowane potrzeby i cele, określ priorytetowe obszary do cyfryzacji. Nie próbuj od razu objąć wszystkiego – lepiej wybrać 1–2 konkretne zagadnienia, gdzie spodziewasz się szybkich i wymiernych efektów. Może to być na przykład: wdrożenie systemu monitorowania pracy maszyn (IoT) na krytycznej linii produkcyjnej w celu redukcji przestojów, albo uruchomienie pilotażowo cyfrowego systemu zarządzania magazynem w jednym oddziale firmy. Ważne, by pilot był na tyle mały, aby dało się nim sprawnie zarządzać i uczyć na błędach, ale na tyle istotny, by jego sukces przekonał sceptyków. Określ mierniki sukcesu pilota (KPI) – np. czy udało się osiągnąć zakładaną redukcję awarii o X%, czy skrócił się czas przezbrojenia linii, czy poprawiła się terminowość dostaw itp. Rozpoczęcie od pilotażu pozwoli Twojemu zespołowi zdobyć doświadczenie z nowymi technologiami na małą skalę i zrozumieć, jak integrują się one z istniejącymi procesami.
- Zapewnij zaangażowanie kadry i rozwijaj kompetencje. Nawet najlepszy plan może spalić na panewce, jeśli zabraknie ludzi, którzy go udźwigną. Dlatego od początku buduj multidyscyplinarny zespół projektowy obejmujący zarówno specjalistów IT, automatyków, jak i przedstawicieli produkcji, jakości, logistyki etc. Wyznacz lidera projektu (lub lidera transformacji 4.0), który będzie koordynował działania i komunikował się z kierownictwem. Jednocześnie identyfikuj wśród załogi „agentów zmiany” – osoby otwarte na nowe technologie, chętne do nauki, cieszące się autorytetem w swoich działach. Mogą oni pełnić rolę ambasadorów Przemysłu 4.0, tłumacząc korzyści kolegom i zgłaszając oddolnie pomysły usprawnień. Zainwestuj też w szkolenia tam, gdzie widać braki kompetencyjne – czy to w zakresie podstaw analizy danych dla inżynierów procesu, czy obsługi robotów dla mechaników utrzymania ruchu. Pokaż pracownikom, że transformacja to szansa rozwoju dla nich, a nie zagrożenie. Transparentna komunikacja (np. regularne spotkania informacyjne o postępach projektu, pokazywanie małych „sukcesów” pilota) pomoże utrzymać wysoki poziom zaangażowania i przełamać naturalny opór przed zmianą.
- Skonstruuj architekturę techniczną i postaw na integrację systemów. Na etapie planowania kolejnych kroków pomyśl o docelowej architekturze cyfrowej Twojej firmy. Ważne jest, aby uniknąć pułapki „wysp” – wdrażania pojedynczych aplikacji czy maszyn, które nie komunikują się z resztą. Dlatego kładź nacisk na rozwiązania otwarte, umożliwiające integrację (np. standardy komunikacyjne w urządzeniach IoT, API w oprogramowaniu). Rozważ, jakie systemy będą potrzebne: MES do nadzoru produkcji? Platforma IoT do zbierania danych z maszyn? System analityczny BI do raportowania KPI? Być może konieczna będzie modernizacja infrastruktury sieciowej (np. instalacja sieci bezprzewodowej na produkcji, segmentacja sieci dla bezpieczeństwa). Tutaj warto korzystać z wiedzy ekspertów – integratorów systemów, dostawców technologii lub konsultantów, którzy pomogą zaprojektować skalowalną i bezpieczną architekturę zgodną z potrzebami. Dobra architektura zapewni, że kolejne wdrożenia (po pilotażu) będą już elementami większej układanki, a nie oderwanymi inicjatywami.
- Wdrażaj stopniowo, mierz efekty i doskonal się iteracyjnie. Po pomyślnym pilotażu przychodzi czas na skalowanie rozwiązań na resztę organizacji. Rób to krok po kroku, ucząc się na dotychczasowych doświadczeniach. Każde wdrożenie traktuj jak projekt z jasno zdefiniowanymi celami biznesowymi i miernikami sukcesu. Regularnie mierz postępy: czy np. rok po wdrożeniu systemu IoT rzeczywiście zmniejszyła się liczba awarii? Czy planowana oszczędność kosztów została osiągnięta? Monitorowanie KPI pozwoli uzasadnić dalsze inwestycje i korygować kurs tam, gdzie efekty są poniżej oczekiwań. Bądź przygotowany na to, że nie wszystko zadziała od razu idealnie – traktuj porażki jako lekcje. W ramach organizacji buduj mechanizmy ciągłego doskonalenia: powołaj fora wymiany wiedzy o nowych technologiach, dziel się case studies wewnętrznie, zachęcaj zespoły do zgłaszania usprawnień. Transformacja 4.0 tak naprawdę nigdy się nie kończy – technologia wciąż się rozwija, konkurencja nie śpi, więc i Twoja firma powinna mieć kulturę permanentnego ulepszania.
- Zapewnij wsparcie najwyższego kierownictwa i długofalową perspektywę. Na koniec – ale absolutnie kluczowe – upewnij się, że zarząd firmy aktywnie wspiera cyfrową transformację. Bez sponsora na wysokim szczeblu trudno będzie pokonać opory organizacyjne czy uzyskać środki na kolejne etapy. Kierownictwo powinno nie tylko zatwierdzić budżet, ale przede wszystkim komunikować wizję 4.0 jako priorytet strategiczny. Dobrą praktyką jest włączenie elementów cyfryzacji do mapy strategicznej przedsiębiorstwa i regularne omawianie postępów na odprawach kierownictwa. Ważne jest też cierpliwe, długofalowe podejście – efekty pełnej transformacji mogą wymagać lat pracy, więc nie można oczekiwać cudów po jednym kwartale. Top management musi więc wyznaczać realistyczne kamienie milowe, nagradzać postępy i utrzymywać konsekwencję mimo ewentualnych krótkoterminowych niepowodzeń. Tylko wtedy organizacja niższego szczebla uwierzy, że „to nie jest kolejna moda, która minie”, lecz stały kierunek rozwoju firmy.
Podsumowanie
Przemysł 4.0 to coś więcej niż tylko zbiór nowych technologii – to nowy sposób myślenia o biznesie produkcyjnym. Czwarta rewolucja przemysłowa łączy świat maszyn, systemów IT i ludzi w jedną, inteligentną całość, umożliwiając skokową poprawę efektywności, jakości i elastyczności przedsiębiorstw. Dla kadry menedżerskiej oznacza to z jednej strony wyzwanie (trzeba poprowadzić organizację przez zmianę technologiczną i kulturową), ale z drugiej strony ogromną szansę. Firmy, które potrafią wykorzystać potencjał IoT, danych i sztucznej inteligencji, zyskują przewagi konkurencyjne – są w stanie szybciej reagować na zmiany rynkowe, oferować klientom lepiej dopasowane produkty, optymalnie wykorzystywać zasoby i obniżać koszty operacyjne. W środowisku zażartej globalnej konkurencji Przemysł 4.0 staje się wręcz nieodłącznym elementem sukcesu. To już nie pytanie czy, ale jak wejść na drogę cyfrowej transformacji. Podsumowując, czwarta rewolucja przemysłowa to podróż, którą prędzej czy później odbędzie większość przedsiębiorstw produkcyjnych. Nie musi ona przebiegać gwałtownie – kluczem jest świadoma strategia, małe kroki i stałe uczenie się na własnych doświadczeniach. Kto dobrze przygotuje swoją organizację (technologicznie i kulturowo), ten nie tylko dostosuje się do zmian, ale też wykorzysta nowe możliwości, jakie niesie cyfrowa era. Przemysł 4.0 to bowiem nie cel sam w sobie, lecz środek do zbudowania nowoczesnego, konkurencyjnego i odpornego na przyszłe wyzwania biznesu. Jak mówi popularne w branży hasło – „Transform or die”. Warto więc już dziś rozpocząć tę transformację na miarę możliwości swojej firmy, by jutro nie pozostać w tyle. Powodzenia na drodze do inteligentnej, przyszłościowej fabryki!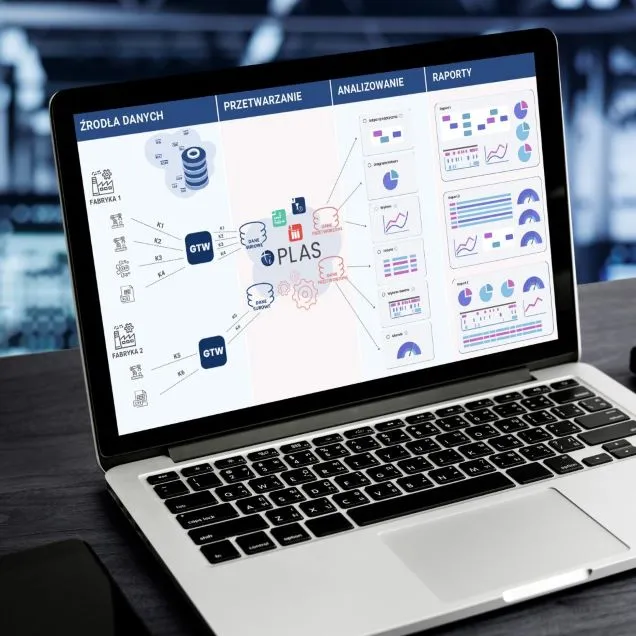
+48 883 366 717