Wstęp
Efektywnie działający proces produkcyjny to jeden z najważniejszych czynników wpływających na rentowność i konkurencyjność przedsiębiorstwa. Jednak niewiele firm może pochwalić się doskonale funkcjonującymi procesami, które odbywają się w halach lub zakładach produkcyjnych. W jaki sposób je usprawnić? Właśnie na to pytanie znajdziesz odpowiedź w naszym dzisiejszym wpisie blogowym!
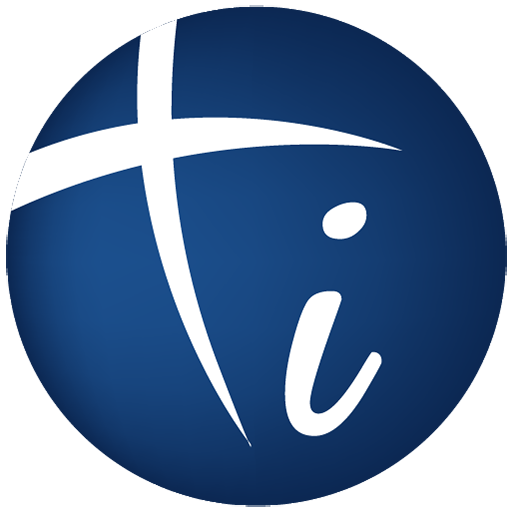
Wstęp do optymalizacji procesu produkcyjnego – kluczowe pojęcia
Przede wszystkim warto zacząć od tego, że pod pojęciem procesu produkcyjnego kryją się wszystkie uporządkowane czynności wykonywane w celu wytworzenia konkretnych produktów. Z jakich rodzajów operacji powinien składać się przemyślany proces produkcyjny?
- operacje technologiczne – to wszystkie czynności, które prowadzą do zmiany kształtu lub innych właściwości tworzonego produktu przez modyfikację jego cech fizycznych, chemicznych, biologicznych lub innych;
- operacje kontrolne – polegają na weryfikacji, czy wszystkie operacje technologiczne są przeprowadzane z przyjętymi przez firmę wzorcami;
- operacje transportowe – czynności, które wiążą się z przemieszczeniem produkowanego produktu;
- operacje związane z magazynowaniem i składowaniem – na tym etapie produkt czeka na dalsze czynności produkcyjne lub zostaje przekazany konsumentowi;
- operacje wspierające – wiele innych czynności dodatkowych.
W kontekście optymalizacji procesów produkcyjnych warto również poznać dokładną definicję pojęć takich jak efektywność operacyjna, marnotrawstwo oraz KPI.
O efektywności operacyjnej możemy mówić wtedy, gdy zasoby są wykorzystywane w taki sposób, aby produkcja wyróżniała się jak najwyższym poziomem wydajności i jednocześnie była realizowana przy minimalnym nakładzie czasu, kosztów oraz energii.
Z kolei marnotrawstwo w produkcji odnosi się do wszelkich czynności, które nie przynoszą wartości dodanej dla produktu końcowego. Należą do nich np. nadmierne zapasy, opóźnienia, przestoje maszyn, nadprodukcja, nadmierne przetwarzanie, wady i odrzuty.
KPI to skrót od Key Performance Indicators. Są to kluczowe wskaźniki efektywności, które mierzą postępy i wyniki w produkcji. Przykładowe KPI obejmują wskaźniki takie jak:
- wskaźnik wydajności pracy (OEE),
- wskaźnik czasu cyklu,
- wskaźnik jakości,
- wskaźnik zużycia surowców.
Diagnoza procesu produkcyjnego – jak zidentyfikować obszary do poprawy?
W celu przeprowadzenia wartościowej i dokładnej diagnozy procesu produkcyjnego należy uzbroić się w cierpliwość oraz wyznaczyć do tego zadania najbardziej odpowiedzialne i zaangażowane w rozwój firmy osoby.
Pierwszym krokiem będzie szczegółowa analiza każdego etapu produkcyjnego. Sprawdź, ile czasu zajmuje cały proces (od momentu rozpoczęcia tworzenia produktu aż do chwili, gdy zostanie dostarczony do klienta) i dowiedz się, jakie narzędzia są niezbędne do jego przeprowadzenia. Zwróć również uwagę na czas taktu (czyli średni czas pomiędzy rozpoczęciem tworzenia pierwszej i kolejnej sztuki produktu zgodnej z oczekiwaniami klienta) oraz na ewentualne marnotrawstwa.
Dzięki pogłębionej diagnozie procesu produkcyjnego będziesz mógł zidentyfikować obszary wymagające usprawnienia. Być może przyczyną niskiej rentowności produkcji są zalegające na magazynie półprodukty lub przestarzałe maszyny, które często ulegają awarii? W zależności od źródła problemu masz do wyboru kilka metod usprawniających czynności odbywające się na produkcji. Dowiedz się więcej o najpopularniejszych sposobach zarządzania jakością w przedsiębiorstwach i wybierz metodę odpowiednią dla Twojej firmy.
Lean Manufacturing, czyli redukcja marnotrawstwa w produkcji
Metoda Lean Manufacturing, znana również jako Lean Production lub Lean Management, jest podejściem do zarządzania produkcją, które ma na celu eliminację marnotrawstwa i ciągłe doskonalenie procesów. Jednym z głównych aspektów Lean Manufacturing jest skupienie się na zidentyfikowaniu i redukcji różnych form marnotrawstwa w procesie produkcyjnym.
Marnotrawstwo w produkcji odnosi się do wszelkich czynności, które nie dodają wartości dla klienta końcowego. Może to obejmować nadmierne zapasy, nadprodukcję, opóźnienia, odrzuty, nadmierną obróbkę lub pracę czy nieefektywny transport materiałów. Wszystkie wymienione formy marnotrawstwa generują straty czasu, energii, zasobów i pieniędzy.
Metoda Lean Manufacturing zapewnia ramy i narzędzia, które umożliwiają identyfikację i eliminację marnotrawstwa, prowadząc tym samym do zwiększenia efektywności, jakości i rentowności produkcji.
Six Sigma – poprawa jakości i spójności w produkcji
Metoda Six Sigma jest podejściem do doskonalenia jakości, które ma na celu minimalizację błędów i odchyleń w procesie produkcji. Koncentruje się na eliminacji defektów, co przekłada się na poprawę jakości końcowego produktu.
Six Sigma opiera się na precyzyjnej analizie danych i statystyce, wykorzystując przy tym narzędzia i techniki takie jak: DMAIC (Define, Measure, Analyze, Improve, Control) do ciągłego doskonalenia procesów. W ramach tej metody zespół specjalistów identyfikuje kluczowe obszary procesu produkcyjnego, które wymagają poprawy, a następnie stosuje odpowiednie narzędzia do redukcji defektów i optymalizacji procesu.
Metoda Kaizen – ciągłe doskonalenie procesu produkcyjnego
Kaizen, w kontekście usprawniania procesu produkcyjnego, jest szczególnie wartą uwagi metodą, ponieważ jej założenia opierają się na ciągłym doskonaleniu i szukaniu usprawnień.
Podstawą tej koncepcji jest zaangażowanie wszystkich pracowników, niezależnie od ich stanowiska i szczebla, w nieustanne poszukiwanie sposobów i pomysłów doskonalących wszystkie obszary firmy. Uznaje się, że to właśnie pracownicy są najlepiej zorientowani w codziennych operacjach i mają wiedzę na temat obszarów, które wymagają ulepszenia. Stosowanie Kaizen promuje partycypację pracowników, zachęcając ich do dzielenia się pomysłami, wnioskami i sugestiami dotyczącymi doskonalenia procesów. Dzięki temu wszyscy pracownicy czują się zaangażowani i odpowiedzialni za jakość i efektywność produkcji.
Metoda Kaizen stawia na zrównoważony, stopniowy rozwój, który przyczynia się do trwałego sukcesu i doskonałości w procesach produkcyjnych.
Rola technologii w optymalizacji produkcji – automatyzacja i cyfryzacja
Nie da się ukryć, że nowoczesne rozwiązania technologiczne stale zmieniają nasze życie prywatne oraz rzeczywistość wielu firm. Mając bowiem do wyboru przykładowo zmywarkę i ręczne mycie naczyń, zdecydowana większość osób wybierze pierwszą opcję. Najważniejsze powody? Oszczędność czasu, energii oraz pieniędzy (dzięki zastosowaniu np. programu eco), a w efekcie domownicy mogą korzystać z czystych naczyń.
Podobny tok myślenia możemy przełożyć na codzienność hali produkcyjnej. To oczywiście ogromne uproszczenie, ale rozważmy kwestię gromadzenia i analizy danych. Jeśli zdecydujemy się zaangażować w tę czynność jednego z pracowników, będzie to od niego wymagało ogromnego skupienia oraz poświęcenia dużej ilości czasu, a i tak ryzyko, że popełni on błąd, pozostaje wysokie.
Z drugiej strony ten obszar, wpływający bezpośrednio na optymalizację procesów produkcyjnych, można w całości zoptymalizować. Przykładowo system IPLAS umożliwia pobieranie i analizowanie danych, a następnie ich wizualizację z wyszczególnieniem informacji, na które szczególnie powinno zwrócić się uwagę. Początkowa inwestycja w automatyzację zwróci się w przyszłości, ponieważ specjalista może zostać przydzielony do ciekawszych i bardziej angażujących zadań, a właściciel firmy zyska rzetelne i prawidłowe dane, na podstawie których będzie podejmował biznesowe i strategiczne decyzje.
Kultura i szkolenia pracowników jako element optymalizacji produkcji
Inwestowanie w rozwój pracowników wymaga od pracodawcy odwagi, ponieważ nie jest on w stanie przewidzieć, czy zatrudniona osoba nie podejmie nagle decyzji o zmianie pracy. Jednak należy podkreślić, że dobrze dopasowane szkolenia uczą pracowników efektywniejszych metod działania, co w przyszłości zaowocuje znacznym wzrostem ich wydajności. Dodatkowo warto zdawać sobie sprawę z tego, że wielu pracowników odchodzi z firm nie tylko z przyczyn finansowych, ale równie częstym powodem zmiany miejsca zatrudnienia jest brak możliwości rozwoju. Nawiązując zatem do wymienionej na samym początku akapitu obawy pracodawców – uczestnictwo w kursach może zmniejszyć rotację pracowników.
Na rynku jest dostępnych wiele szkoleń z rozmaitych metod optymalizacji procesów produkcyjnych. W przypadku dużych zakładów produkcyjnych niezwykle istotne jest, aby menadżerowie oraz liderzy dokładnie zapoznali się zarówno z teorią wybranej metody, jak i jej zastosowaniem w praktyce. Następnie uzyskaną wiedzę przekażą pracownikom z ich zespołów, dzięki czemu cała firma będzie aktywnie pracować nad optymalizacją produkcji i ciągłym doskonaleniem wszystkich czynności związanych z tym procesem.
+48 883 366 717